23 August 2010

Selecting a specific niche market, producing in small batches, and meeting the particular requirements of local customers—this is the key to making Belgian SMEs successful.
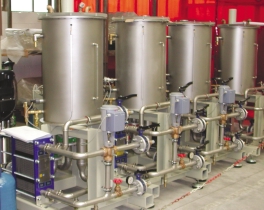
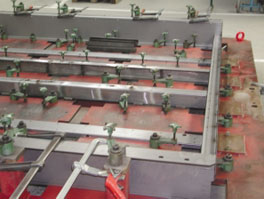
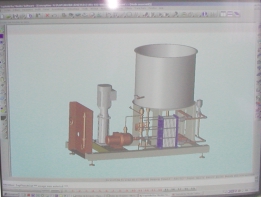
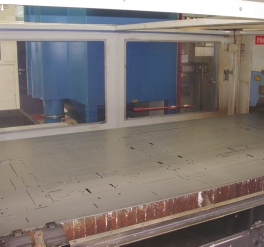
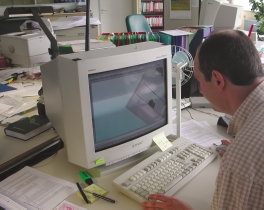
Selecting a specific niche market, producing in small batches, and meeting the particular requirements of local customers—this is the key to making Belgian SMEs successful. “Local” for us means of course “European”. SMEs therefore are forced to invest in new technologies that give them a competitive advantage on the market and enable them to face the competition arising in the new EU countries with lower wages and therefore reduced production costs.
This, at least, is the vision of Nathalie Celis, Managing Director of Garnimetal. Garnimetal, a traditional family company based in the Belgian town of Wavre and specializing in sheet metal manufacturing, is about to celebrate its 80th anniversary on December 20, 2004. A few months ago, the CAD department at Garnimetal was brought up to date when the company purchased a set of solutions by the French software manufacturer Missler Software: TopSolid, TopSolid’PunchCut (comprising TopSolid’Punch, a CAM software for piloting punching tools that also includes the post-processors required for machine preparation and TopSolid’Cut, a CAM solution for laser cutting). Another item on Garnimetal’s 2004 investment agenda is the purchase of a new laser-cutting machine to allow processing at a higher speed, but the company is still waiting for the right offer. A critical requirement at Garnimetal is the integration of its production environment with the Missler Software range of solutions: TopSolid’PDM (Product Data Management, for the management of projects, drawings, documentation and other files) and TopSolid'Erp (management of all company activities using an Oracle database and a defined feedback of production data). The French magazine “Industrie Technique et Management” has spoken to Nathalie Celis, Managing Director of Garnimetal, and to Luc Cornelis of 4D Services, distribution partner for Missler Software’s CAD/CAM/ERP solutions.
Sheet metal manufacturing
Garnimetal is a small enterprise: 25 of its 30 employees work on the shop floor, another four in the design department. In 2003, the company turned over an approximate 2.5 million Euros. Garnimetal was founded in 1924 as an industrial joiner’s shop, mainly manufacturing seats for passenger ships and trains. The original wooden frames were later replaced by a lighter aluminum frame structure. Consequently, metal machining became increasingly part of the Garnimetal portfolio. In 1974, the company gave up its joinery branch altogether and focused exclusively on metal working. The management systematically invested in suitable machinery, first in punching machines and later in a laser-cutting machine and the bending presses and welding stations needed for further processing. Today, Garnimetal offers tailor-made or small quantity products made of steel, stainless steel, aluminum, copper, brass, tantalum or titanium with thicknesses ranging from 0.2 to 15mm. Garnimetal’s customers come from a variety of industries: electronics assembly, train equipment (e.g. engine casings, control cabinets), security devices (e.g. booms, turnstiles for access control), medical, clean room technology, industrial kitchens in inox. Most of Garnimetal’s customers focus on final assembly and have therefore outsourced sheet metal manufacturing to external suppliers.
3D to 2D
Parts are either derived from drawings or are developed in cooperation between the client and Garnimetal designers. The company prefers and actively looks for market niches with tailor-made jobs or customizations that require the supplier to be located close to the client site. Batch production orders, on the other hand, are increasingly outsourced to EU countries with lower wage levels. This trend has become increasingly apparent over the last few years. The company has invested in NC machines, and a special CAM software solution for sheet metal design, 3D Catalpa, (which has since this time become TopSolid’PunchCut) has been in use at the design department for over 10 years. A crucial requirement for sheet metal design is the inclusion of functions that allow the creation of 2D flat patterns from the 3D part model and the fast and efficient generation of CAM programs for use on punching and laser-cutting machines. Catalpa provided this functionality: the Garnimetal designers can create the 2D production drawings from the 3D model and use them to set up the CAM solution for controlling the punching and laser-cutting machines. Many of the current—allegedly repetitive—orders are actually a sequence of individual small-sized lots: The parts to be manufactured are similar, but each follow-up order requires modifications. The changes required are sometimes minor: a different hole diameter to facilitate assembly, a slightly larger or thinner edge, and so forth. One of the drawbacks of Catalpa at the time was the repetition of tasks if any modifications needed to be carried out. Each part modification required the generation of a new 2D drawing from scratch and subsequent operations required for the generation of the ISO code. Following the merger of Missler Software with Catalpa a new generation of integrated sheet metal CAM software, TopSolid’PunchCut was born. TopSolid’PunchCut is a fully integrated solution which optimizes the sheet metal manufacturing process and in particular improves the creation of flat patterns from the 3D model to 2D sheets for punching and laser-cutting. In addition to being a fully integrated solution TopSolid provides an architecture with full interdependency. This means that any change to a parameter (e.g., a different hole diameter) that is applied in any of the three phases of development (3D, 2D, or CAM) can easily be leveraged to the other phases without further work— This eliminates unnecessary repetition of tasks, thus enabling the operator to continue work on a project instead of starting over again and again.
A learning process
The solution has now been in use for three months, it is of course difficult to exactly quantify the benefits. Each project still requires the creation of the database and the components, some of which can later be reused thanks to parameterization. Getting familiar with TopSolid usually requires a 5-day training for first-time users. Garnimetal decided to conduct a 3-day training, with another 2 days to follow later when the users had gathered some actual project experience with the software. The follow-up trainings have already been scheduled. TopSolid’PunchCut operators receive an additional 8-day initial training on Missler Software’s CAM solutions. They, too, will be given another 2 days to further optimize their use of the software. Garnimetal is supported by 4D Services and directly by Missler Software’s French headquarters, when necessary. A case in point for this seamless cooperation is Missler Software’s help with selecting the right laser-cutting machine. Testing of such machines normally requires a variety of CAM programs, but purchasing all post-processors was out of question. Missler Software was able to help out by providing Garnimetal with the ISO code for various laser-cutting machines, which allows for easy benchmarking and subsequent comparison of each machine’s performance. The programs were requested on a Thursday — and were already available the following Monday.
Necesito más información
UNA PREGUNTA SOBRE NUESTROS
PRODUCTOS O SOLUCIONES?
Encuentre su punto de venta más cercano Contacte con nosotros Obtener un presupuesto