27 May 2010
A crise económica fez com que muitos projectos de TI parassem. Não foi esse o caso na Koenig & Bauer. Apesar de uma quebra nas encomendas, da redução do horário de trabalho e de uma série de cortes nos postos de trabalho, o famoso fabricante de prensas conseguiu implementar a mudança planeada para o sistema de fabrico assistido por computador TopSolid'Cam praticamente dentro do prazo. Graças ao TopSolid, os empregados que estão envolvidos na programação NC têm agora um desempenho ainda mais eficiente, de modo a estarem na melhor posição possível para a próxima vaga de encomendas.
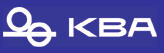
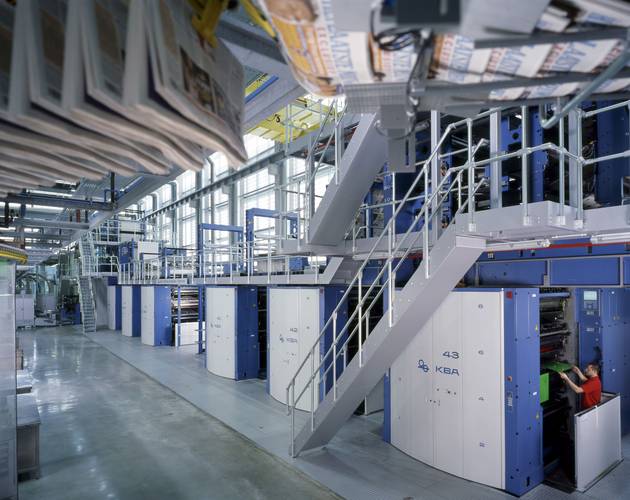
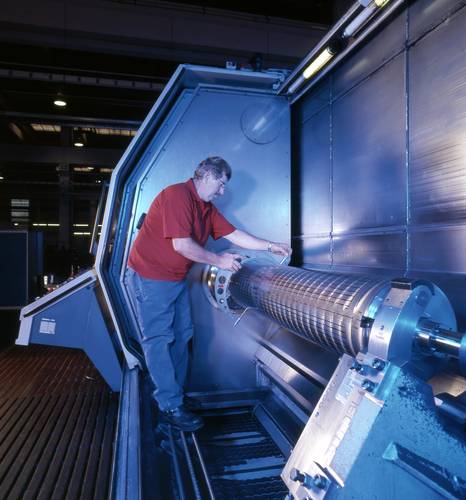
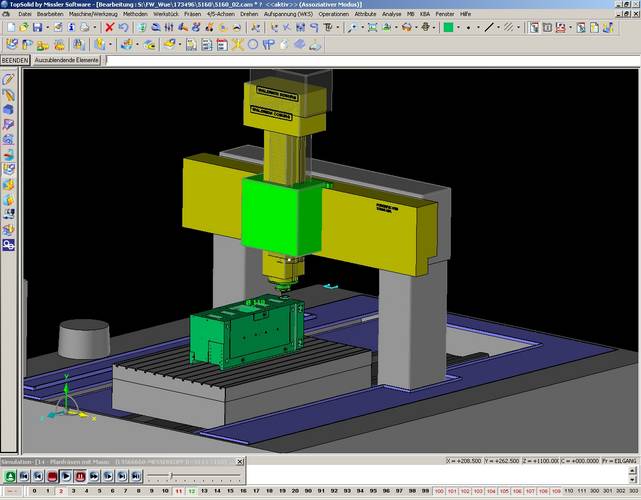
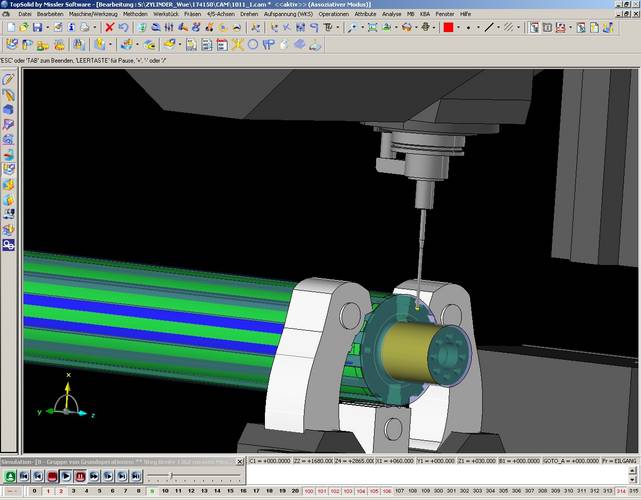
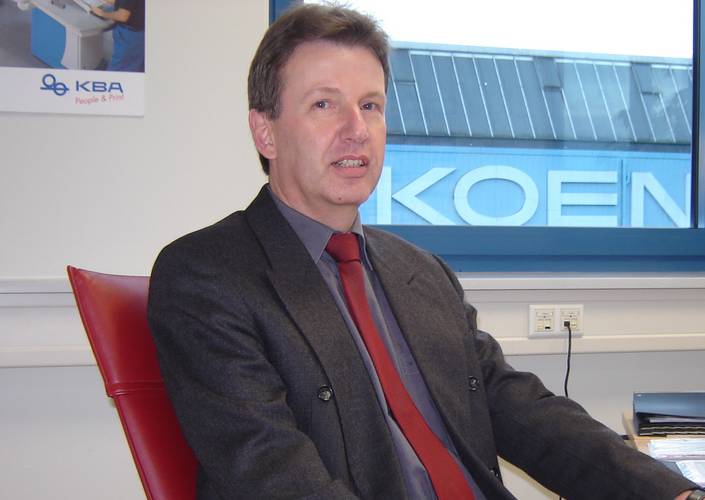
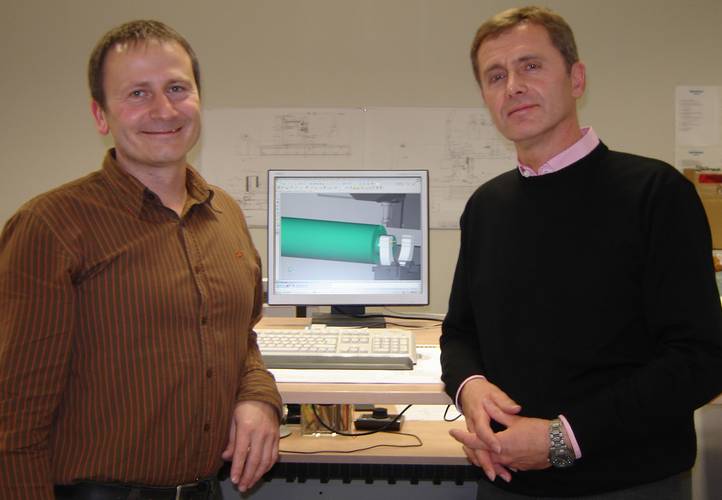
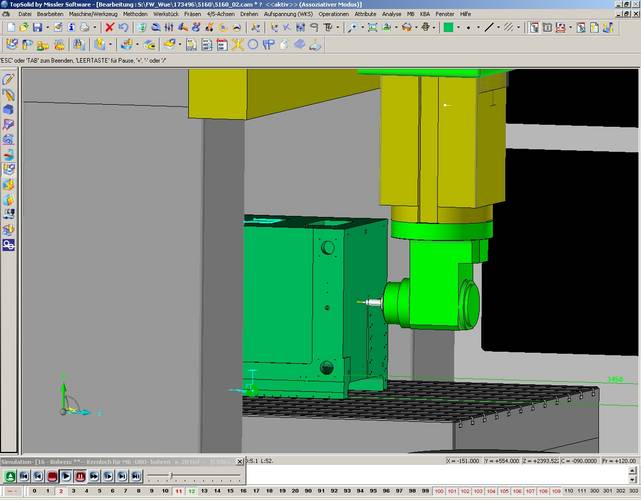
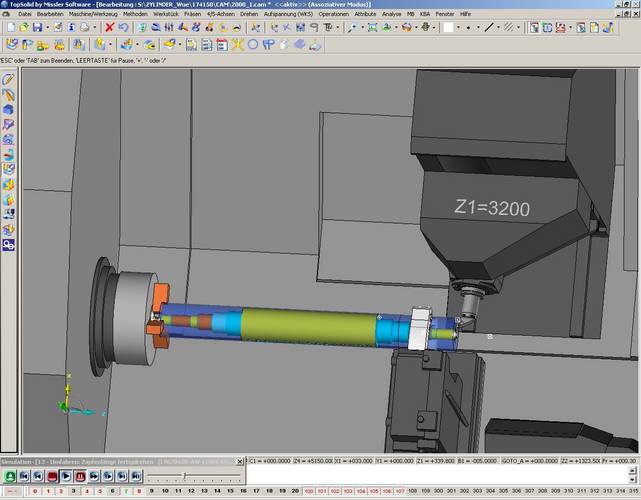
A Koenig & Bauer passou por um mau bocado em 2009. Só nos primeiros três trimestres, o fabricante de prensas, dependente da exportação, teve de absorver uma quebra de encomendas superior a 30%. No entanto, graças a ajustamentos de capacidade e a outras medidas de poupança de custos, espera-se poder apresentar resultados equilibrados no final do ano. A Koenig & Bauer emprega atualmente cerca de 7000 pessoas em todo o grupo. A empresa-mãe do grupo é a Koenig & Bauer AG (KBA), fundada em 1817, com fábricas em Würzburg, Frankenthal, Radebeul e Trennfeld. Estreitamente ligada ao grupo encontra-se a fábrica de máquinas KBA-Mödling AG na Áustria, que fabrica as suas próprias máquinas de impressão de notas e componentes para prensas planas, bem como uma série de outras filiais no país e no estrangeiro.
O grupo KBA é um dos maiores fabricantes de prensas do mundo e o principal fabricante de prensas offset de grande formato, bem como de prensas de impressão de embalagens, jornais e latas. A extensa gama de produtos da empresa, que abrange desde a impressão de jornais e listas telefónicas até à impressão digital, passando pela impressão offset folha-a-folha e pela impressão offset em rede comercial, proporcionou um certo grau de estabilidade durante a recessão económica. Consequentemente, as encomendas de impressoras offset planas já começaram a aumentar um pouco no verão de 2009, apesar de ainda não se vislumbrar qualquer melhoria para os sistemas de impressão específicos do cliente e mais dispendiosos para jornais e impressoras offset rotativas comerciais. As grandes impressoras rotativas são fabricadas principalmente na fábrica de Würzburg, que também tem a sua própria fundição.
No entanto, os trabalhadores de Würzburg têm estado bastante ocupados nos últimos meses: "O nosso espetro de peças tornou-se significativamente maior e mais diversificado, uma vez que a crise nos obrigou a recorrer a mais insourcing, de modo que atualmente fabricamos nós próprios peças que anteriormente teríamos comprado noutras instalações. Atualmente, fabricamos internamente todas as peças fundidas de maiores dimensões", explica o Dr. Andreas Göttker, Diretor de Fabrico e Fundição da KBA em Würzburg. Nos novos centros de maquinação de pórticos, que entraram em funcionamento no final de 2008, podem ser maquinadas com elevada precisão peças fundidas de grandes dimensões, tais como estruturas laterais e caixas de subestrutura. A fim de alcançar a máxima utilização da capacidade, a KBA também opera como um fabricante contratado.
IMPLEMENTAÇÃO DO CAM
Para além do seu trabalho diário normal, os programadores NC em Würzburg e os seus colegas em Frankenthal, Radebeul e Mödling - cerca de 50 utilizadores no total - precisavam de aprender as funções do novo sistema de programação. Em maio de 2006, a KBA tinha decidido substituir o antigo sistema de programação (Bravo NCG) pelo TopSolid'Cam. O que se revelou decisivo na escolha do TopSolid, em oposição a uma solução CAM ligada ao sistema de design NX, foi o facto de o TopSolid oferecer um melhor suporte para os centros multifuncionais de torneamento-furação-fresagem da WFL Millturn Technologies, utilizados pela KBA em todas as suas instalações, em particular para o fabrico de cilindros. Além disso, o que também desempenhou um papel importante na decisão foi o apoio personalizado oferecido pelo fabricante do sistema e pelos seus parceiros de vendas regionais.
A implementação da nova solução CAM em Würzburg e Frankenthal foi efectuada pelo parceiro da Missler Software, NCDATA AG. Para poder ligar o parque de máquinas em ambos os locais, foram programados cerca de 40 pós-processadores para a KBA. Estes geraram os modelos 3D das máquinas no TopSolid'Cam com base nos dados correspondentes do fabricante ou, caso não existissem tais dados, construíram-nos de raiz e mapearam a cinemática da máquina nos modelos, sendo este o pré-requisito para uma programação e simulação fiáveis dos percursos das ferramentas. Além disso, ligaram a administração das ferramentas TDM através de uma interface ao novo sistema CAM, de modo a que os utilizadores pudessem aceder aos parâmetros das ferramentas existentes e aos valores de medição a partir das definições por defeito ao efectuarem a programação.
As definições TDM são utilizadas de duas formas no TopSolid'Cam para gerar a geometria das ferramentas, como explica Rainer Wiesner, programador NC: "Por um lado, geramos modelos através dos quais as ferramentas são construídas dinamicamente, com base nas definições. Isto funciona bem com ferramentas rotativas de perfuração e fresagem, que têm uma estrutura relativamente simples. Para as ferramentas de torneamento, continuamos a manter as configurações no TDM, mas geramos um modelo 3D interactivamente no TopSolid, para que tenhamos a geometria correcta para a simulação. Ou então, recebemos os modelos diretamente dos fabricantes de ferramentas." A interface entre o TopSolid'Cam e o TDM é bidirecional, o que significa que o software CAM comunica as ferramentas utilizadas ao sistema de administração de ferramentas, que é utilizado pelos programadores para preencher e manter as listas de ferramentas.
AVALIAÇÃO DOS DADOS DOS FUROS DE SONDAGEM
Um requisito essencial da nova solução CAM era a possibilidade de importar, juntamente com a geometria CAD, informações específicas de fabrico para o TopSolid'Cam e utilizar estas informações para a automatização da maquinação NC. Isto é particularmente importante para o fabrico das gigantescas armações laterais, que incorporam entre 1000 e 2000 furos, a maioria dos quais são repetitivos. A Missler Software escreveu um programa adicional correspondente para a KBA que permite avaliar as listas de furos do NX no TopSolid'Cam e visualizar informações como o tipo de furo, diâmetro, profundidade do furo, tipo de maquinação ou tolerância diretamente com base no modelo 3D subjacente. Com base nestas informações, os furos podem então ter métodos de maquinação automaticamente predefinidos atribuídos.
Enquanto que anteriormente os programadores tinham de simular a geometria CAD na sua aplicação CAM para poderem gerar os seus programas NC, agora podem importar diretamente os dados Parasolid e associá-los às informações de fabrico do NX. O TopSolid oferece funções CAD poderosas para a preparação de modelos prontos a serem fabricados; por exemplo, é possível deslocar um orifício de perfuração em fracções de milímetro para garantir que está corretamente centrado. É possível tornar a geometria "burra" um pouco mais inteligente, por exemplo, colocando duas superfícies uma em relação à outra e modificando assim a medição resultante", salienta o Sr. Wiesner.
O Dr. Göttker ainda não está totalmente satisfeito com o processo de mudança, ou seja, com a possibilidade de atualizar e/ou adaptar programas NC existentes através de alterações de design com o mínimo esforço. Muitas vezes, os designers utilizam componentes existentes como modelo para novos projectos, fazendo apenas pequenas alterações. A dificuldade reside em comunicar estas alterações de geometria e de dados de forma selectiva ao TopSolid'Cam. É verdade que o sistema possui funções poderosas para comparações de geometria, para que se possa identificar, por exemplo, quais os furos que foram deslocados. No entanto, o utilizador não pode integrar as alterações com o toque de um botão no seu programa NC, uma vez que as informações de perfuração e a geometria podem nem sempre corresponder corretamente, o que significa que são necessárias inspecções manuais. "O que também gostaríamos era de poder alinhar e modificar seletivamente as listas de furos, mas isto ainda não foi implementado", diz o Dr. Göttker.
Entretanto, a Missler Software implementou outro dos pedidos de melhoria da KBA: a longa lista de operações de maquinação para uma estrutura lateral pode ser subdividida no gestor de maquinação e agrupada de forma diferente. Isto facilita a atualização e otimização subsequentes dos programas NC, por exemplo, se a pessoa que opera a máquina alterar uma determinada configuração de broca e comunicar esta alteração aos colegas na programação CAM. Anteriormente, os programadores teriam de percorrer todo o programa meticulosamente para localizar todos os pontos em que a configuração alterada ocorre.
SATISFEITO COM O PROGRESSO DO PROJECTO
Na KBA estão muito satisfeitos com a forma como a NCDATA AG tem conduzido o projeto. O planeamento original previa a transferência dos vários grupos de máquinas em quatro fases até ao final de 2009 para a programação com o TopSolid'Cam. "Agora temos todos os pós-processadores internamente, mesmo que ainda não tenham sido todos testados e implementados de forma produtiva", explica Klaus Rüger, Diretor de Programação NC e Design de Equipamento de Produção na KBA. "Os outros locais têm de recuperar algum atraso, mas isso deve-se principalmente a flutuações na carga de trabalho e no número de funcionários. No entanto, todos os utilizadores receberam formação e já estão habituados a programar diariamente com o novo sistema CAM."
Só em Würzburg, a NCDATA AG requalificou 20 funcionários nos últimos três anos, incluindo dois operadores de máquinas que prestam apoio à programação em alturas de pico de capacidade. Dois utilizadores avançados, formados desde o início, ocupam-se agora da programação de métodos, da formação e do apoio: "Descobrimos que os utilizadores precisam, em primeiro lugar, de se habituar ao sistema antes de receberem qualquer formação adicional sobre o mesmo. Realizamos a formação em design internamente como uma forma de formação no local de trabalho, porque isso nos permite responder mais eficazmente às questões e problemas individuais dos utilizadores", diz o Sr. Wiesner, um dos dois utilizadores avançados.
Dependendo da recetividade do empregado e do nível de complexidade da máquina a ser programada, pode levar até três ou quatro meses até que o utilizador domine perfeitamente o novo sistema CAM, como explica o Sr. Wiesner: "O âmbito funcional do software é tão abrangente que qualquer pessoa que não esteja a trabalhar continuamente com o sistema tem de se voltar a familiarizar com ele se não o utilizar há vários meses. Isto não é propriamente fácil para os nossos operadores de substituição, que só são afectados à programação em caso de estrangulamento da capacidade. Felizmente, o processo de familiarização é bastante rápido graças à facilidade de operação, em particular quando já se está familiarizado com as máquinas e as peças a serem programadas."
MAIS SEGURANÇA NA PROGRAMAÇÃO
Do ponto de vista do utilizador, o ponto forte do novo sistema CAM é o suporte de programação gráfica/visual. O utilizador vê não só a geometria do seu componente e/ou das peças em bruto, mas também todo o ambiente da máquina, incluindo o gabarito e as ferramentas, bem como os modelos 3D. Após cada etapa de maquinação, é possível atualizar o modelo da peça em bruto para verificar onde e quanto material resta. "A execução da maquinação no modelo de volume é particularmente vantajosa quando temos de programar peças externas que são fabricadas por nós no âmbito do fabrico por contrato", afirma o Sr. Rüger. "O novo sistema CAM foi, portanto, muito bem recebido. Tenho a certeza de que nenhum dos nossos funcionários estaria interessado em voltar à solução antiga."
"A forma das peças complexas pode ser estabelecida muito mais rapidamente e sentimo-nos mais seguros na maquinação porque podemos ver cada passo individual da maquinação", explica o Sr. Wiesner, que continua a dizer: "A nossa confiança nos programas que geramos com o TopSolid'Cam ainda precisa de ser consolidada, é claro. Quanto mais tempo trabalharmos com o sistema, mais seguros nos sentiremos."
A utilidade da nova solução CAM está agora a causar uma impressão na KBA, mesmo que isso ainda não possa ser quantificado com precisão. "Já poupamos muito tempo pelo simples facto de não termos de gerar a geometria de novo para podermos programar a peça", diz o Sr. Rüger. "Nas peças complexas, a programação também é mais rápida graças aos automatismos e aos métodos. Infelizmente, ainda estamos a perder tempo com as alterações porque ainda não descobrimos a melhor forma de trabalhar."
Graças ao apoio profissional da NCDATA AG, a KBA negociou com sucesso a mudança do sistema de programação CAM, mais ou menos dentro do prazo, e atualmente trabalha de forma produtiva em todas as instalações com o novo sistema CAM. O Dr. Andreas Göttker está confiante de que a produtividade dos utilizadores continuará a aumentar assim que o seu conhecimento do sistema for estabelecido e os processos de mudança se tornarem cada vez mais automatizados e/ou mais eficazmente suportados pelo software.
Precisa de mais informações
PERGUNTA SOBRE NOSSO
PRODUTOS OU SOLUÇÕES?
Encontre o ponto de vendas mais próximo Contate-nos Obter uma cotação