4 décembre 2015
It’s made of stainless steel with a shiny mirror finish and rises over Lake Como, in front of the well-known Piazza Cavour. We’re talking about the work that an international ‘starchitect’ presented to the city in collaboration with a local association. It was executed by a company from Cantù, Province of Como, facilitated in the planning phases by the simplicity and power of an integrated CAD/CAM solution dedicated to the sheet metal industry.
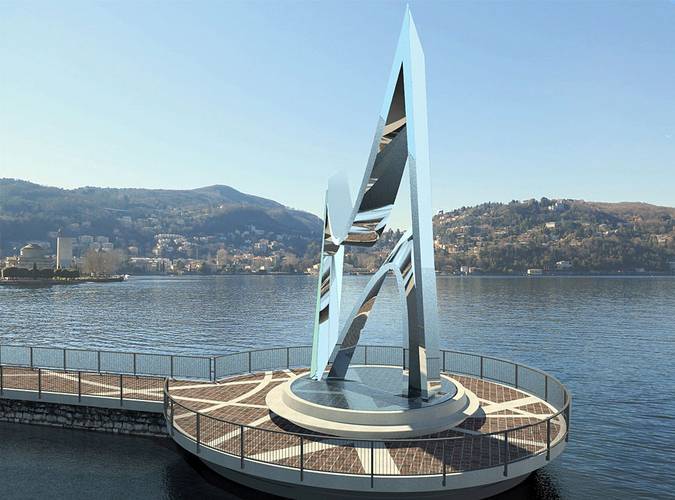

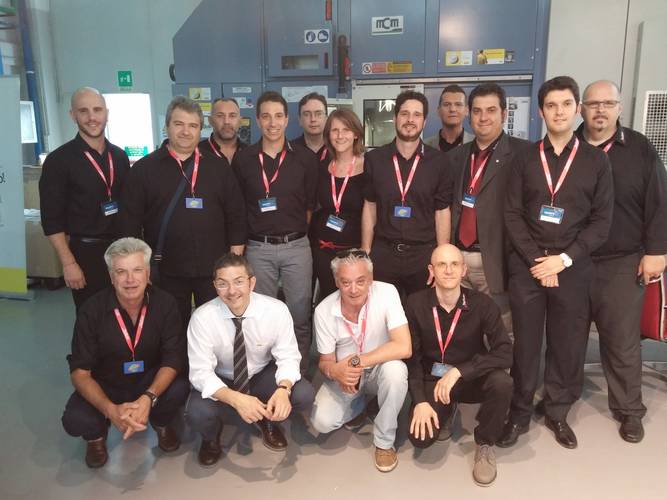
“The Life Electric is inspired by the electrical voltage between two poles of a battery, Volta’s great gift to humanity.” Those were the words expressed by the American ‘starchitect’ Daniel Libeskind who signed the work that he donated, together with the Friends of Como Association from the eponymous city, to celebrate the memory of scientist Alessandro Volta, inventor of the battery, for the 270th anniversary of his birth (1745-1827). A sculpture installation, defined by Albert Einstein as “the fundamental basis of all inventions.” The structure measures over 16 meters high, weighs a total of 270,000 kilos and is divided into five primary elements. These figures are impressive enough when compared to the height of a building (equivalent to five floors) and with the contemporary lightness of the structure towering over the profile of the water. The two steel sinusoids as conceived by Libeskind do not block the magnificent view of the surrounding landscape in any way. Perhaps less poetic was the practical and concrete dimension that enabled it all to be brought together. No stranger to such challenges, it was Metalsistem who took charge of the work. With its headquarters in Cantù, Province of Como, it has, for quite some time now, specialized in satisfying the requirements of designers worldwide that are every bit as elegant as exclusive.
“Over the years,” states Umberto Pratò, co-owner together with Alfredo Bray and Cosimo Deiana, “we have always been focused on special processes that allow us to match a tradition of craftsmanship and innovation with the use and assembly of materials. The pursuit of quality and attention to detail are something of an obsession.”
An operational approach in which the design dimension plays a fundamental role in optimizing time and execution methods, even in relation (for this and other projects) with possible changes during the construction phase, resulting from the ongoing quest for perfection of designers and creatives when it comes to their work. For the design and development side, the company makes extensive use of Missler’s TopSolid CAD/CAM software, which has already been in service for some time now at the company’s technical office.
Integrated project development
The associative and parametric CAD/CAM/PDM Solution, developed on the Parasolid engine, TopSolid from Missler Software was implemented in the Metalsistem technical office over ten years ago. Recently released in the new TopSolid 7.9 version, it offers a hybrid CAD environment for designing parts (solids, surfaces, sheet metal, process plant engineering), together with restraints and mechanisms, working 2D with related separate bases and indexing on several levels, all of it in associative mode. The native PDM controls and automates the interaction between the various users and proper workflow of the product (changes, revisions, usages, replacement parts, etc.). It is also in a league of its own with the features of its integrated and verticalized modules (plastic mold design, sheet metal and die casting). As far as machining operations are concerned, it has become a reference point in machine tool programming (CAM): Milling in 1/2D, 3D 4/5 indexed and continuous axes, multi-axis and multi-task lathing. All told, its power and flexibility are highly appreciated in the modules adopted by Metalsistem as well.
“Developing Libeskind’s work,” Pratò explains, “required careful study in order to obtain the best aesthetic effect over the curves of the structure. In fact, there are no continuous regular flat surfaces, but rather profiles with radii of variable curvatures. The key to the development and good final result is the substructure, used to sustain and to provide a point of support to the sheet metal casing composed of a tubular matrix, namely a cage 20 mm thick, framed in a comb and subsequently welded.”
The internal skeleton thus acts as a primary support for a first “skin” of stainless steel sheet 3 mm thick, upon which the external “skin” of AISI 316 stainless steel sheet with a shiny mirror finish is “glued.” Pratò followed this development step-by-step, taking full advantage of the flexibility of the TopSolid’Design module.
“Clearly, the work depicts a stylized ‘A’ and a ‘V’ (tracing the initials of Alessandro Volta – editor’s note). Pratò continues, “Its creation called for the simple subdivision into 5 different elements, in the order conceived as follows: the first step was to develop the ‘A’ in 3D. I then worked on the two lateral support ‘legs’, to finish with the upper ‘V’, divided in turn into two sections.”
A demanding process in which the technician had to take into account and resolve unconventional development criticalities, in addition to providing for the subsequent transformation of the materials to render the desired aesthetics of the final result.
A synergy of strength and flexibility
TopSolid’s intuitive design, simplicity and processing power allow the technician and designer keep in step with work progress and with a roadmap that is firm and binding.
“A thorough knowledge of TopSolid’s functionalities, procedures and potential,” Pratò emphasises, “allowed me to accelerate considerably, with the certainty that what was reproduced on video would be found with the same corresponding results in the workshop. This is a strong point of no small importance, also in terms of the safety that the installed piece must guarantee.”
In this respect, a few checks of maximum levels were performed with the help of the software and by sending the results to external engineers who subsequently confirmed (and countersigned) the accuracy.
“In other projects,” Pratò continues, “I take full advantage of the functionalities of the software that allow me to manage centers of gravity in real time. It actually understands that, for various reasons, a design must be secured with ‘disguised’ weights to ensure it remains static and stable. Even here, the correspondences are perfect, together with the ability to control changes and adjustments in the course of the work.”
Once the design dedicated to Alessandro Volta was defined, the process thus continued in the workshop with laser cutting of the various component elements of the structure, the welding of the cage (substructure) and assembly of the 5 elements. The first “skin” (3 mm) is attached to the substructure and then the aesthetic outer cladding is attached (also 3 mm).
“Outer cladding,” Pratò adds, “made of steel sheets with a shiny mirror finish, mounted on flat surfaces and welded onto edges to maintain maximum planarity.”
Installed last summer, the work completed was designed to make the most of noble materials with that were used, even during the darker hours. A control system, yet again devised by Daniel Libeskind, manages a performance of short light cycles that simulate the natural variations in color temperature and intensity of daylight throughout the day. A delicate “light show” of biodynamic light created by taking advantage of highly energy efficient LEDs.
More features and improved design efficiency with the new 2015 version
With the release of the TopSolid 7.9 version, TopSolid offers users close to 100 technical enhancements and new features intended to improve the performance of this integrated CAD/CAM/PDM calculation system, making it more effective and flexible for users than ever. It would be impossible to list them all, since they concern all of the modules. In TopSolid’Design, for example, separate Sketch, Assembly Modeling and Draft Creation are the procedures that have benefited for the most part from the contributions of developers from the French software house.
High marks for both the CAM module for 2D (new grinding features with mouse, enhancements and added options for geometric optimization, cycle chamfering and managing buildups), and 3D/4D/5D (including a new isoparametric morphing strategy, enhanced management of buildups and new control inserting negative machining clearances) and Turning (new management of pilot points, enhancements in the machine simulation and new tools for off-center drilling). Meanwhile, the user interface, locking surface, die holders and injection were the parts most improved by the TopSolid’Split and Mold modules.
Where metal takes shape
Metalsistem started out in the metal structural work business in 1995. Over the years, it has become highly specialized in processing stainless steel, brass, aluminum, titanium and pewter, serving the demanding sectors that continue to converge more closely with the highly diversified world of design. With its headquarters in Cantù, at the threshold of Como, directed by its three co-owners, Alfredo Bray, Cosimo Deiana and Umberto Pratò, you can discover their capacity to satisfy the requirements of the food, textile, pharmaceutical, and mechanical industries, even for medium/small volumes and the complex sector of custom furnishings. The development of this phenomenon is ongoing, based on its business of transforming source materials into finished products. The use of technologically advanced equipment and the rich background of some 20 highly qualified people allow it to provide quick and efficient solutions to an ever-growing clientele on the national and international scenes alike. Thanks to its internal design studio, using Missler TopSolid CAD/CAM software, Metalsistem is capable of designing the idea provided by the customer and creating the finished product. The technical office is in charge of the consulting phase for studying in co-design the feasibility of the projects, resolving any criticalities and problem issues, suggesting solutions for improvement or for customizing the order. The lasting and constructive collaboration with many architecture offices allows the company to create products with an exclusive design that are present in art galleries, museums, showrooms, exclusive houses or public places worldwide, as well as the sculpture-installation “The Life Electric”. From the concept through to the finished product and open to new market challenges, Metalsistem maintains complete control over the production cycle throughout the following processing phases: laser cutting, shearing/punching, bending, mig-tig welding, CNC turning and milling through the machining center.
Three decades of change in the world of CAD/CAM/PDM
The Happy 30th Anniversary event was held last July at the Coromant Productivity Center in Milan. Organized by Missler Software Italy in collaboration with Sandvik Coromant, it celebrated our first 30 years of business.
“Missler Software,” explains Diego Moltini, Lombardia Sales Manager, “turns 30 this year. We decided to mark this important anniversary by organizing a unique nationwide event that would also allow us to take advantage of the current release of TopSolid’s 2015 version. Almost the entire Italian staff from the software house was present for the occasion that marked their outstanding commitment in making the preparations over the preceding months.”
With some 80 attendees from roughly 50 different firms, not to mention prominent members of the mainstream trade press who accepted the invitation, the event was a resounding success.
With his careful eye on every detail, the event was prepared with the precious help of Alessandro Oldani, director of the Coromant Productivity Center, together with Diego Moltini. Particular attention was also paid to the preparation of the demonstration processes on CNC machines on which participants were able to appreciate the excellent mix of technology obtained by the TopSolid algorithm and Coromant tools.
“Together,” beams Moltini, “they save a remarkable amount of operating time.”
Besoin de plus d’information
une question sur nos
produits ou solutions ?
Trouver votre point de vente le plus proche Contactez-nous Demander un devis