17 June 2011
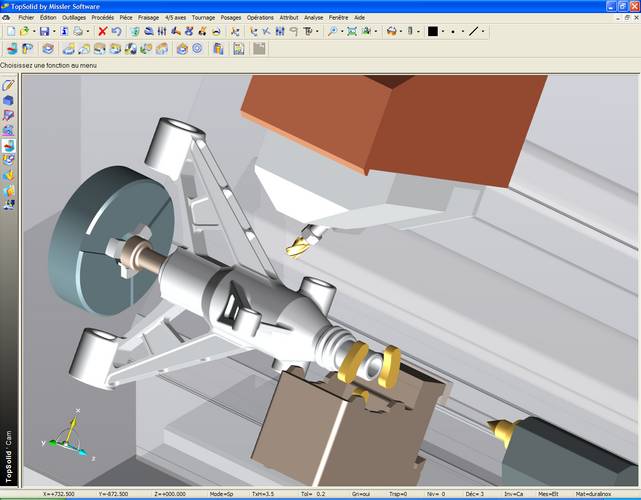
Mill turn machines (or multifunction machines) are increasingly used in today’s manufacturing plants. The reason behind the success of these machines is evident - their capacity to combine milling and turning operations and thereby machine complex parts in just 1 operation considerably reduces preparation times. Often long preparation times lead to high costs especially in the production of small series. In addition mill turn machining guarantees higher precision machining as it is not necessary to machine the part in several operations which implies less handling of the part during the different machining stages. These 2 factors offer a competitive advantage for many small sub-contractors who manufacture very complex, high precision parts in small series of 1-100 parts.
The difficulty to program Mill turn machines
Mill turn machines are often very difficult and complex to program. The multitude of tool turrets, holding fixtures and the complex kinematics of the machine must all be managed by a CAD/CAM software. Mill turn machines are expensive (€250,000 - €500,000 or more), their implementation is complicated and and in many cases these machines need to work 24h a day so that the investment is profitable. The slightest time loss when implementing and using these machines can result in huge financial losses. In other words the machining program must work from the outset!
It is therefore necessary for a company thinking of investing in such a machine to be equipped with a CAD/CAM solution capable of programming all machining processes: turning, 2 axes milling, 3 axis milling, 4 & 5 axis continued milling, 4 & 5 axis continued turning, synchronization and complex simulation. It is also essential to work with a software that is capable of simulating, in a realistic manner, what happens on the machine in order to reduce implementation times, prevent collisions, optimize cycle times, etc.
Strong turning competencies necessary
One of the key competencies of a CAD/CAM software for multifunction machining is its capacity to manage milling and turning. The majority of software solutions on the market today offer very strong milling strategies but are less competent in turning. Missler Software in fact developed very strong experience in turning from early on and today is one of the leading providers of CAD/CAM software for turning strategies. Many TopSolid customers chose TopSolid’Cam because of its strong turning capacities.
With TopSolid’Cam turning operations are carried out as easily as milling cycles. The part is put on a virtual machine and the software proposes adapted machining cycles. In addition, TopSolid’Cam indicates which operations can and cannot be carried out with the chosen machine. This differentiates TopSolid’Cam from other software solutions which do not have integrated simulation capacities. According to Jean-Pierre Lugarini, CAM Development Manager for Missler Software “TopSolid’Cam does not simulate a machine like in some software solutions, it programs a virtual machine which thereby enables the operator to verify and control the tool path during programming.” Another strong point of the software is the possibility to manage the stock so that all machining operations take into account the correct stock model.
Key fonctions in TopSolid’Cam to program Mill turn machines
We have already seen that the CAD/CAM software must be complete in order to program mill turn machines. Below is a list of other essential features a CAD/CAM software must have to successful program these machines:
- Stock management – It is impossible to program a mill turn machine without excellent and real time stock management. With TopSolid’Cam tool paths are calculated for each machining operation based on the stock left behind after previous operations. (It is important not to confuse “stock management” with “machine simulation with material removal”).
- Machine kinematics – TopSolid’Cam’s kinematic engine enables assembly simulation of the machine based on CAD files provided by the machine-tool manufacturer or made using TopSolid’Design (or any other CAD software).
- Simulation and collision management – Thanks to its kinematic engine TopSolid’Cam anticipates collisions and automatically modifies the orientation of tool angles to avoid all collisions between the machine, the tool turret, the holding fixture and the part. In cases where collisions cannot be avoided TopSolid’Cam will not permit the machining of tool paths which cause these collisions.
- Chronogram – The chronogram allows the synchronization of operations which need to be carried out simultaneously. The operator can have a direct input on cutting conditions and operation positions in order to optimize the manufacturing sequence.
- Tool data base - Tool modeling is very important and may be considered as being as important as machine modeling. In order to generate correct simulation results all tools used need to be represented as accurately and realistically as possible. All operators should be able to represent their tool and tool paths in the CAM software. TopSolid’Tool offers a good tool database and responds to the needs of most TopSolid’Cam users. For more detailed tool databases Missler Software has developed interfaces with external databases such as Gedix, Tool Expert and Walter TDM.
- Topological analysis
- Ergonomy
In order to really get the most out of your mill turn machine you need to reunite the following criteria: trained and skilled staff, a well-adapted CAD/CAM software capable of simulating machining operations, good support from the CAM developer who is familiar with the machine tools on the market and is capable of using this knowledge in the software and post-processors that worl. A company that is capable of meeting all of these criteria will benefit from important productivity gains, especially for the machining of complex parts in small series.
Necesito más información
UNA PREGUNTA SOBRE NUESTROS
PRODUCTOS O SOLUCIONES?
Encuentre su punto de venta más cercano Contacte con nosotros Obtener un presupuesto