3 November 2020
PMP Multitask, a company specializing in multi-tasking machining for the medical sector, has chosen TopSolid’s CAD/CAM solution to respond to its rapid growth which will be reflected by moving to a new structure in the coming months, where the company aims to double its production using Lean logic and Industry 4.0.
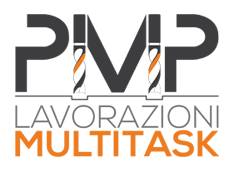
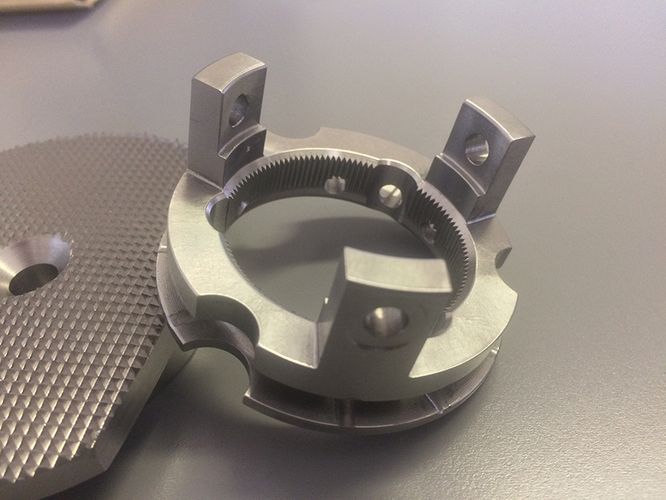
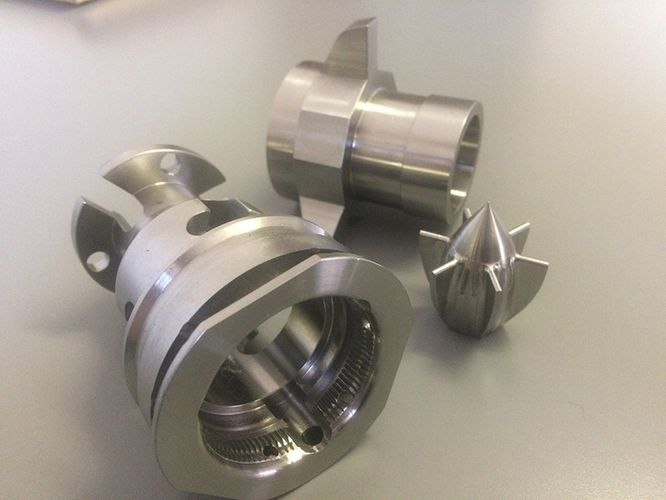
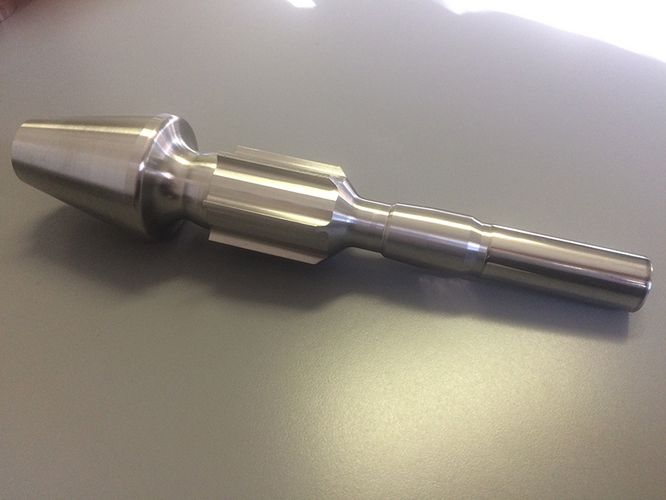
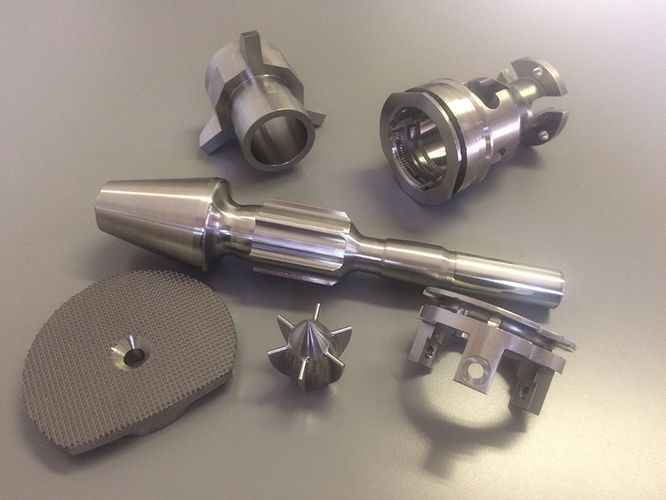
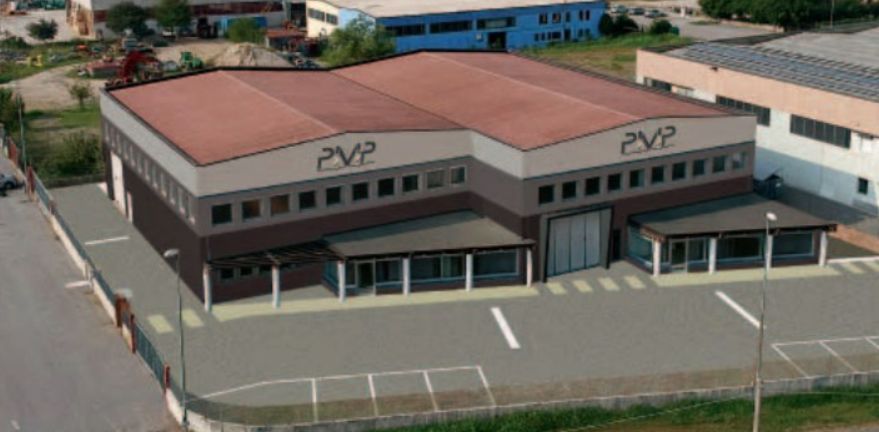
As part of its growth strategy, PMP Multitask, a company offering multi-tasking machining for the medical industry, has chosen to rely on the TopSolid suite from TOPSOLID SAS for its CAD/CAM projects. With a view of relocating to a new site that will quadruple the floor space, and with an annual turnover growth of 20%, PMP Multitask has in fact found in TOPSOLID SAS’ offer the most suitable solution to regroup the tools that will be used in the design and production of its structure. Therefore, the company will benefit from the knowledge shared between all operators and obtain a high degree of versatility to manage quality production rapidly and with flexibility.
However, in addition to the highly appreciated solid modeling and unfolding, the ability to use floating licenses from the purchased licenses was a deciding factor in the choice. This offers greater flexibility with respect to the use of the software, hence providing optimal return on investment. The support and expertise of TOPSOLID SAS technicians also enabled PMP to customize certain post-processors and optimize production with new machining strategies specifically tailored to their needs. Finally, the convenience of the TopSolid PDM server will be of great help in Lean process that PMP will be implementing at its new site, by changing the image in terms of efficiency and cleanliness of product lines, as required by the stringent standards in the medical industry.
Special multi-tasking materials
PMP Multitask is a company founded in 2005 in Peschiera del Garda, Italy on the initiative of brothers: Maurizio and Alessandro Pederiva, who have acquired ten years of experience in the family business.
The company specializes in the multi-tasking processing of special materials, such as stainless steel, duplex, super duplex, aluminum alloys, special plastics, titanium and its alloys, heat resistant alloys, hastelloy, inconel and superalloys.
The medical sector is the main reference sector for which PMP has also obtained the 13485 certification, in addition to the 9001 standard for general mechanics. The other industrial sectors are therefore packaging and food, with some applications in the field of motor racing and hydraulics.
- "Thanks to the multi-tasking machining process, we are able to deliver finished parts from raw materials, which reduces production time and increases levels of machining precision, with the unique positioning of the part on the machine,” explains Maurizio Pederiva, owner of PMP Multitask.
The services offered include turning, milling, drilling and tapping, as well as 5-axis cutting and inclined machining. Everything is done in-house, thanks to a fleet of machines that includes the eight latest-generation machining centers, including five centers for 5-axis continuous operations. In order to offer a complete finished product to end customers, the company therefore collaborates externally with a certain number of companies specializing in heat and surface processing and other complementary machining operations.
In 2005, on the recommendation of a machine tool technician, PMP was introduced to TopSolid and decided to add the two CAD/CAM solutions already used on their workstations to a TopSolid test license. The rapid expansion that has taken place in recent years, with increases at a rate of 20% per year, reaching a turnover of 1.2 million euros in 2018, led the company to move its activities to a new facility in the province of Mantua, Italy which with its 1,200 m² will quadruple the floor space.
- "With demand rising sharply last year, we began to feel the need to consolidate the CAD/CAM solutions we were using in the company. The choice went to TopSolid, with the purchase of four licenses in September 2018 to cover all the machining operations that take place in our fleet of machine," explains Pederiva.
Highly flexible floating workstations
PMP has chosen the TopSolid solution as the CAD/CAM benchmark for various reasons, starting with the exceptional level of performance it offers in solid modeling. Although PMP is a subcontractor, the company is often responsible for making changes and advising customers on changes to be made to the projects assigned to them. The high level of flexibility and versatility of the software is therefore highly appreciated, offering the company a high level of responsiveness in making rapid changes from one machining operation to another.
- “We often have to be very responsive and flexible when machining small series of parts. TopSolid is a highly versatile tool that perfectly meets this need, allowing us to quickly manage urgent requests, for example, by exchanging project files even between machines that are not fully compatible with each other, with practically no file modifications needed," says Pederiva.
Above all, the floating license system was the deciding factor to adopt the TopSolid solution. It allows the software to be installed on all machines in the workshop, so that they can be used interchangeably by all operators.
- "This feature was decisive because it also makes the solution very cost effective. Having floating CAD/CAM stations also allowed us to pool the knowledge of our operators together, without having to depend on the skills of a single employee who previously managed the software on a single workstation," says Pederiva.
As part of the contract with TOPSOLID SAS, training courses were organized for all PMP operators, who are now able to program using the same software with all its possibilities and modules on the entire fleet of machines in operation.
Lean and connectivity for the medical sector
In the process of consolidating the CAD/CAM solutions used, PMP therefore worked closely with TOPSOLID SAS to customize certain aspects of the software.
- "TOPSOLID has effectively supported us in the customized development of some post-processors and in the management of standard tools, with the creation of our automatic tool generation database. TOPSOLID SAS gave us recommendations on the fastest and most efficient methods to use to customize the tool. We obtained a very good result, also in the creation of exchange templates from one machine to another that allow us to be really efficient," explains Pederiva-.
With its expertise, TOPSOLID SAS has also advised the company on new machining strategies contained in the 5-axis modules made available, which save considerable time in the specific machining operations carried out at PMP.
- "We have saved a lot of time in machining operations and increased our competitiveness compared to our main competitors. We are using the complete TopSolid solution, with the exception at the moment of the module for the machining of variable pitch screw, a type of part that we do not often have the opportunity to machine, but which will probably be implemented in the future."
Finally, the decision to rely on TopSolid is proving to be a winner, in particular because of the upcoming expansion of the company, with the imminent move to the new structure that will be built according to Lean logic to have a clean, almost entirely sterilized workshop environment inspired by the best manufacturing processes. In PMP's projects, Lean should allow for a 50% increase in production, employing the same number of employees, i.e. 11 people working in the company to date.
- "We are already connected in logic 4.0 with some of our machines and in the new building, we will have a brand new company network that will allow us to connect everything to the management and CAD/CAM system, which will transmit data directly to the machine through the network. It is also thanks to the simplicity of the TopSolid PDM that we have considerably increased the backup speed, as well as improving the control and security of the data itself," explains Pederiva in conclusion.
A real change of image will therefore support PMP's expansion in the coming months, with a decisive push toward cleanliness and maximum process efficiency, in order to offer a quality of service that corresponds perfectly to the requirements of end customers in the medical industry.
(article written by Marco Zambelli – RMO, February/March 2019)
Meer informatie nodig
EEN VRAAG OVER ONZE PRODUCTEN OF OPLOSSINGEN?
Vind uw dichtstbijzijnde verkooppuntContacteer onsVraag een offerte aan