10 October 2013

Une gestion d’outils efficace permet non seulement d’économiser des frais d’outils, mais également d’accélérer la programmation CNC et de réduire les temps de rodage à condition, bien entendu, que les programmeurs FAO aient accès aux données d’outils réelles. C’est pourquoi Bombardier Transport a construit une solution d’intégration formée de TopSolid’Cam de Missler Software et des solutions de gestion d’outils Tool Management Solutions de Zoller sur son site de Netphen en Allemagne, où sont fabriqués des châssis et des bogies pour matériel roulant ferroviaire.
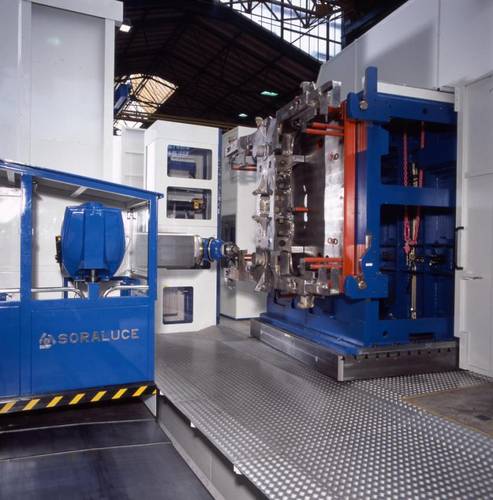
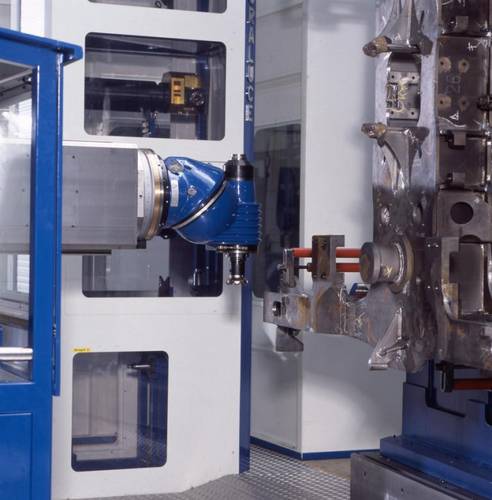
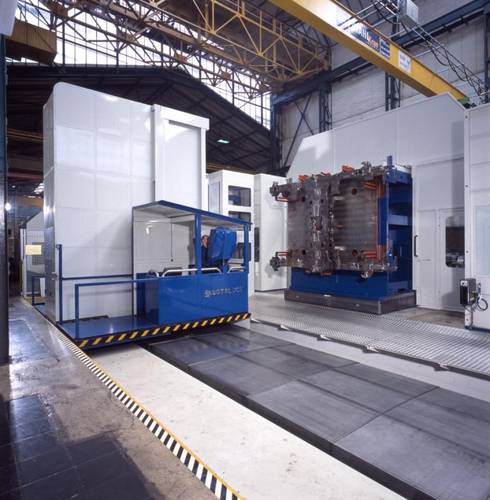
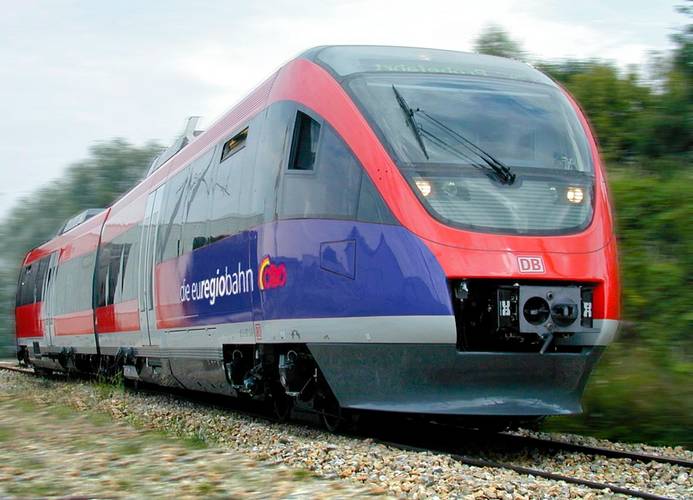
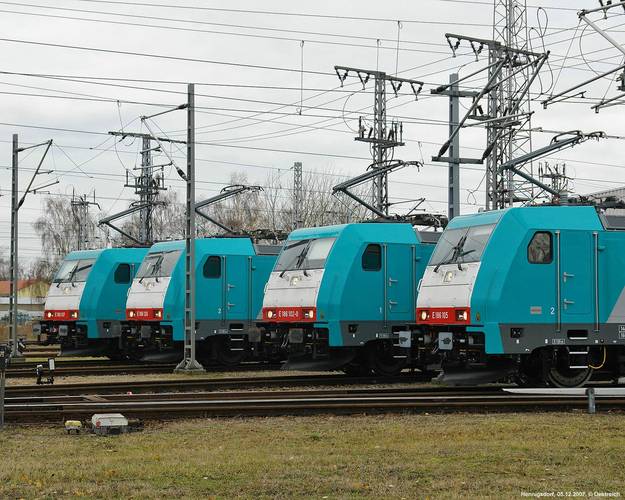
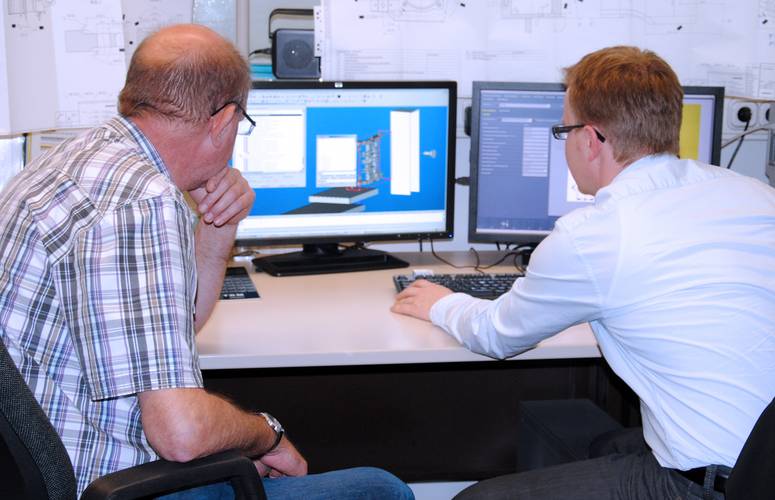
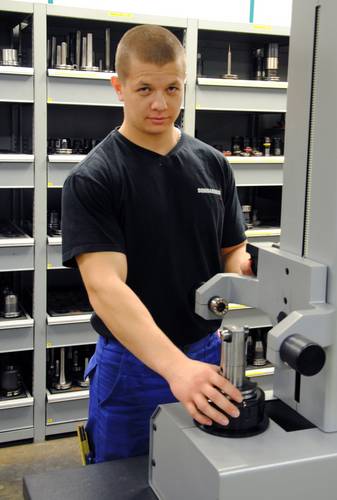
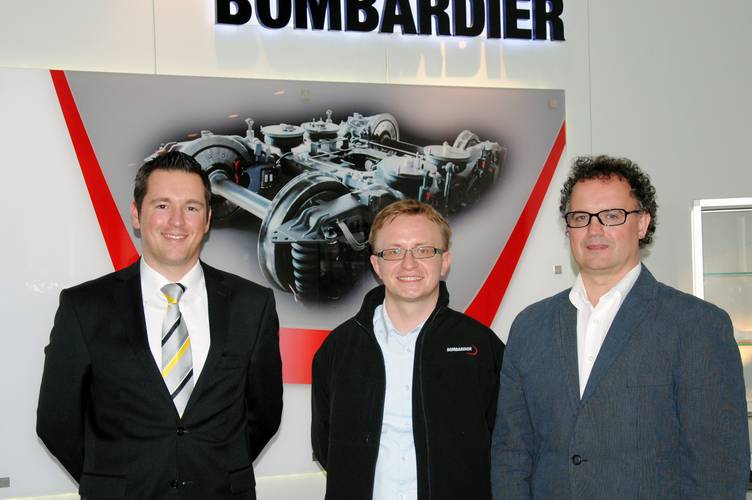
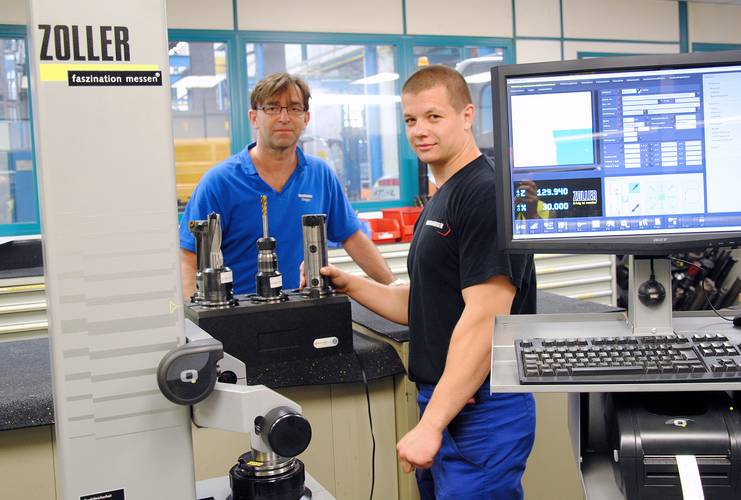
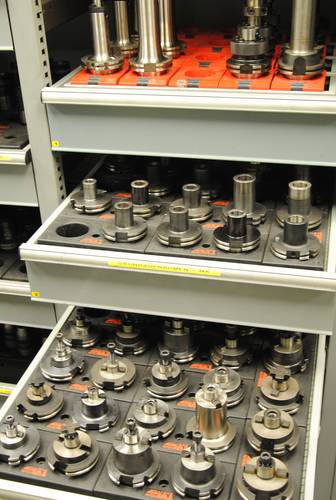
Avec plus de 36 000 collaborateurs et 62 sites dans 25 pays, Bombardier Transport est le plus grand constructeur mondial de matériel roulant ferroviaire. L’Allemagne est un pays ferroviaire par excellence et c’est là que la division Transport du groupe canadien Bombardier a son siège mondial. L’usine de Netphen fabrique des châssis et des bogies pour les matériels roulants ferroviaires de tous types, depuis le tramway jusqu’au train à grande vitesse. En revanche, Bombardier ne fabrique pas ces équipements uniquement pour ses propres trains : Bombardier Transport fournit notamment à Siemens Mobility les bogies nouvelle génération d’ICE.
Ce sont entre 2 500 et 3 000 châssis et bogies de différents types dont la fabrication mécanique est réalisée chaque année à Netphen, incluant peinture et montage final. Malgré la crise économique, le volume de commandes de ces dernières années a augmenté de telle sorte que l’usine bénéficie d’un plan de charge pour des effectifs de 700 collaborateurs. À elle seule, l’acquisition de nouvelles machines et de nouveaux outils n’a pas suffi à venir à bout de la charge de travail en constante évolution : il a fallu que l’entreprise améliore aussi sa productivité et qu’elle réduise les temps d’immobilisation relativement longs lors des changements d’équipements des machines et du rodage de nouveaux programmes CNC. La condition pour y parvenir a été l’introduction d’un système moderne de FAO en 3D. Début 2011, la société Moldtech de Netphen a installé ses premiers postes de travail TopSolid.
Optimisation du réglage des outils
Auparavant, les programmeurs FAO élaboraient les programmes CNC de fabrication des bogies à l’aide d’un système de programmation 2,5D qui non seulement prenait beaucoup de temps, mais était également source de nombreuses erreurs. « Nous faisions la programmation sur la base de dessins 2D, ce qui fait que nous ne savions jamais vraiment à quoi le châssis ressemblait, ni si nous avions tenu compte de toutes les arêtes gênantes en cours de fabrication », explique un utilisateur, Michael Kringe. Par ailleurs, les programmeurs de FAO ne pouvaient prévoir les outils que de façon approximative car ils n’avaient aucun accès direct aux données de l’ancienne base de données Access.
Cela impliquait une charge de travail supplémentaire lors du réglage des outils car les programmeurs étaient obligés de composer la totalité des outils sur la base de la liste d’outils approximative et des dessins. Il arrivait souvent qu’on ne s’aperçoive qu’au moment du rodage des programmes CNC que les outils étaient un peu trop courts ou un peu trop longs, et qu’il faille les modifier à nouveau.
Outre un système FAO en 3D, les utilisateurs de Netphen avaient donc le besoin urgent d’une gestion d’outils intégrée offrant la possibilité d’accéder aux paramètres d’outils réels lors de la programmation FAO. La nouvelle solution devait cependant apporter une aide non seulement à la programmation FAO, mais également à la gestion du parc d’outils et du lieu de stockage, ainsi qu’à la gestion des commandes. Il fallait de plus qu’elle puisse communiquer avec le système de mesure.
« C’est une solution complète que nous recherchions », explique Damian Sakwerda, programmeur FAO. « Comme cela faisait déjà longtemps que nous travaillions avec un appareil de réglage Zoller, nous avons décidé d’acquérir un nouvel appareil ainsi que la gestion d’outils Tool Management Solutions de Zoller. »
Le principal avantage de la gestion d’outils Tool Management Solutions est que, au lieu de travailler avec plusieurs bases de données dans l’entreprise, nous exploitons désormais une seule source de données d’outils, qui permet également d’enregistrer les valeurs de mesure réelles grâce à l’intégration de l’appareil de réglage. C’est d’autant plus important qu’il arrive que les outils soient réaffûtés, ce qui entraîne des variations de diamètre et de longueur.
La base de données contient toutes les informations nécessaires à la fabrication et accessibles en un seul clic. Cela permet non seulement d’économiser du temps, mais aussi de réduire le nombre d’erreurs pendant la préparation des outils, comme le déclarent d’une même voix Rüdiger Hof et Sergej Ponomarenko, du service de réglage.
Le système Tool Management Solutions de Zoller est une solution conçue de manière modulaire qui gère les caractéristiques et les données techniques des outils et des composants, mais également leur lieu de stockage. Le temps est ainsi optimisé lors de la recherche des outils dans l’atelier. La disponibilité s’en trouve également accrue, ce qui réduit le nombre d’outils nécessaires à la fabrication.
Pour l’usine Netphen, savoir combien d’outils sont nécessaires et où ils se trouvent est d’autant plus important car nombreux sont les outils utilisés et les chemins qu’ils empruntent sont parfois tortueux. Ils vont de magasin en magasin pour le préréglage, puis vers les machines, subissant parfois d’autres étapes intermédiaires.
À ce jour, environ 2 500 outils complets circulent au sein de l’entreprise, soit 1 200 rien que pour les quatre centres de perçage et de fraisage de Bimatec Soraluce, souvent en multiple exemplaire pour garantir leur disponibilité. Michael Kringe estime que, grâce au logiciels installés, les coûts d’outillage ont été réduits de 25 %, soit environ 200 000 euros par an.
FAO avec gestion d’outils intégrée
La possibilité d’intégrer TopSolid’Cam et le système Tool Management Solutions de Zoller a certes été un critère important dans la décision en faveur du logiciel de FAO, mais cela n’a pas été la seule raison. En effet, quatre systèmes de FAO avaient été présélectionnés et leurs performances ont été testées sur la fabrication d’une même pièce. TopSolid’Cam nous a convaincus par sa facilité d’utilisation, par ses fonctions d’importation complètes et par la prise en charge de modèles 3D venant de systèmes tiers (les bogies sont, en effet, modélisés dans Catia), par la représentation simple et claire des opérations d’usinage et surtout par les puissantes fonctions de simulation dans l’environnement de la machine.
Il a été également décisif de pouvoir compter avec la société Moldtech sur un partenaire compétent pour l’implémentation, la formation (y compris la formation continue) et l’assistance relatives à la solution de FAO. « Grâce à la qualité du support que nous avons reçu de Moldtech, le passage à la 3D a été pour nous quelque chose de très simple », poursuit D. Sakwerda.
En lien avec Zoller, Moldtech a programmé l’interface bidirectionnelle entre TopSolid’Cam et le logiciel de gestion d’outils. Les programmeurs FAO indiquent à TopSolid’Cam les caractéristiques et les propriétés souhaitées, puis ils interviennent directement sur les données des outils au sein du système Tool Management Solutions. Cela leur facilite la tâche et améliore surtout la fiabilité des programmes CNC.
Pour pouvoir utiliser les outils de simulation de programmation FAO, il faut bien entendu avoir recours à des modèles 3D. Habituellement, ces modèles sont construits sous forme d’enveloppe géométrique sur la base des caractéristiques, puis mis à la disposition du système de FAO. Pour les contours complexes, il est néanmoins possible de les produire manuellement et de les enregistrer dans la base de données d’outils. Par ailleurs, il est possible d’importer des modèles 3D de catalogues constructeurs dans des formats neutres.
La liste des outils utilisés pour la programmation FAO peut être à son tour transmise à la gestion d’outils, et directement utilisée pour la production de fiches de réglage, ce qui réduit sensiblement les coûts liés au réglage.
Moldtech ne s’est pas seulement occupée de la programmation de l’interface avec la gestion d’outils, mais également de l’interfaçage avec le parc de machines. La prise en charge des unités de perçage et de fraisage de Bimatec Soraluce, équipées de têtes amovibles, s’est avérée particulièrement exigeante. En fonction des surfaces devant être usinées sur le châssis, les outils peuvent être équipés d’une tête rigide, d’une tête coudée ou d’une tête orthogonale pivotante.
L’usinage avec TopSolid’Cam étant programmé avec l’environnement de machine virtuelle, la cinématique des têtes amovibles doit être simulée de manière fiable avec ses degrés de liberté, puis traduite en langage machine. C’est Moldtech qui a préparé les modèles cinématiques de machines, avec les post-processeurs.
Bombardier Transport a uniformisé l’usinage sur les unités de perçage et de fraisage de différentes dimensions, de telle manière que l’on n’ait plus besoin que d’un seul post-processeur. Il a fallu un certain temps pour adapter et optimiser ce dernier car Moldtech n’a pas seulement dû reproduire les fonctions spécifiques des machines, mais également un certain nombre de cycles d’usinage propres à l’entreprise.
Pour les trajets d’outil qui se répètent, les programmeurs FAO utilisent par exemple depuis longtemps la technique des sous-programmes qu’il a fallu adapter au nouvel environnement : « Les opérations telles que le surfaçage, les cycles de fraisage ligne à ligne ou le rognage sont d’abord conçues en tant que sous-programmes, qui sont ensuite appelés plusieurs fois avec d’autres profondeurs de passe », explique D. Sakwerda. Cela a entre autres l’avantage de donner des programmes CNC relativement légers et pouvant donc être chargés plus rapidement.
Temps de rodage quasiment divisé par deux
Les opérations de fraisage et de perçage d’un châssis soudé complet peuvent prendre jusqu’à 22 heures en fonction de la complexité du travail à effectuer. Il est donc facile de s’imaginer le temps que cela peut prendre de roder pas à pas un programme CNC entièrement nouveau. M. Kringe estime que les temps de rodage pour l’usinage d’une nouvelle pièce ont été réduits de près de 50 %.
Grâce aux puissantes fonctions de simulation de TopSolid’Cam, les programmeurs sont en mesure de détecter des collisions éventuelles dès le stade de la programmation sur ordinateur, ce qui améliore la sécurité. Par ailleurs, ils ont la possibilité de simuler les parcours d’approche et de dégagement, et de les optimiser en ayant un regard sur le temps de parcours des machines.
Les économies de rodage sont essentiellement dues à la diminution du nombre d’erreurs de programmation à éliminer après détection sur la machine. Grâce à la bonne intégration de TopSolid’Cam et de la gestion des outils, la durée nécessaire au montage et au démontage a été réduite car le système Tool Management Solutions de Zoller est capable de déterminer les outils déjà disponibles sur la machine concernée.
Cela signifie concrètement que la durée nécessaire pour passer l’usinage d’une pièce donnée d’une machine à une autre est désormais comprise entre deux et trois heures, contre quatre ou cinq heures auparavant. « Grâce à la programmation en 3D et à la gestion d’outils intégrée, nous avons gagné en productivité pour l’usinage mécanique », conclut D. Sakwerda. Et Rüdiger Hof, du service de réglage, ajoute : « Nous travaillons désormais beaucoup plus sereinement car grâce à Zoller et TopSolid’Cam, nous ne pouvons plus faire d’erreurs ».
Besoin de plus d'informations
UNE QUESTION SUR NOS
PRODUITS OU SOLUTIONS ?
Trouvez le point de vente le plus proche Contactez-nous Demandez un devis