18 September 2012

Pour pouvoir rivaliser avec la concurrence internationale, les entreprises présentes dans des pays où la monnaie est forte doivent veiller à maintenir un coût de production aussi bas que possible. La société Ifanger AG en sait quelque chose ! Ce fabricant d’outils suisse utilise le logiciel de CAO/FAO TopSolid pour fabriquer des outils de tournage et de moletage et pour programmer l’usinage CNC. Il est ainsi parvenu à réduire sensiblement les temps de programmation et d’exécution initiale ; un gain de temps qui se traduit par des économies de francs suisses.
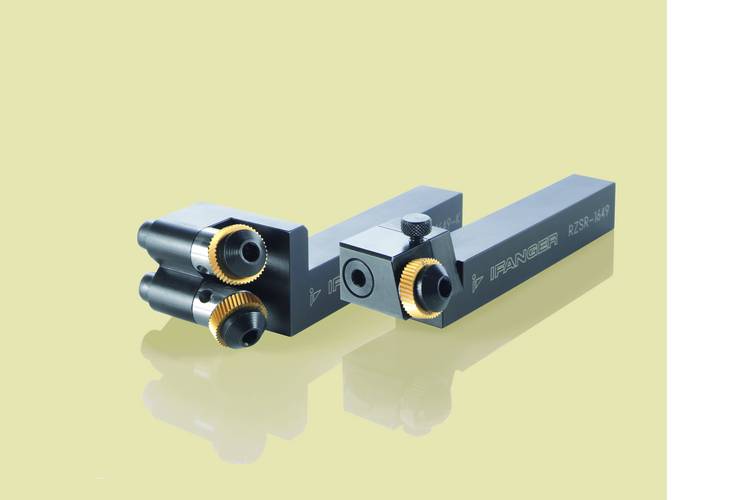
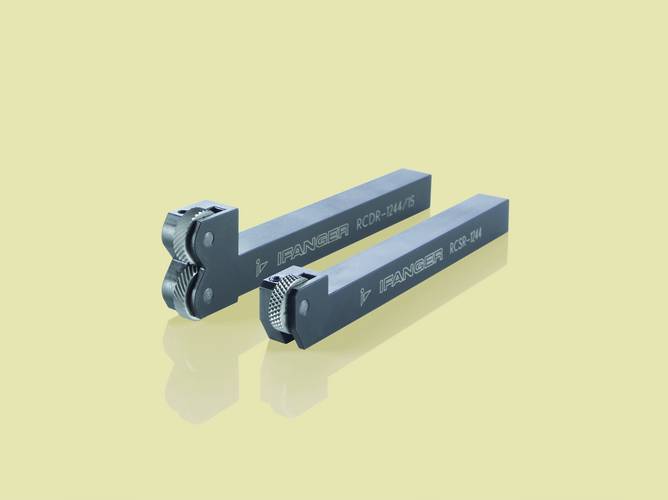
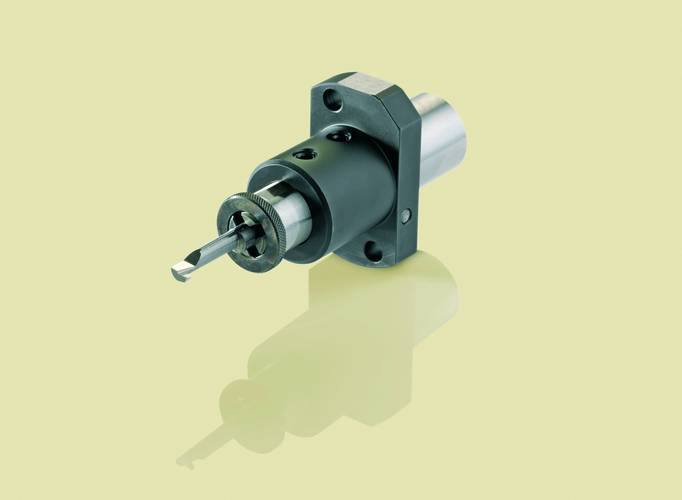
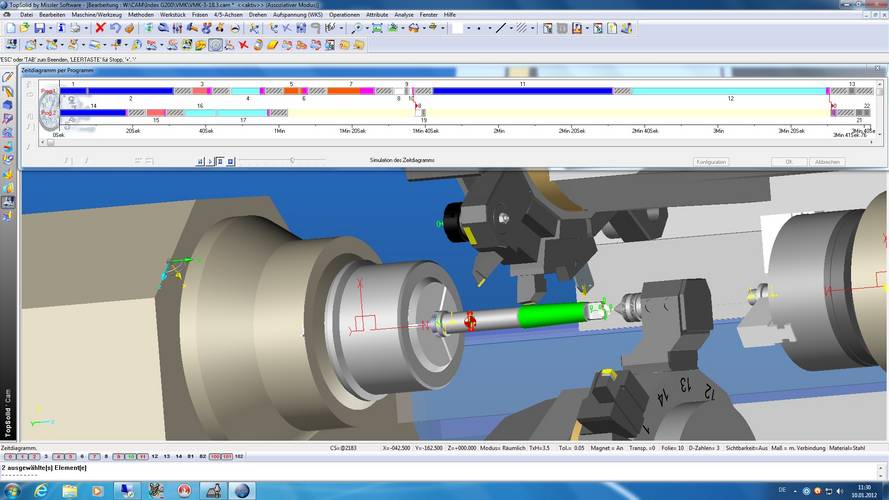
Proposer des technologies d’usinage de pointe, tel est le credo de la société Ifanger AG, fondée en 1917 par le grand-père du directeur actuel, et implantée à Uster près de Zürich. Outre des outils spéciaux de tournage et de moletage, cette entreprise familiale suisse développe et fabrique des outils de tournage intérieur de haute précision, conçus à base de métaux durs et destinés à des alésages dont le diamètre est compris entre 0,5 et 7 mm. Ils sont commercialisés dans le monde entier sous le nom de marque MicroTurn (principalement pour des clients des secteurs de l’électronique, des technologies médicales et de la construction automobile). Depuis de nombreuses années, l’entreprise propose également sur le marché suisse des porte-forets et des outils de serrage, ainsi que des outils de fraisage, de tournage, de perçage et de lamage usinés par des fabricants reconnus, tels que Kennametal ou Komet.
Les outils de tournage intérieur dotés d’un profil régulier, pouvant uniquement être aiguisés au niveau de la face de coupe, ont pendant longtemps été le fleuron de la marque d’outils suisse. « Aujourd’hui, nos produits phares sont les outils de tournage intérieur de la gamme MicroTurn en métal dur et taillés dans la masse », explique Stefan Spuler, directeur d’Ifanger. Bien qu’il s’agisse généralement de produits standard, la société doit développer de nouveaux porte-outils adaptés pour chaque nouvelle machine de tournage longitudinal introduite sur le marché. Et elles sont nombreuses ! De même, les outils de tournage de plus grande taille et dotés de plaquettes, ou les supports des molettes rayées, font souvent l’objet de fabrications particulières, qui doivent être développées et usinées dans le cadre du contrat avec le client.
De la CAO à la FAO
Pour réaliser plus vite et à meilleur prix les demandes personnalisées des clients, Ifanger modélise les outils et porte-outils spéciaux en 3D à l’aide de TopSolid, afin de pouvoir les adapter rapidement en entrant simplement quelques paramètres. De cette manière, les temps de rotation ont pu être considérablement réduits, comme l’explique M. Spuler : « Dans le temps qui nous était auparavant nécessaire pour dessiner le support d’une molette rayée en 2D, nous arrivons aujourd’hui à adapter la maquette, à créer le programme de FAO adapté et à fraiser la pièce sur la machine. L’association de la CAO et de la FAO génère des gains de temps exceptionnels, notamment en ce qui concerne les gammes de produits fabriquées en petites quantités. »
Il y a un peu plus d’un an, l’acquisition d’une nouvelle fraiseuse haute précision de type Fehlmann P60 et équipée d’une commande Heidenhaim 53 s’est avéré une occasion idéale pour introduire la solution de CAO/FAO 3D de Missler Software. Pour transformer les porte-outils conformément aux exigences du client ou de la machine sur des machines 5 axes compactes et dotées de dispositifs de réduction des vibrations, il était indispensable de mettre en œuvre un nouveau système de programmation. En effet, l’éditeur classique ne permettait pas de programmer l’usinage complexe de pièces comprenant de nombreuses obliques imbriquées, ou uniquement en échange d’une quantité démesurée de travail et de temps pour l’exécution initiale et l’optimisation du code NC. « Nous voulions justement gagner en rapidité pour les pièces produites en petites quantités et pour cela, une programmation sans faille est nécessaire », poursuit Stefan Spuler qui s’est lui-même chargé de rechercher un logiciel adapté. Mais l’achat du nouveau système de programmation avait également une autre raison d’être : la société souhaitait proposer des emplois attractifs pour les jeunes qui correspondent à leur formation.
En tant que fabricant d’outils et de supports spécialisés, Ifanger avait besoin d’un système de FAO doté de fonctionnalités CAO performantes, une condition qui réduisait d’ores et déjà le nombre de systèmes envisageables. Pour l’entreprise, une bonne prise en charge des travaux de tournage était également essentielle, dans la mesure où, en plus de la Fehlmann P60, deux centres de tournage-fraisage de type Index G200 devaient être également reliés à la solution FAO. Ces deux machines sont équipées d’une double broche et de deux tourelles porte-outils qui sont dotées d’outils à entraînement pour les opérations de fraisage et de perçage des pièces tournées. Ifanger utilise déjà ces machines depuis quelques années ; elles étaient cependant jusqu’à récemment programmées à l’aide d’un éditeur de texte standard. Dans ces conditions, l'utilisateur ne décelait les collisions qu'au moment de l’exécution initiale. Il en résultait alors de longues périodes d’inactivité ou d’immobilisation de la machine.
Trouver le bon partenaire
Ifanger a rapidement trouvé le logiciel adapté à ses attentes : parmi les solutions ou les combinaisons de systèmes évaluées, TopSolid offre la meilleure intégration CAO/FAO ainsi que la meilleure prise en charge de l’usinage par tournage/fraisage. Si le choix du système fut facile, celui du partenaire demanda un peu plus de réflexion. Malgré la distance géographique et la barrière linguistique (le suisse allemand étant une langue en soi), l’entreprise suisse s’est néanmoins décidée en faveur d’AdeQuate Solutions, partenaire Missler Software, du fait de son expérience dans le domaine du tournage-fraisage et de ses importantes ressources en personnel. « Pour nous, c’est la garantie d’un bon support technique et d'une réaction rapide en cas de besoin d’ajustement des post-processeurs », explique M. Spuler, qui se montre pleinement satisfait de la société de services informatiques basée à Lahr.
Pour commencer, AdeQuate Solutions a raccordé la fraiseuse Fehlmann P60 au logiciel TopSolid. La société de services informatiques a fourni les post-processeurs nécessaires avec un système de modélisation de machines cinématique qui permet de simuler l’usinage à 5 axes dans l’environnement virtuel de la machine. Au niveau du post-processeur, seuls trois ou quatre réglages ont été nécessaires pour que l’application fonctionne parfaitement, comme l’explique Stefan Spuler : « Nous avons nous-mêmes modélisé la tour de bridage pour le serrage de plusieurs éléments, afin de pouvoir simuler l’usinage quel que soit l’élément utilisé. Pour les outils de fraisage, nous utilisons la solution standard de TopSolid’Tool, de sorte que nous n’avons dû insérer que quelques fraiseuses spéciales et les supports dans la bibliothèque. »
Pour le tournage, en revanche, de nombreux outils ont été reproduits intégralement dans TopSolid’Tool, tandis que les supports des machines Index ont pu être téléchargés à partir de la page d’accueil du fabricant. Le raccordement entre les deux centres de tournage-fraisage s’est avérée un peu plus difficile, Ifanger ayant certaines exigences en ce qui concerne l’étayage des pièces, la mobilité des tourelles porte-outils et le maintien de la pièce par la contre-broche. Aujourd’hui encore, ces opérations doivent être réalisées manuellement par les programmeurs de FAO. Mais pour Richard Zak, responsable de la division de tournage-fraisage chez Ifanger, « cet inconvénient n’est pas tant à imputer au post-processeur, qui interprète correctement les opérations définies manuellement, qu’aux routines manquantes du logiciel de FAO. TopSolid offre la possibilité d’enregistrer ces opérations sous forme de méthodes réutilisables, mais pour cela, nous manquons encore un peu de formation ».
Des gammes de pièces facilement ajustables
À propos de formation : AdeQuate Solutions a dispensé une formation de trois jours aux utilisateurs, afin de leur présenter les principales fonctions de CAO et de FAO. De l’avis de M. Spuler, qui travaille lui-même avec le système, c’est peu de temps pour véritablement se familiariser avec les particularités de la construction paramétrique : « Je définis par exemple les porte-outils comme une gamme de pièces afin de pouvoir les adapter rapidement aux exigences des clients. Une fois que les relations paramétriques sont correctement définies, tout va très vite. Récemment, j’ai épaté un client en modifiant la maquette 3D pendant notre conversation téléphonique et en lui envoyant le PDF avec le dessin mis à jour avant même qu’il n’ait reposé le combiné. »
La durée de travail nécessaire à la construction s’est considérablement réduite grâce au paramétrage systématique des pièces qui prennent souvent des formes similaires et grâce à la création de gammes de pièces. Autre avantage de l’intégration de la 3D : la modélisation permet de créer des vues photoréalistes des produits pour les catalogues et pour la documentation du client. Cet atout n’est pas encore exploité à ce jour.
Les constructeurs utilisent également TopSolid pour la modélisation des outils MicroTurn, afin de créer des dessins de fabrication à partir des maquettes, pour la rectification des métaux durs. Au grand regret de M. Spuler, les machines de rectification ne peuvent pas être reliées à TopSolid’Cam pour l’instant ; il n’est donc pas encore possible d’en programmer l’usinage par la CAO. De ce fait, les équerres (mathématiquement exactes) de certaines géométries figurant dans les dessins doivent être retravaillées pour la fabrication. « Cela ne pose pas de problème majeur », explique Stefan Spuler ; « nous devons simplement veiller à appliquer les mesures saisies manuellement en cas de modifications. »
Une programmation plus rapide
Dans les locaux d'Uster, TopSolid est actuellement utilisé sur deux postes de travail de CAO et un poste de FAO que se partagent deux programmeurs au sein de l’atelier. Ils travaillent juste à côté des machines, de sorte que l’exécution des nouveaux programmes de commande numérique peut être observée directement sur place. « Nous avons défini le montage et le serrage des machines en fonctions des pièces, afin d’appliquer facilement un modèle contenant les opérations d’usinage, les valeurs de coupe, les impacts, etc. pour des pièces identiques. Cette réutilisation des données a permis de réduire à une demi-heure les opérations de programmation qui prenaient entre deux et trois heures les premiers temps », explique M. Zak. Des gains de temps supplémentaires sont également possibles grâce à l’exploitation constante de séquences de traitement standard, par exemple pour le perçage, le centrage, le biseautage et le filetage, qui peuvent être enregistrées dans la maquette CAO, sous forme de fonctionnalité.
Le logiciel TopSolid accélère non seulement la programmation du fraisage et du tournage, mais il réduit également la durée nécessaire à l’exécution d’un nouveau programme NC sur les machines. Cela vaut notamment pour les centres de tournage-fraisage dans lesquels les mouvements de deux tourelles porte-outils doivent être réglés de manière synchronisée dans un laps de temps relativement court. Pour M. Zak, qui a déjà travaillé avec différents systèmes de FAO, « le bon contrôle visuel sur l’ensemble de la machine est un des atouts majeurs du logiciel ». Il permet aux utilisateurs de constater et de corriger les problèmes de collision dès le stade de la programmation. Ainsi, les programmes NC envoyés à la machine sont fiables.
Un diagramme prévisionnel vous permet également de simuler le déroulement temporel des opérations d’usinage au niveau de la broche et de la contre-broche, et de les planifier de manière à réduire au minimum la durée d’exploitation des machines. « Bien entendu, c’est quelque chose que nous faisions déjà avant, mais uniquement lors de l’exécution initiale du programme, c’est-à-dire que les machines restaient souvent inactives pendant des heures », se souvient M. Spuler. « L’intégration de TopSolid n’entraîne pas forcément une réduction des temps d’exploitation des machines, mais plutôt une disponibilité accrue des machines, dans la mesure où nous consacrons aujourd’hui bien moins de temps à la recherche d’erreurs et à l’optimisation du programme d’usinage. » Cela permet de réaliser des économies, un facteur concurrentiel important pour les entreprises qui officient dans des pays dotés d’une monnaie forte. En effet, nos voisins membres de la Communauté européenne ne peuvent pas espérer voir l’Euro reprendre de la vigueur de sitôt.
Besoin de plus d'informations
UNE QUESTION SUR NOS
PRODUITS OU SOLUTIONS ?
Trouvez le point de vente le plus proche Contactez-nous Demandez un devis