3 September 2010
Electrical design and manufacturing.
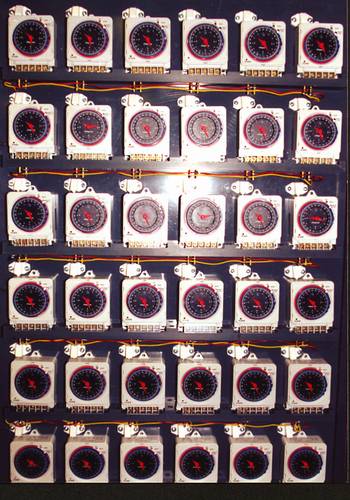
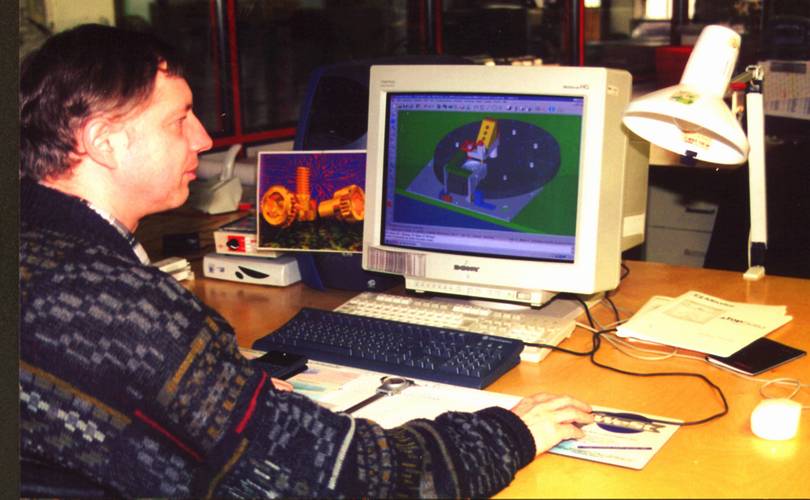
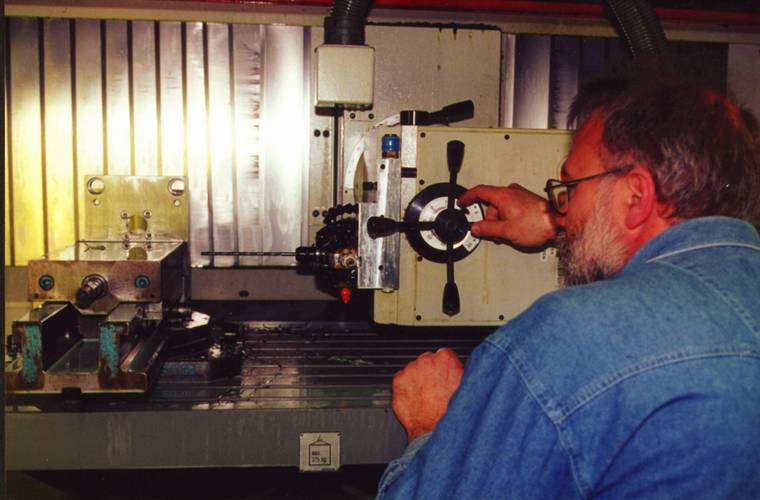

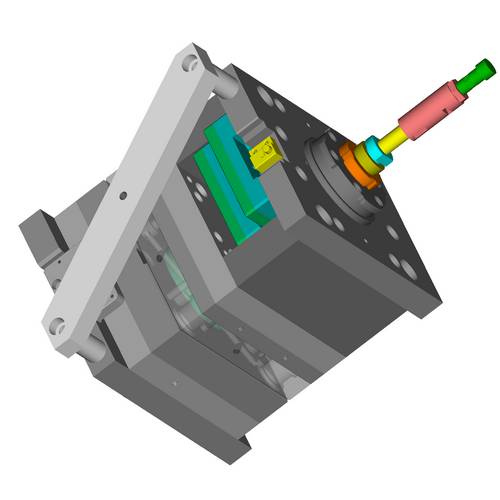
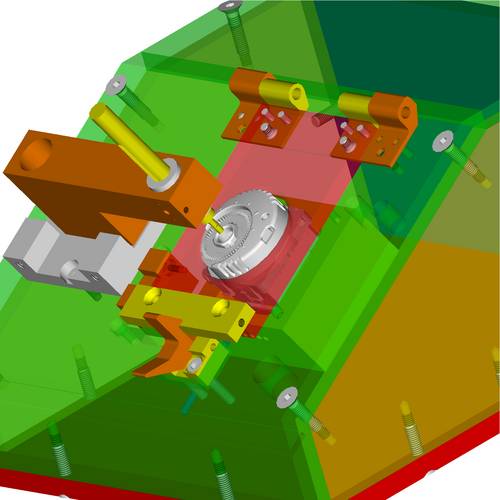
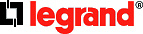
TopSolid and Legrand GmbH
Companies with a high level of in-house production are often tempted into making convenient compromises for the sake of an integrated system environment. This includes using the same CAD system for both product development and tool making. However, using different systems may prove to be more cost-effective and rational, as long as the switch is made at the correct place in the process chain. Thus, the German subsidiary of the French electrical manufacturer Legrand, which uses a popular 3D CAD system to develop their products, has been able to considerably shorten their turnaround time by implementing Missler Software’s end-to-end CAD/CAM solution for both tool making and production resource design.
Legrand is a Group which operates across the globe, employs more than 23 000 people and has consolidated annual sales of 2.9 billion euros (for the financial year 2004). Legrand supplies electrical fitters with just about everything electrical for homes, offices and factories across the globe. Their range of products includes switches and sockets, dimmers, motion and light sensitive switches, remote control systems and building technical systems, distribution boards and the appropriate equipment, switching cabinets, transformers and industrial power sockets as well as electrical chimes, intercom systems, emergency lighting and alarm systems. Despite this wide range, Legrand sells all its products exclusively to specialist stores.
The German subsidiary of Legrand was founded in 1970 in Ratingen and merged, eight years later, with WEG Westdeutschen Elektrogerätebau which was based in Soest. Today, the small town in Westphalia is not only home to the sales center for the German market, it is also a modern production plant for products developed in Germany. Within the Legrand Group, Legrand GmbH is responsible for the development and manufacture of the Rex time switch system and other components for building automation systems. This includes the design and manufacture of tools and production resources.
Shortening turnaround time
The success of Legrand is very much determined by the building industry which has suffered in recent years. In order to be able to compete successfully in this market, under these conditions, the company must be able to offer a higher quality at lower prices and make use of every possible opportunity to save money. And tool and production resource manufacture has also been forced to play its part in this process. "As far as the complex tools are concerned, we can boast a reduction in turnaround time from 20 weeks down to 12", says Erhard Lorenz, responsible for tool making in Soest.
The use of a universal 3D CAD/CAM solution in tool development was one of the most important criteria for this, as Legrand is currently required to concentrate more and more on complex surfaces. The tool design team introduced the first 3D workstation as early as 1996. This station used the same 3D system as is used for product design throughout the Legrand Group, and tool design was considering introducing another workstation of this type. This created more and more 3D data flowing into the tool making process, which could not be processed and evaluated optimally. "We then out-sourced the creation of NC programs for the first 3D electrodes", recalls Martin Drebber, milling expert.
5 years ago, and with this background in mind, the tool makers set out to find a 3D CAM system to replace the existing 2 1/2D solution. At the suggestion of the French parent company, which has a say in investment decisions, one of the solutions tested was the TopSolid’Cam software from Missler Software based on the product TopSolid, a combined surface/solid modeler.
Transition to 3D in one go
However, the main reason for choosing the French software package was not due to the influence of the parent company, but based the decision of the tool designers in Soest not to develop the existing CAD installation, but instead to set up 3 workstations using the 3D software from Missler Software. "The financial investment allowed us convert all tool and production resources design to 3D simultaneously", explains Michael Wendel, who is responsible for tool design. It was not just the cost-effectiveness of the product that impressed the users at Legrand, but more the advantages of having an unbroken process chain, from tool design through to the finished part. The strengths of the solution can be attributed to the combination of TopSolid’Mold and TopSolid’Cam, a fact that both Erhard Lorenz and Michael Wendel are only too happy to confirm.
At the end of 1998 Legrand purchased three TopSolid software licenses for the tool design department, and two licenses for the mold-making package, TopSolid’Mold, which were installed under Windows NT on three PC workstations. At the same time the tool making department received two TopSolid’Cam workstations. The hardware used by the tool making department consists of two Compaq computers which are more than suited to the somewhat rougher working conditions, since these two CAM workstations are located very close to the actual processing stations. The tool design department uses two SGI NT platforms and one HP machine.
Satisfied with support
The users at Legrand are fully satisfied with the support provided by their local German distributor, West GmbH. "The concept of complex surface milling was new territory for me as well. At first, it was extremely helpful to be able to simply send a file over to Saarbrücken and to discuss the problem on the phone to find out the right parameters and strategies required to achieve the optimum result," explains Martin Drebber. The distributor, WeSt GmbH, has a wide range of CAM expertise and not only wrote the post-processors for the processing stations at Legrand, but they also optimized these to suit the requirements of the users. This optimization included, for example, the implementation of special functions such as the switching of compressed air for cooling.
Tool design is team work
The original 3D license in the tool design department is still used to convert CAD models from product design into IGES files and to post-process them should problems occur during conversion. In 95 percent of cases, the transfer of data to TopSolid works perfectly, as Wendel says, and if not, then gaps between surfaces can often be closed by modifying the tolerance settings.
TopSolid'Design or TopSolid’Mold are then used to create a tool out of the component geometry. But before this can be done, the designers and the tool makers must sit down together and specify the following details: the general make-up of the tool, the orientation of the component in the mold, the part line, the location of the injection nozzles and the side the object is to ejected, the position of the ejector pin and the slide assemblies, insofar as the use of undercuts makes the latter necessary to eject the object from the mold. The product designers may also be called upon to indicate how it may be possible to simplify the tool by modifying the component that is being manufactured. During tool design, the designers must take into account which machines are to be used to form which components. "Obviously, it makes a difference whether I want to mill or wire EDM an insert", explains Erhard Lorenz.
The TopSolid’Mold software provides a multitude of automatic functions which makes designing tools a lot less complicated. The program is able to calculate the shrinkage of a model, optimize its position within the mold and to calculate part lines and areas that would not be ejected from the mold. The design of moveable function groups such as slide assemblies and mold locks can be simplified by the definition of parametric relationships between the elements of an object. The software also automatically checks the component and other elements of the mold for collisions, a function which provides the user with a high level of confidence particularly when designing a cooling circuit.
At Legrand, these automated functions are either not used, or are only used selectively, as the users have many years experience. "You simply know how a particular plastic behaves at a particular temperature and define the shrinkage rates according to that", explains Michael Wendel. He is particularly impressed by the excellent support for standard objects and normalized parts. To this end TopSolid’Mold provides an extensive 3D library containing components from Hasco, Strack and other respected manufacturers. The company-specific standards already created in the parametric CAD system were easily transferred to the new system using the IGES interface.
Design evaluation
Many of the important parameters required for subsequent processing are already defined at the tool design stage in the form of so-called Features and can thus be evaluated automatically by TopSolid’Cam. "A drilled hole with a tolerance of 10H7 is actually recognized as such. This means that the system knows that it is to center the drill, drill a two tenths pilot hole and then finish using a reamer. I no longer have to define the individual processing steps myself", explains Martin Drebber. The system is even able to automatically recognize and process pockets. These functions are particularly advantageous when making subsequent modifications to the tool, as the drilling and milling programs can be updated at the touch of a button.
Since Legrand does not produce preproduction series or specimen tools, each of the tools made is in fact a prototype. This means that it may be necessary to make modifications to a finished tool, because the part does not fall out of the mold first time or does not have the required quality. It may also be necessary to increase, for example, the wall thickness of the component or a radius in order to improve the filling process. TopSolid’Cam recognizes immediately, by referring to the tool geometry, that a modification has taken place and is thus able to immediately begin calculating the new tool paths.
The CAM software makes it possible to store relatively complex processing cycles in the form of a program that can be called up at any time, as and when required. "For example, I have written a drilling process which tells the system that when it is using a size 10 drill to drill to a depth of 20 millimeters, it can carry out the process in one movement. After 20 millimeters the system moves on to another cycle and removes the chips", explains Drebber. "I can also define filters which make it impossible to select the wrong tool to process a particular workpiece or material." Drebber has also been able to store tool-specific processing parameters in the tool library, for example, cutting depth, cutting speed, feed per tooth.
Speeding up milling programming
Thanks to the automated features, Drebber estimates that actual time taken to create the milling programs using the new 3D system is up to 80 percent quicker than using the previous system. And he only needs half the time to create the drilling programs. "You also save time up front, because a 3D model makes it easier to see how to process the piece, whereas with a drawing you first have to work it all out." According to Wendel, the speed advantage gained during tool design is achieved mainly by the fact that the 2D drawings for tool making can be derived almost immediately and that, at least for the milling pieces, it is no longer necessary to specify as many dimensions.
The turnaround time from starting the tool design process through to the production of the first specimen part has been reduced considerably as a result of the end-to-end CAD/CAM system, despite the fact that the actual processing at the machine is not yet much quicker. As a result, the tool makers have since introduced an additional piece of software designed to optimize feeding and have also purchased a high-speed spindle which allows them to run the processing stations at higher speeds. "This is, to a certain extent, a makeshift solution as we are not yet able to use the potential of a high-speed milling machine to the full", says Erhard Lorenz. "We want to try and make sure that in the future everything is hard milled to reduce the need for erosion."
The implementation of the new CAM software makes it possible to mill sample parts for functional testing within a reasonable amount of time. "In the past, a specialist sample maker would have required 150 hours to put together a complex plastic housing. Using the 2 1/2D system it still takes three days to create the milling program. If we use the 3D system, we only need two hours to create the program, but the machine still requires 5 hours milling time", says Erhard Lorenz. However, recently the trend has moved towards fewer and fewer sample parts being created in this way, because in many cases a stereolithographic model is sufficient.
In the production resource department, the implementation of the new CAD/CAM system is most noticeable when it comes to making use of stored sequences, which in turn makes the design process quicker because you are able to reuse pieces that have already been created. It is very difficult to compare the current situation with the past as Reinhard Fastnacht, who designs production resources for Legrand, goes on to explain. "Complex units, such as indexing plate workstations, were never completely drawn up in 2D, but instead as individual parts and then completed in the fitting shop. Now the fitters receive the parts ready to go, and all they have to do is to put them together." This not only halves the time taken to assemble the components, but also ensures that all future assembly stations are structured in this way.
The use of the TopSolid solutions at Legrand has led to a wide range of benefits which have more than outweighed the theoretical disadvantages of a heterogeneous system environment. The additional system administration work is under control, thanks to the uniform operating system environment, and even the data conversion effort required at the transition between product design and tool design has been kept to a minimum.
Photos BG Concept Marketing Communication
Potřebujete více informací