24 July 2012
O cubo de câmbio de 14 velocidades da Rohloff é, sem dúvida, bastante familiar para qualquer ciclista de montanha entusiasta, mas muito poucos deles estariam familiarizados com o nome L. Richter. A empresa sediada na cidade alemã de Lichtenfels, em Hesse, fabrica as complexas peças de alumínio para acoplamentos que atendem aos mais altos requisitos de qualidade e precisão. A usinagem millturn é programada em modernos centros de usinagem usando o TopSolid'Cam da Missler Software, o que reduz consideravelmente os tempos de ferramental.
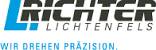
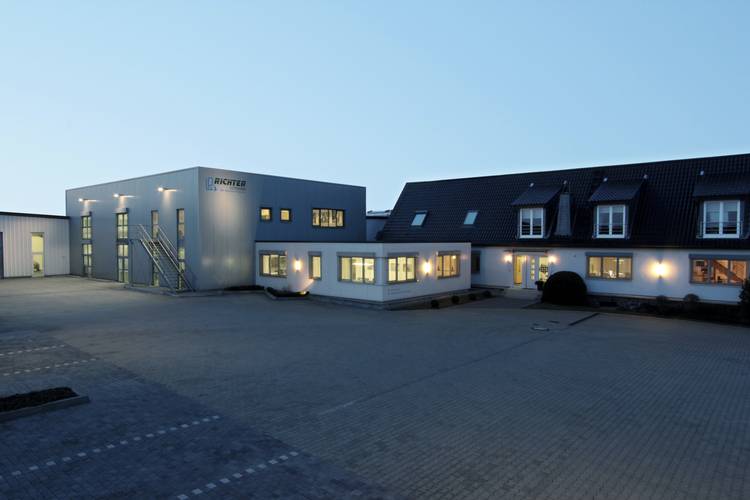
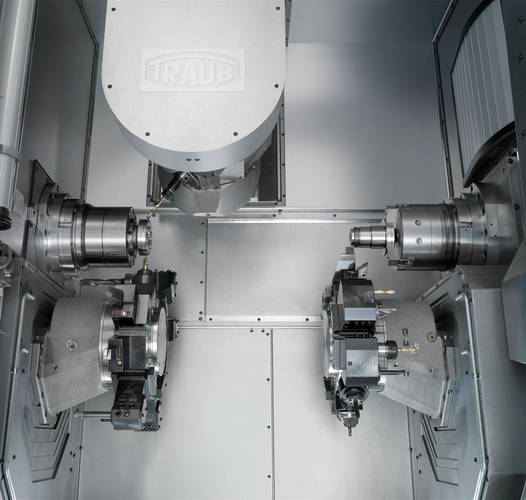
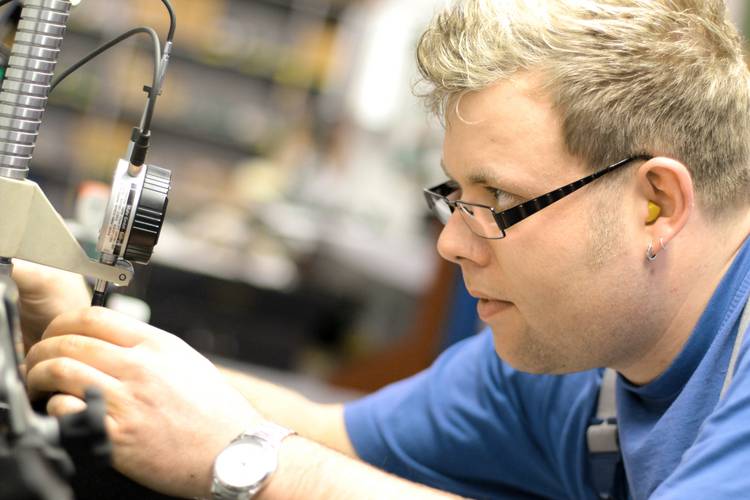
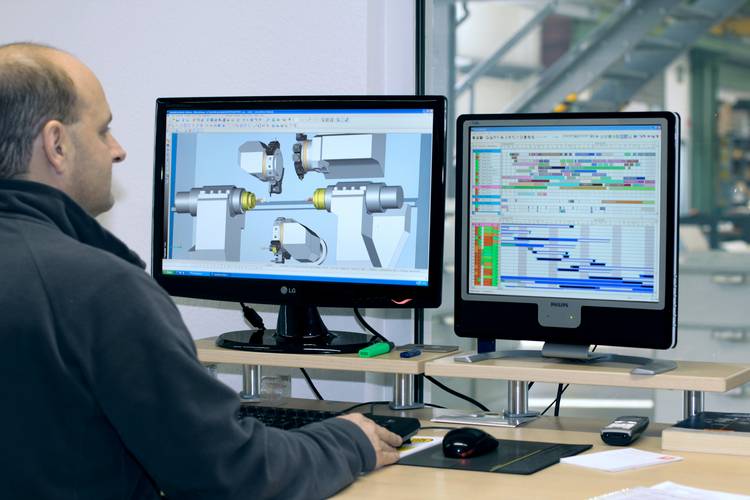
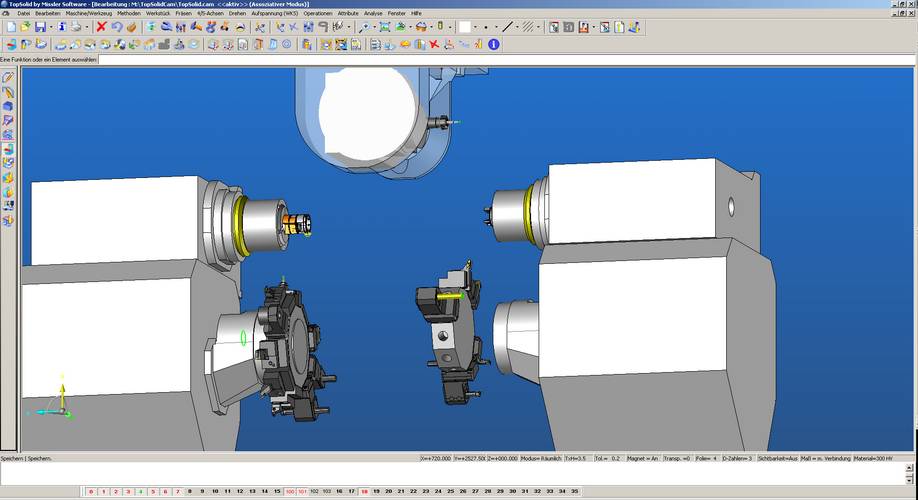
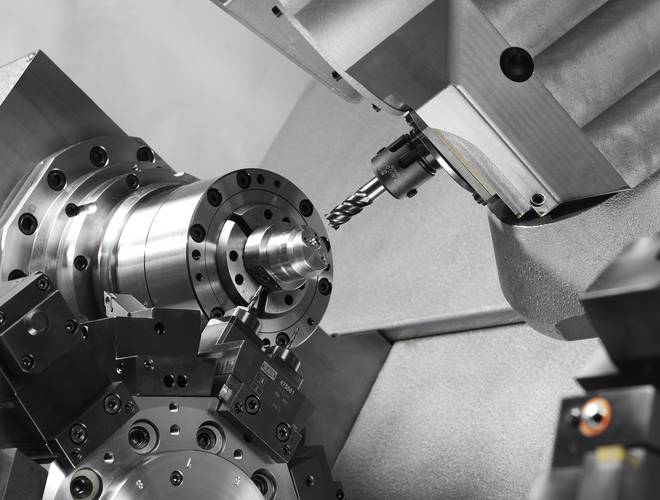
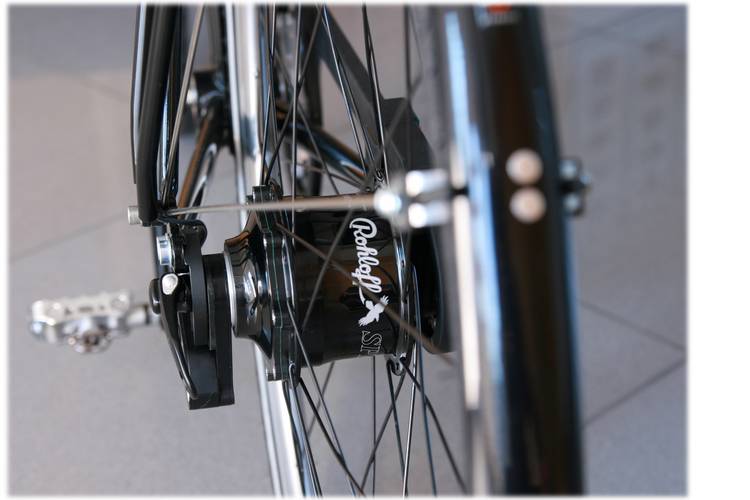
L. Richter KG, de Lichtenfels, é uma daquelas empresas que demonstram que, mesmo na Alemanha, é possível permanecer competitivo como uma pequena empresa de manufatura se você se especializar de forma criteriosa. Fundada há quase 50 anos como uma tradicional fábrica de moldagem de metais, que produzia peças simples de latão em grandes quantidades de lotes, essa empresa familiar com atualmente 25 funcionários se desenvolveu por meio da implementação de modernas máquinas CNC e tecnologia de programação CAM para se tornar um parceiro de fabricação reconhecido na produção de peças de precisão complexas feitas de materiais desafiadores. Além do aço inoxidável, a Richter trabalha predominantemente com alumínio, mas também com plásticos.
Para os especialistas em fabricação baseados em Lichtenfels, as peças complexas são peças torneadas que envolvem um alto grau de fresamento. O grau de complexidade pode ser medido com base nos tempos de usinagem. No novo centro de torneamento da Traub TNX65/42, equipado com um fuso principal e um contrafuso, duas torres de ferramentas, um fuso de fresamento giratório e um magazine de correntes, uma peça de aço inoxidável pode agora ser completamente usinada. Embora as cerca de 50 ferramentas de torneamento e fresamento estejam trabalhando simultaneamente ou sobrepostas em ambos os fusos, a usinagem leva 24 minutos. "Normalmente, uma peça torneada fica aqui de 2 a 3 minutos", diz Matthias Richter, o chefe da segunda geração da empresa.
QUALIDADE CONSISTENTE DAS PEÇAS
A Richter trabalha para clientes de vários setores, que geralmente não têm suas próprias instalações de fabricação e, para muitos, é até mesmo o único fornecedor de determinados componentes. "Confiabilidade e qualidade são o que nossos clientes valorizam em nós", diz Richter. "Nosso ponto forte é a combinação de peças e materiais complicados, o cumprimento de cronogramas e a qualidade consistente. Nossos padrões autoimpostos geralmente são mais altos do que os ditados pelos clientes, principalmente no que diz respeito ao acabamento de superfícies." Precisão visível e mensurável: para verificar a precisão dimensional das peças, a empresa estabeleceu sua própria garantia de qualidade com suporte de computador. Isso significa que o número de devoluções é praticamente zero.
O uso de novas tecnologias desempenha um papel fundamental no sucesso da empresa, juntamente com a qualificação dos funcionários. A primeira máquina CNC - uma Traub - foi adquirida em 1979 pelo pai do Sr. Richter, para a usinagem de peças e materiais complexos. Desde 1989, todas as máquinas são programadas off-line, a fim de reduzir ao mínimo o tempo de inatividade. "A aquisição do primeiro sistema de programação da Index, que ainda funcionava com computadores VAX, representou um grande investimento para uma empresa do nosso porte", lembra o chefe da empresa, ele próprio um programador. Há três anos, a empresa substituiu a solução 2½-D pelo sistema CAD/CAM 3D TopSolid'Cam, a fim de explorar melhor o potencial das máquinas de múltiplos eixos e reduzir os tempos de ferramental. A nova solução CAD/CAM está sendo usada atualmente em três estações de trabalho.
Tempos curtos de ferramental são um critério importante para a empresa, a fim de reagir de forma flexível aos desejos dos clientes e poder fabricar peças em lotes pequenos, mantendo a relação custo-benefício. "Nas máquinas mais complexas, fabricamos, por lote, de 250 a no máximo 5.000 unidades; nas mais simples, lotes ainda menores", explica o Sr. Richter. "Aqui temos pouquíssimas máquinas que funcionam por mais de 10 dias em um determinado trabalho. Normalmente, suas ferramentas são trocadas todos os dias, às vezes até várias vezes por dia."
BENEFÍCIOS DA NOVA MÁQUINA TRAUB
O parque de máquinas da empresa inclui, além do novo centro de torneamento de fresas Traub TXN65/42, tornos automáticos Index C100, equipados com três torres de ferramentas para a fabricação de grandes volumes de lotes, e vários centros de usinagem de 4 eixos Index G200, cada um configurado com dois eixos-árvore e torres, equipados com ferramentas acionadas para torneamento e fresamento combinados. Para a usinagem de peças menos complexas, eles também têm tornos automáticos mais simples. Os operadores da Richter são treinados de forma tão abrangente que podem operar todas as máquinas, embora a Traub - ao contrário das máquinas Index - não esteja equipada com um controlador Siemens, mas com um TNX ou Mitsubishi.
A aquisição do novo centro de usinagem significou custos adicionais para o fuso de fresamento extra, mas eles se pagaram em todos os aspectos. A empresa agora é capaz de realizar a usinagem completa de peças torneadas com requisitos complexos de fresamento. "Demos um salto do espectro de peças para dimensões totalmente novas e nos diferenciamos ainda mais da concorrência", afirma Richter. "Os prestadores de serviços que usam uma máquina como essa são poucos e raros."
A Richter já estava usando as máquinas Index para usinagem completa, mas cada vez mais se deparava com limites com as ferramentas acionadas nas torres rígidas, por exemplo, ao usinar furos e roscas íngremes, ou porque não era possível alojar tantas ferramentas quanto necessário nas torres. "As ferramentas acionadas também têm a desvantagem de serem consideravelmente mais caras do que as ferramentas HSK normais, de se desgastarem mais rapidamente, de levarem mais tempo para serem trocadas e de não atingirem as mesmas velocidades de rotação", explica o Sr. Richter. "Para peças torneadas que envolvem uma grande quantidade de fresamento, somos, portanto, mais rápidos com a Traub, tanto com as ferramentas quanto com a usinagem, o que compensa a maior taxa horária da máquina."
ENCONTRAR O PARCEIRO CERTO
Todas as máquinas são conectadas por meio de pós-processadores de alto desempenho ao TopSolid'Cam e, com exceção de algumas poucas operações, são fornecidas com o código NC do novo aplicativo CAM. A conexão com o parque de máquinas foi realizada pelo parceiro de vendas da Missler Software, AdeQuate Solutions, que não só programou os pós-processadores, mas também gerou os modelos de máquina 3D para a simulação e, se disponibilizados pelo fabricante, mapeou a cinemática nos modelos. Para minimizar o esforço de manutenção do software, a Richter dispensa em grande parte as adaptações específicas do cliente aos pós-processadores, com exceção de alguns ciclos de usinagem que não estavam contidos no padrão.
A programação do pós-processador para o centro de torneamento da Traub foi um território virgem para a AdeQuate Solutions. Isso envolveu a necessidade de os programadores levarem em conta várias particularidades do controle TNX; por exemplo, o fato de que a correção do raio de corte durante a usinagem no contraeixo é calculada em sentido inverso, o que inicialmente causou problemas de contorno. No entanto, o verdadeiro desafio consistiu em mapear as diversas opções de usinagem. O fuso de fresagem, por exemplo, não só pode girar 180°, mas também pode girar em seu próprio eixo e travar, de modo que é possível, ao girar com duas ferramentas deslocadas, carregar uma ferramenta de corte adicional. Além disso, é possível apoiar peças torneadas mais longas em um cabeçote móvel fixado na torre do contrafuso.
"Para nós, como fornecedores, a máquina é ótima porque pode ser implementada de várias maneiras, mas isso também deve ser suportado pelo pós-processador", explica o Sr. Richter, que, a esse respeito, elogia muito a competência da empresa de software sediada em Lahr e a qualidade do serviço: "Todos os pós-processadores puderam ser usados imediatamente, de modo que pudemos programar com eles imediatamente e, se uma operação não tiver o suporte ideal, receberemos um pós-processador atualizado em 24 horas. Nós realmente recebemos o melhor suporte possível da AdeQuate Solutions."
SELEÇÃO DO SISTEMA NA SEGUNDA TENTATIVA
Se o fornecedor de sistemas baseado em Lahr não existisse, a empresa provavelmente teria optado por uma solução CAM diferente. Na seleção do sistema do processador, o TopSolid foi inicialmente rejeitado, pois foi apresentado por outro fornecedor. Embora o software oferecesse o melhor suporte para torneamento e fresamento de todos os sistemas considerados, durante a apresentação do sistema, ele pareceu aos operadores ser muito complicado de usar. Então, graças a uma dica de um conhecido, foi feito contato com a AdeQuate Solutions. "Inicialmente, superestimamos o esforço necessário para a modelagem 3D. Quando um funcionário da AdeQuate Solutions nos demonstrou, em uma peça complexa, como era simples criar o modelo e programar as etapas de usinagem com base em um desenho 2D, ficamos bastante surpresos", diz o Sr. Richter. "Isso mostra que você não precisa apenas do sistema certo, mas também do parceiro certo."
As funções CAD integradas são um ponto forte do TopSolid'Cam, como o Sr. Richter continua demonstrando. Elas são importantes para os programadores CAM porque eles não recebem dados 3D de todos os clientes e precisam inicialmente modelar as peças para poder fazer qualquer tipo de programação. No entanto, mesmo que recebam dados 3D, muitas vezes é necessário fazer adaptações na geometria, pois os projetistas do cliente normalmente criam seus modelos com dimensões nominais sem levar em conta as tolerâncias de fabricação. Embora o TopSolid ofereça um bom suporte para essas adaptações, às vezes é mais eficiente recriar completamente o modelo para poder explorar os benefícios da associatividade entre os modelos CAD e CAM. "Os programas CAM facilitam ainda mais a atualização da geometria caso sejam feitas alterações", explica o Sr. Richter.
Mesmo que os usuários precisem, em primeiro lugar, gerar um modelo 3D, o que, graças a essa rotina cada vez mais frequente, também ocorre mais rapidamente do que há dois anos, eles economizam tempo na programação das operações de torneamento e fresamento. Tudo o que eles precisam fazer é clicar nas superfícies a serem usinadas, selecionar a ferramenta e definir os parâmetros de corte. Anteriormente, eles tinham que transferir dimensões e pontos de corte, em parte manualmente, a partir do desenho CAD, o que consumia um tempo relativamente longo. Acima de tudo, eles podem proceder muito mais rapidamente com as alterações, pois não precisam recriar os programas CAM (ou mesmo apenas partes deles), basta recalcular. "Se os dados 3D do cliente não estiverem limpos, hoje não hesitamos em simplesmente retrabalhar os dados", diz o Sr. Richter. Às vezes, os especialistas em fabricação disponibilizam seus dados de modelo para clientes que ainda não estão implantando nenhum sistema 3D.
OTIMIZAÇÃO DA USINAGEM DE MÚLTIPLOS EIXOS
A cadeia de processos CAD/CAM integrada também traz grandes benefícios em termos de garantia de qualidade, como diz o Sr. Richter. As medidas e as tolerâncias definidas no modelo ou no desenho podem ser transmitidas em formato DXF para o software de qualidade auxiliado por computador da empresa e usadas para a geração automática dos planos de teste. Cada peça na Richter é 100% testada e documentada antes de ser liberada para a produção em série. Os finalizadores são responsáveis pela qualidade de suas peças e também medem as dimensões críticas em amostras retiradas da produção em série. "Programamos a usinagem, em parte, combinando-a com a geometria a ser examinada e, assim, garantimos a alta confiabilidade do processo", enfatiza o Sr. Richter.
Os programadores também usam as funções de CAD para incorporar ferramentas, porta-ferramentas e sistemas de fixação, um a um, no TopSolid'Tool. Inicialmente, isso exigiu um grande esforço, mas hoje está valendo a pena, como explica o Sr. Richter. Graças ao mapeamento abrangente do ambiente da máquina, os usuários podem simular e otimizar de forma confiável seus programas CAM no computador. A nova solução CAM oferece a possibilidade, entre outras coisas, de calcular e minimizar os tempos de operação da máquina por meio da organização ideal das etapas de usinagem no eixo principal e no contraeixo com o auxílio de um fluxograma gráfico. Anteriormente, os programadores tinham que fazer isso de cabeça e, às vezes, só depois de executar o programa, descobriam que ele não funcionava como planejado.
Graças à simulação e à visualização da usinagem CAM, as máquinas Richter são hoje usinadas consideravelmente mais rápido. Isso se deve, acima de tudo, ao fato de que os programas executados nas máquinas são tecnologicamente impecáveis e funcionam de forma totalmente suave. Anteriormente, havia muitas dificuldades de adaptação que só podiam ser eliminadas durante a execução e, para os operadores de máquinas, não era fácil entender o que a máquina estava fazendo ou o que realmente deveria estar fazendo. Agora eles podem dar uma olhada no computador e, portanto, podem ter mais confiança quando se trata de rodar. "Com peças complexas, graças à preparação ideal dos programas, ganhamos de 25 a 30% nos tempos de ferramental", diz Richter. "A sincronização ideal da usinagem de múltiplos eixos também contribui para a minimização dos tempos de operação da máquina."
Precisa de mais informações
PERGUNTA SOBRE NOSSO
PRODUTOS OU SOLUÇÕES?
Encontre o ponto de vendas mais próximo Contate-nos Obter uma cotação