23 July 2012
We are all familiar with fire doors made of metal. Yet the fact that an elegant wooden door is able to resist fire for one hour or more would come as a surprise to most people. Lindner Türen-Fassaden s.r.o. (Linder Doors & Facades), a Lindner Group company, manufactures project doors of this type in various dimensions for customers worldwide. In order to program more efficiently the CAM machining of the blanks, the door models are configured in 3D to customer specifications using TopSolid’Wood from Missler Software.

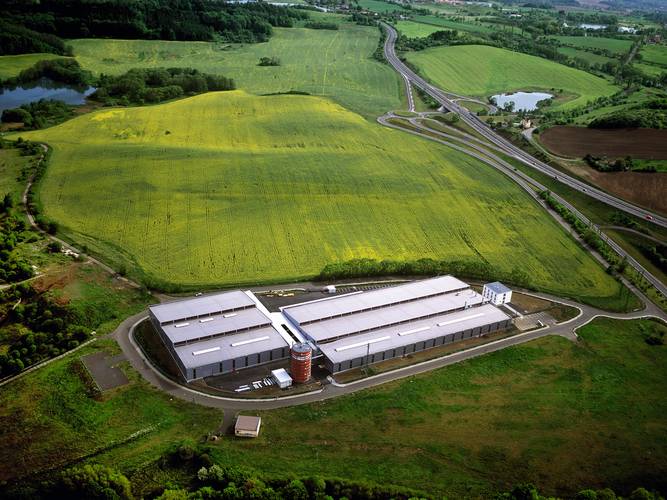
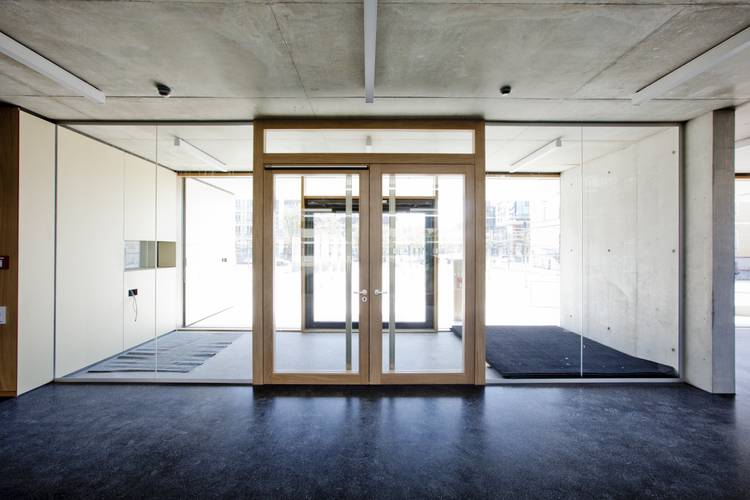
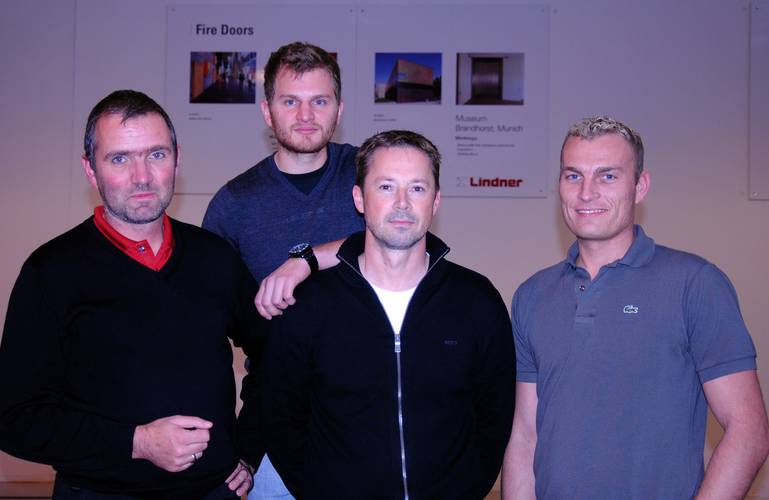
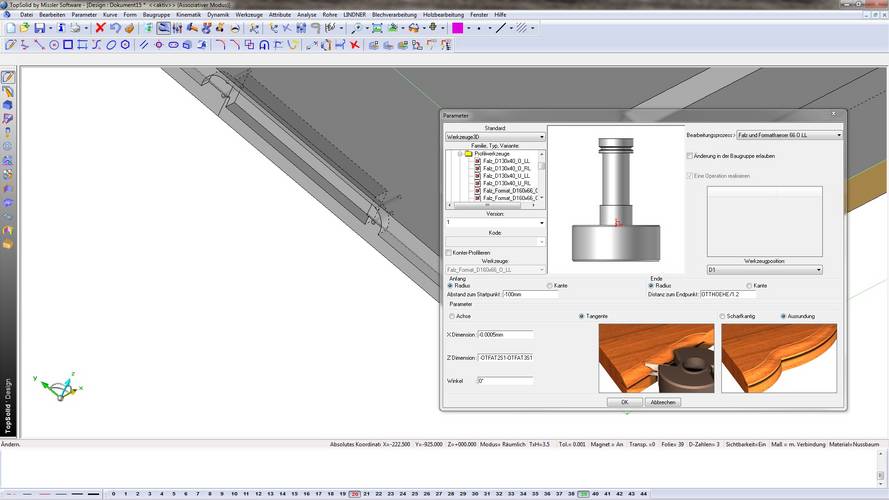
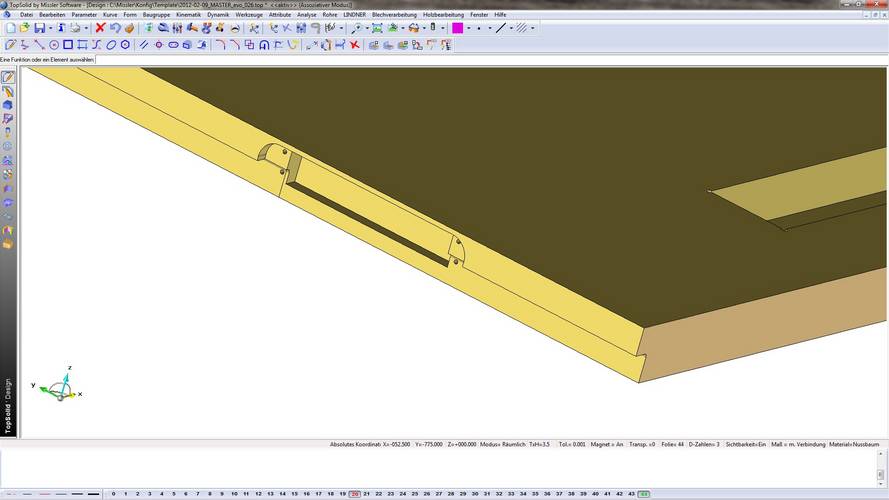
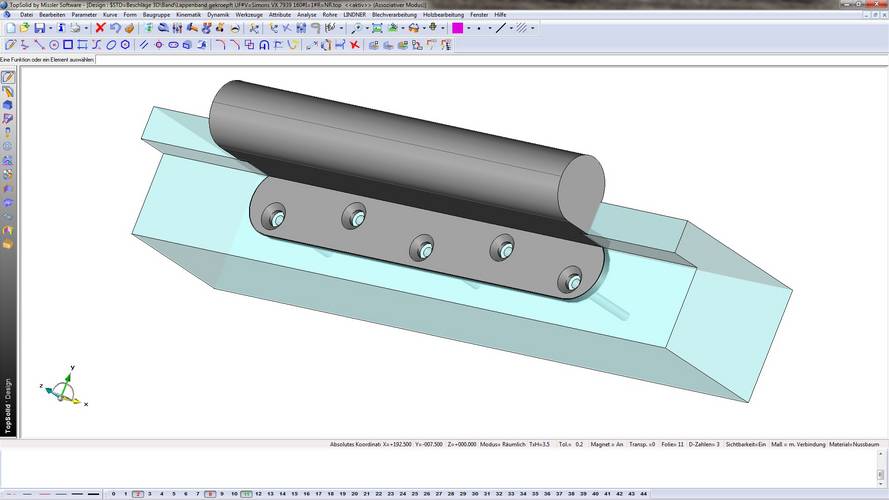
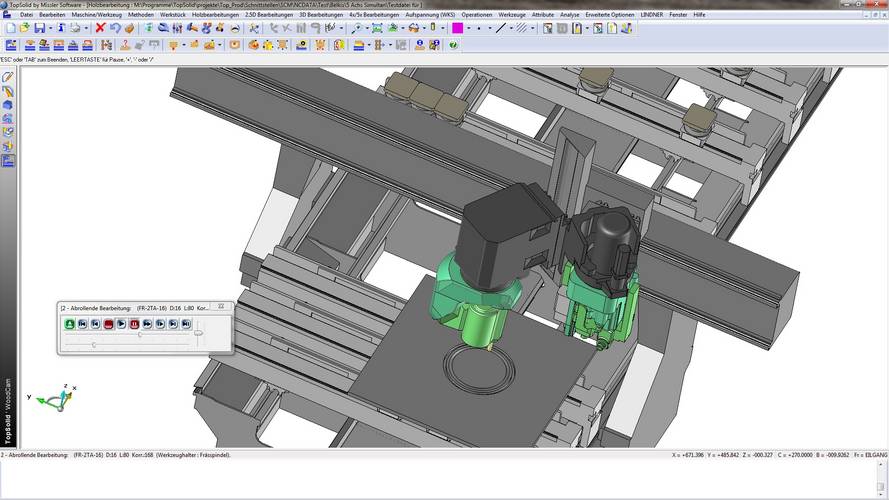
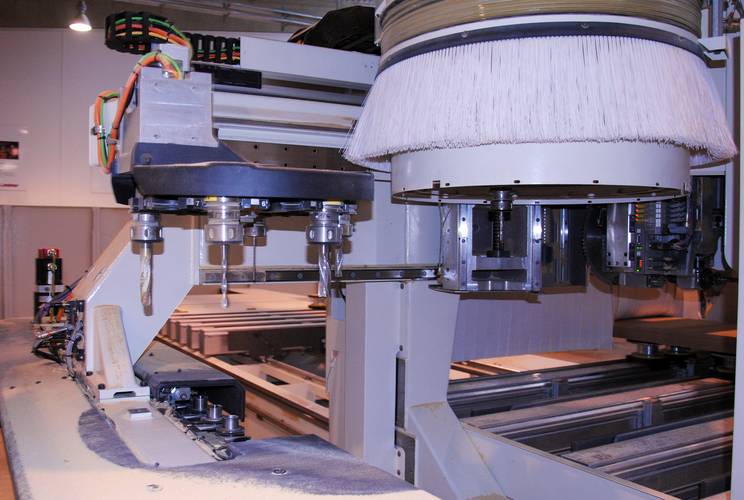
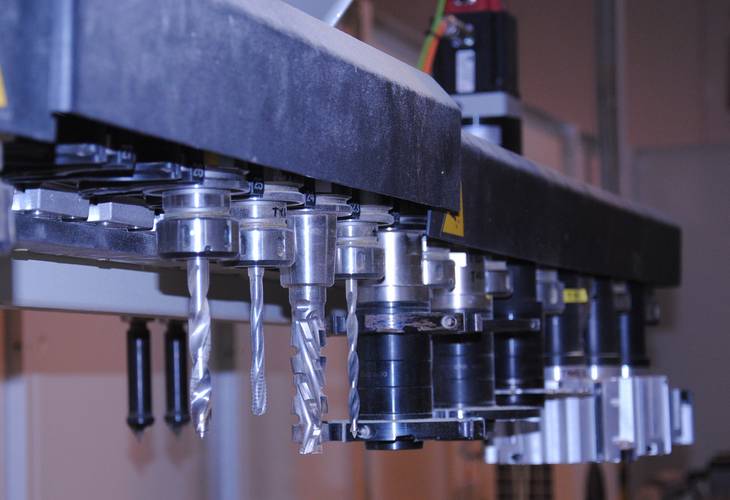
With over 5500 employees, six production sites and more than 50 international subsidiaries, the Lindner Group, with its head office in Arnstorf, Lower Bavaria, is one of the world's leading specialists for interior fittings, insulation technology and sophisticated facade design. This family company, founded in 1965 by Hans Lindner, not only develops customer-specific concepts for the facades and interiors of airports, railway stations, cruise ships, concert halls and office buildings, but also supplies its own purpose-built products: ceiling and partition wall elements, double floors and, for the case in point, special doors for fire, smoke, radiation, noise and burglar protection. Lindner also provides services such as pollutant cleanup or the renovation and interior demolition of buildings.
The project doors are produced in the Czech town of Ostrov, near Karlovy Vary, where Lindner built a modern factory for doors and wall elements five years ago, and which today employs around 100 Czech and German workers. The factory has a production capacity of approximately 50,000 doors per year, working flat out on this "special door". "In this regard we are better and faster than most of our competitors," says Kurt Fritz, boss of Lindner Türen-Fassaden s.r.o.: "All our doors are custom-made, often manufactured singly and seldom in more than 10 units. Time is therefore a critical factor, along with costs. We also have to face up to the competition within the group, and offer our products at similar prices to other manufacturers."
The production processes in Ostrov are strictly organised, in order to guarantee a work cycle of eight weeks maximum. The focal point of the door manufacturing is the MAKA 5-axis machining centre, equipped with 2 milling spindles and a pneumatic handling system for work piece loading. On the machine, the door blanks are milled to the desired overall dimension (basic formatting), grooved along the edges and fitted out with the recesses for locks, hinges, floor seals and glazing. In order to be able to react more flexibly to specific customer wishes, Lindner expanded the machine pool some months ago to include an SCM Accord 40fx machining centre for the 5-axis machining of particularly complex contours. In terms of the number of tool slots and the dimensions, both machines can be used for machining complete doors, meaning that the company has alternative possibilities in the event of capacity bottlenecks or malfunctions.
Connection to the ERP system
Both the SCM machining centre and the MAKA are connected to the TopSolid’Wood CAD/CAM system. Missler Software sales partner, AdeQuate Solutions, programmed the post-processors required for this, which were then tested and optimized on the machines. Furthermore, the Lahr-based system vendor prepared the machine models in 3D, this being a prerequisite for reliable simulation of the CAM machining. The tools had to be modelled in part by the operators themselves in 3D, since most manufacturers do not yet make any 3D data available. The operators are extremely satisfied with the quality of the post-processors. "We have learned to be cautious, since when we introduced the old solution we found out that the machine does not always do what we expect it to," says Mr. Fritz. "Thanks to AdeQuate Solutions, we haven't yet seen many metal chips flying around."
AdeQuate Solutions also programmed in conjunction with oxion ag the bidirectional interface for the new ERP software, oxaion, which has been deployed throughout the Lindner Group and which runs absolutely without a hitch. The replacement of the existing ERP solution above all provided the opportunity for the workforce in Ostrov, two years ago, to go out and find a new CAD/CAM system. The key objective was the integration of the variant configurator, which oxaion had improved at the request of Lindner specifically for doors, in order to be able to use the door characteristics defined in the ERP system directly for the CAM programming. This was also previously possible, yet with the restriction that the operators had to complete the 3D manually in the old programming environment, since this was a purely 2D system. The use of a 3D system offered the promise here of still greater integration, according to Mr. Fritz.
The project team scrutinized various 3D Systems, and shortlisted two of them. "Although other suppliers had more experience in wood processing, we opted for TopSolid’Wood and collaboration with AdeQuate Solutions, since the software, in our opinion, offered greater potential," says Frank Roeder, who handles administration of the ERP installation in the group. "We wanted a solution that other subsidiaries could also use in the future; for example, object design, as used in ship fitting. Also in TopSolid’Wood’s favour were the powerful functions for the visualization and simulation of the CAM machining."
Powerful CAD functions
The operators needed a CAM system with comprehensive CAD functions in order to be able to design the 3D door models so that they could be controlled by entering parameters. First and foremost among these operators are the two system administrators, who handle the mapping of the range of variants in the 3D system. They first of all populate a library with parametric door elements (edge band, frame, middle layers, etc.) that can be used for the various door types via positioning elements and references in the templates. The elements are linked together via parametric relations and they inherit certain characteristics. The door type and door dimensions determine, for example, the size and strength of the built-in frame, which again determines the size of the panels for the middle layers.
The templates concern in principle generic basic models of the various blanks, which can be adapted according to customer requirements through entering parameter values. In all, there are approximately 70 different blanks; for example, for single or double leaf doors, with or without a glazing aperture, with top panel or fanlight, with or without jambs, with flush-closing door leaf or a particular rabbet geometry, etc. Flush-mounted glazing, concealed hinges and locks with control technology are further design characteristics that influence the form of a door. They also differ, naturally, in terms of their internal construction, depending on whether they are designed for fire, radiation or noise protection.
The customer-specific form of a given project door is recorded in the variant configurator of the ERP system, so that employees involved in work preparation do not have to enter all 400 parameters since many fields are automatically filled in via the predefined rules. A traffic light system signals which characteristics are fully defined or still need to be defined so that the configuration can be technically implemented. The parameters are transferred at the touch of a button in XML format to TopSolid’Wood, in order to generate, with the aid of the corresponding template, a 3D model of the desired door, which may if necessary still be adapted interactively.
Integrated CAD/CAM process chain
Lindner has built up a closed process chain for wood processing, rare to find with such a level of integration. The data exchange between the ERP system and the CAD/CAM system is no one-way street. Parts lists and work plans can be derived from the door models and mirrored back over the bidirectional interface to the ERP system. "We originally wanted to create the parts lists in oxaion, but then we realised that it was more efficient to generate them as a by-product, so to speak, of the 3D model in TopSolid’Wood," says Kai Müller from system administration. A general work plan is stored in the ERP system with all possible work processes and the machining times, from which the work processes for the job in hand are filtered on the basis of the parameters from the CAD/CAM system.
Based on the customer-specific forms of the door models, the employees in work preparation generate the NC programs for the mechanical machining using TopSolid’Wood Cam, taking as reference certain templates, for the basic formatting of the blanks, for example. These templates contain the machining strategy for a completed door, tailored to match the specific requirements of Lindner: "When doing the basic formatting, we can't just trace the door with the milling cutter, we have to take care with the grain when machining to prevent the wood from splitting. If it runs from top to bottom, the top edge is pre-milled with a counter clockwise tool in the opposite direction, and only then machined with the main tool," explains system administrator, Maximilian Kreilinger, who produced the template.
At present, the system administrators are busy mapping components such as fittings, locks, hinges and floor seals in TopSolid’Wood, and storing the corresponding machining cycles. Their positioning in the door determines at which point of the blank the recess is integrated and how it is to be machined. One of the desires for improvement expressed by the operators is the possibility to summarize the machining operations and organize them in a hierarchical tree structure. "Not only would that offer greater clarity for many work processes, but it would also make it possible to mask entire blocks, so that you could, for example, leave one side of the door entirely unworked," Mr. Müller explains, to which Mr. Kreilinger adds: "It would also be practical to be able to organise parameters in alphabetical order, irrespective of the chronological sequence in which they are were created. Otherwise, when there are 300 parameters, it becomes difficult to search through them all."
Reducing the time spent on programming
In order to be able to react flexibly to desires for change from customers, the prepared CAM files with the machining operations are not immediately post-processed. The machine operators only generate the NC code for the machining operations when the job arrives at the machining centres. This procedure also has the advantage that technological improvements, for example, on account of the use of new tools, do not need to be reproduced in multiple NC files, and the machining can if necessary be transferred more quickly from one machine to another. Already executed programs are stored with the job, in order to be able to demonstrate precisely the measurements with which the door in question has been delivered.
The switch to the new CAD/CAM solution has contributed to the reduction of the programming times at Lindner, since many parameters are today already entered in the ERP system and can be used end-to-end throughout the process. At the same time, process security has been improved enormously. Customers can obtain a better image of the desired door, since if necessary they can rapidly be provided with a 3D model, making life so much easier for customer advisers.
The Ostrov-based door specialists save costs above all on system administration, since they can use the resources of the parent company, and this eliminates the costs of maintenance and support for its own ERP installation. There are also possibilities for leveraging synergies in other areas too: "The CAD/CAM solution is scalable," says Mr. Fritz. "Colleagues in other sister companies have expressed concrete interest in it." Concrete indeed: Lindner Objektdesign GmbH has already opted for TopSolid'Wood and is currently launching the first training sessions. For this, AdeQuate Solutions will be integrating a 5-axis machining centre from Homag.
Meer informatie nodig
EEN VRAAG OVER ONZE PRODUCTEN OF OPLOSSINGEN?
Vind uw dichtstbijzijnde verkooppuntContacteer onsVraag een offerte aan