28 February 2012
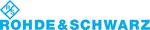
Companies that manufacture highly complex parts in small unit quantities need reliable NC programs. This is why Rohde & Schwarz decided to replace its existing programming environment for milling and turning with the integrated TopSolid CAD/CAM system from Missler Software.
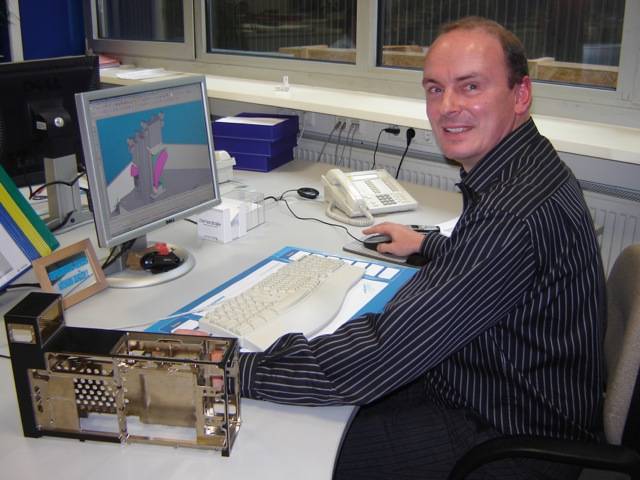
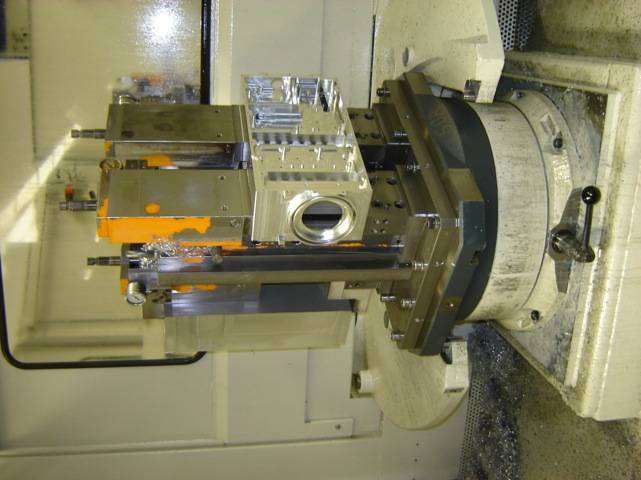
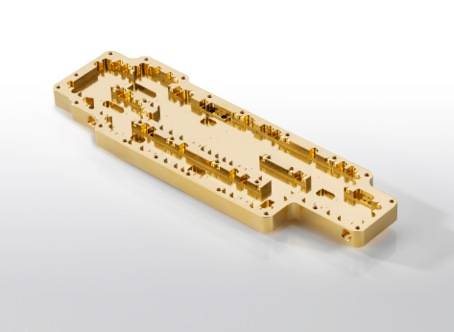
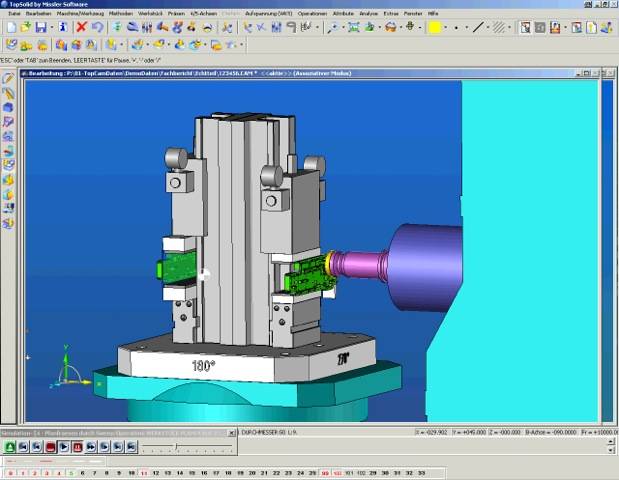
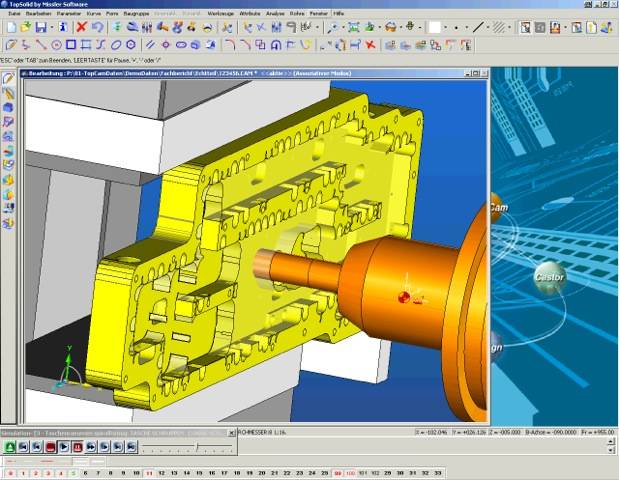
The electronics company, Rohde & Schwarz, is a leading solutions provider in the field of test & measurement technology, broadcasting, radio monitoring and location, and secure communications. Having been founded over 70 years ago, this independent company has a worldwide presence with its services and a tightly-knit service network in over 70 countries. With a headcount of 7200 employees, the company has annual turnover figures of more than €1 billion. The company has its head office in Munich.
Wireless communication marches inexorably onwards. From internet access through W-LAN to Bluetooth headsets for mobile phones, wireless transmission is everywhere. To prevent any "unwanted interference", Rohde & Schwarz manufactures testing and measurement devices with which the manufacturers of radio communication systems can test and calibrate their products. Alongside testing and measurement technology, the internationally active electronics company produces equipment for radio communications, broadcasting and TV technology. For example, Rohde & Schwarz makes transmitters for digital terrestrial TV. "It's a booming market," says Paul Hauner, in charge of the CAM application for machining on the Teisnach site.
The Teisnach plant, home to over 1100 skilled personnel, is the Rohde & Schwarz Group's service centre for mechanical and electronic manufacturing. Here, in the Bavarian Forest, not only are the housing components and PCBs produced for the company's own products, but complex components for the customers are also manufactured. The service scope of the manufacturing specialists extends from equipment design through manufacturing and surface coating to the assembly of mechanical subassemblies, electromechanical systems and special machinery. These include TV transmitters for customers worldwide, which are assembled in Teisnach.
One CAM system for many CAD systems
The product developers of Rohde & Schwarz are based on the Munich site and work with the I-deas software from Siemens PLM Software (previously UGS), which is shortly to be replaced by its successor system, NX. Their colleagues in the manufacturing department in Teisnach, who handle all preparatory activities for manufacturing, including NT programming, do not however only have I-deas data to process. In tool and mould manufacturing, Autodesk Inventor is used, and from external customers they receive components that have been designed with Pro/Engineer, Catia or SolidWorks. "For this reason, we needed a CAM solution with good interfaces," says Mr. Hauner.
CAD data has been used in Teisnach since the 1980s for NC programming. This makes the manufacturing specialists capable of manufacturing even the most complex parts, with little drawing information, while guaranteeing process reliability and high quality. They generate drilling and milling programs with Exapt Plus, while the situation in terms of turning is somewhat more heterogeneous. In part, the operators program directly on the machine, sometimes using a machine-oriented programming tool or a help editor, which makes it difficult to transfer parts on to another machine. The machine pool in Teisnach consists of approximately 25 milling machines and 17 turning-drilling-milling centres, the performance scope of which could not be fully exploited to date on account of insufficient programming functionality.
Yet not only the machines themselves, but also the parts to be machined are becoming increasingly complex. Rohde & Schwarz therefore needed a CAM solution with high-performance simulation functions: "We wanted to have a constantly updated raw part and be able to simulate the machine situation down to the minutest details, not least because multiple-axis machines are very collision-prone," says Mr. Hauner. Always to be borne in mind when representing the manufacturing environment on the computer was the need to improve the documentation and reproducibility of the processes. The programmer should no longer be able to deploy a tool that is not available in the workshop or use jigs for which there exists no design documentation.
Thorough search for the right CAM software
Rohde & Schwarz took plenty of time in selecting its system. The three-man project team, comprising two experienced NC programmers alongside Mr. Hauner, first of all analysed the CAM requirements and drew up a shortlist of the systems and manufacturers concerned. The remaining candidates were invited in 2005 to a two-day benchmarking session, during which they demonstrated the performance capabilities of their systems on the basis of typical work pieces and taking account of the existing machines and machine processes. TopSolid emerged as the clear winner of this benchmarking! The decision in favour of the system was confirmed by a six-month test phase with two high-end machines for milling and turning, in order to be able to test the entire requirements spectrum under production conditions.
An extremely important requirement of the NC programmers was good support for change processing, as Mr. Hauner says: "With us there is no special prototype manufacturing. In order to guarantee problem-free production start-up and keep the costs under control, we manufacture both prototypes and mass production parts in mass production quality. This means that as from the very first run, a great deal of manufacturing know-how goes into the processing, which we do not wish to lose in the event of any design changes. We need to integrate these changes quickly and channel them with process reliability into manufacturing."
Updating the NC programs
TopSolid won us over not only by its unsurpassed functionality for turning and milling, but also by being at least on a par with the other systems when it comes to change processing. The design module can operate with many CAD formats and also offers the possibility of modifying imported files, for example in order to displace an edge, if the designer has not centred the tolerances. For a parametric system, this is by no means a given," explains Mr. Hauner. Design errors are in any case cleaned up in the source system, because otherwise it would be a matter of continually making improvements to the components in the event of changes being made.
At Rohde & Schwarz, it is fairly common for components to be modified during job preparation. In these cases, the NC programmers can load the new component version in TopSolid’Design and see just what has changed with the aid of the geometry comparisons function. This is something that cannot always be determined unequivocally from the change notifications, as Mr. Hauner goes on to explain: "A particular strength of TopSolid’Cam is its replace function. This allows you to apply the new geometry to an existing NC program and update the machining in the ideal case at the touch of a button. If the form of the component has been significantly changed, or if new features have been brought in that the NC program does not yet know, the programmer must of course intervene interactively."
A decisive criterion for choosing TopSolid was the possibility to associate the CAM solution with the Walter TDM resources management tool, which was to be introduced in parallel with the new CAD/CAM solution. Although Rohde & Schwarz was not procuring any equipment requiring the manufacturer to prepare CAD data in a coordinated format, the representation of the existing equipment and the linking of the TDM system with TopSolid’Cam involved considerable expense. This meant that the passage of the CAD/CAM solution into productive operation was somewhat delayed.
Happy with the choice of partner
In order to have a single interlocutor in the event of interface problems, Rohde & Schwarz placed the responsibility for the coupling of TDM and TopSolid in the hands of the Missler Software sales partner, Adequate Solutions, who also implemented the CAD/CAM solution in Teisnach. The Lahr-based systems vendor was singled out following the choice of the CAD/CAM solution as the competent partner with regards to adaptation of the post-processors and the linking of the complex complete machining centres. "We are thoroughly satisfied with the system decision and the choice of partner," assures Mr. Hauner.
During the test phase, the three members of the project team were trained in several workshops that lasted between two and three days. The training took place in-house, so that the operators could quickly put into practice what they had learned. "TopSolid is a very powerful system, and is therefore not suited to operators who only work sporadically. It takes time to get really up to speed with it," says Mr. Hauner. "We can therefore say with some certainty that we are still not fully exploiting the performance possibilities of the software."
The operators have been pleasantly surprised to see how practically-oriented the milling strategies that the system proposes are. This also applies for HSC milling. The automatisms available are most welcome, even if they do not replace the know-how of the operator, who may sometimes have to choose a different strategy or machining sequence in order to avoid delay in work piece production. These are aspects that cannot be simulated on the computer. The operators are not yet making use of the possibility of defining reusable machining cycles for certain geometry elements (e.g., bores).
Flexibility when clamping
When producing their NC programs, the operators begin for the most part with a 3D finished part, from which they generate the raw part geometry - generally an enveloping cuboid - and calculate the stock removal. For this they use a template for which the machine is preconfigured with the appropriate clamping set-up, they clamp the part and they machine it with the tools out of TDM. For classic six-sided machining with machine clamps that move through 180°, there arose the problem of tool sequence optimisation involving several clamps. The CAM system offers little support for this, since it cannot yet know when calculating the tool paths for machining on the first clamp which tools it will later need for the two clamps; for this, it must know the up-to-date raw part geometry from the first clamp. Adequate Solutions has therefore comprehensively adapted the post-processor so that the tools can be used without being changed for both clamps.
TopSolid will be deployed in production by Rohde & Schwarz only partially at first, since the project team is still working on getting the application up and running and developing the methods. Four different machine types, representing approximately half of the machine pool, are comprehensively represented in the CAM software, and calibrated according to the TDM standard. "New machines are systematically represented immediately in the system, with the existing ones being gradually transferred," says Mr. Hauner, "all except the older machines that run with a stable capacity limit, in other words on which, essentially, existing parts are manufactured using existing programs. It's not worth generating their representations in TopSolid."
Considerably shorter running-in times
TopSolid is currently installed in Teisnach on three PC workstations running under Windows XP. More precisely, this involves a network installation with three simultaneously usable licences of TopSolid’Design and the TopSolid’Cam module for 3-axis milling. The TopSolid’Cam turning module has two network licences, and the module for 4 and 5-axis milling has one. For the drilling and milling programs, there are also nine fixed-installation Exapt licenses, which are due to be replaced successively by TopSolid. They are not, however, used from morning till night, since the machine operators also generate NC programs alongside their machining work.
Mr. Hauner estimates that, in the final upgrade stage, Rohde & Schwarz will deploy TopSolid on seven workstations. The intention is to associate the software with the company-wide Teamcenter Engineering product data management system, which already today controls the preparation of the CAD data. Central administration of the NC programs and of all production-relevant information is important for the company in order to ensure traceability at each stage of production design, which Mr. Hauner is keen to stress. He also considers it premature to make any statements, at the current stage of the project, with regard to benefits, even if it has already been clearly demonstrated that the programming and running-in times are considerably reduced: "The objective of the project was to reduce the programming costs by 30% and the tooling and running-in times by 20%. As far as running-in times are concerned, in particular, we are set to significantly exceed these targets." When you consider that the running-in times for complex components can stretch over several working shifts, it is easy to see what these time-savings could mean with regard to machine utilisation capacity.
The programming costs are reduced not only on account of faster NC programming with TopSolid, but also thanks to time saved on searching for tools and production documents. At the same time, TopSolid’Cam leads to better and more reliable NC programs being produced, and thereby contributes to the avoidance of costly errors. Mr. Hauner tells of a case in which costs amounting to several thousand euros were incurred due to the fact that someone had forgotten to document the displacement of a drill hole by two tenths of a millimetre: "In the future, such errors can be detected in time thanks to TopSolid."
Necesito más información
UNA PREGUNTA SOBRE NUESTROS
PRODUCTOS O SOLUCIONES?
Encuentre su punto de venta más cercano Contacte con nosotros Obtener un presupuesto