14 September 2010
O TopSolid'Cam reduz o tempo de operação da máquina.
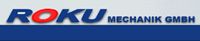
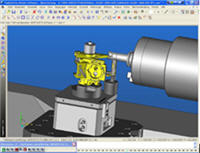
Para a ROKU Mechanik GmbH, uma empresa especializada na usinagem completa de peças A complexas (uma classificação de peças de altíssima qualidade), tempos curtos de operação da máquina são mais importantes do que tempos curtos de programação. Com o TopSolid, a empresa consegue simular e otimizar não apenas os caminhos das ferramentas, mas também a duração da usinagem. O gerente da ROKU, Roland Kuhnhaus, está prevendo uma redução total de custos de pelo menos 50% graças ao uso da solução da Missler Software.
A ROKU Mechanik GmbH, com sede em Unterschneidheim, na Alemanha, é uma empresa de manufatura tradicional que lida com a usinagem completa de componentes complexos com todos os revestimentos de superfície usuais para seus clientes, além de fornecer suporte logístico aos clientes. "Fornecemos peças prontas para instalação diretamente para as oficinas de montagem dos clientes, muitas vezes como conjuntos completos de peças com 200 a 300 peças separadas no compartimento Kanban", explica o gerente da empresa, Roland Kuhnhaus. Nesses casos, a empresa também coordena a aquisição de peças de catálogo e a fabricação de peças de estamparia e a laser que normalmente seriam entregues a subcontratados. A ROKU é especializada na fabricação de "peças A" para a fabricação de veículos, tecnologia de propulsão, aeroespacial, tecnologia médica e indústria óptica, que normalmente são produzidas em lotes de até 10.000 peças por ano. A empresa, que atualmente emprega 140 funcionários, usina a carcaça do eixo de equilíbrio, por exemplo, para os motores de um importante fabricante de automóveis alemão e usina a carcaça de alumínio de câmeras profissionais e microscópios de operação para um fabricante alemão de dispositivos ópticos. Até certo ponto, isso envolve componentes relacionados à segurança que são entregues diretamente à linha de montagem, com altos requisitos de processo em termos de qualidade e confiabilidade.
Para garantir uma transição perfeita do protótipo para a produção em massa, a ROKU fabrica essencialmente peças de protótipo em máquinas de produção em massa, com todos os equipamentos de produção e dispositivos de fixação necessários sendo projetados internamente. "Precisamos ser capazes de acomodar a produção em massa até mesmo de peças altamente complexas em um tempo de resposta tão curto quanto possível", diz Kuhnhaus, ao descrever um dos desafios enfrentados por sua empresa. "Por esse motivo, a fabricação de peças atualmente ocorre em paralelo ao desenvolvimento de peças - peças que podem, se necessário, ser descartadas em caso de erros. Esse é um risco que o cliente está preparado para aceitar a fim de colocar seus produtos no mercado rapidamente."
Nos últimos anos, a ROKU fez muito para padronizar o parque de máquinas, substituindo as muitas fresadoras e tornos diferentes por centros de usinagem altamente complexos, com até oito eixos, para uma remoção abrangente de material, independentemente do material a ser usinado: aço, titânio, alumínio, peças fundidas/forjadas ou plásticos. A variedade de diferentes controladores também foi reduzida para incluir apenas os controladores Fanuc e Okuma. A padronização permite um planejamento de produção flexível, já que os programas e dispositivos CNC podem ser usados em conjunto com praticamente todas as máquinas, embora também sejam necessárias ferramentas CAD/CAM poderosas para explorar totalmente o potencial da máquina. "Se não for possível simular a usinagem visualmente em um computador, a complexidade cada vez maior das peças gera tempo de inatividade da máquina para a execução e troca de ferramentas, e ninguém pode mais se dar a esse luxo", afirma enfaticamente o Sr. Kuhnhaus.
PONTOS FORTES PARA TRABALHOS EM TORNO
Em função da crescente complexidade das máquinas e das peças a serem usinadas, a ROKU optou, no final de 2005, por introduzir um sistema CAD/CAM 3D. Anteriormente, os operadores de máquinas já costumavam preparar a usinagem off-line, mas usando um editor 2D tradicional para os desenhos de fabricação. Isso tinha a desvantagem de que eles não podiam calcular a geometria da peça bruta e a remoção de material, nem reconhecer as bordas projetadas. A análise de colisão é, portanto, importante para o ROKU, pois muitas peças têm formas tão complexas que é necessário desenvolver um aparato especial para fixá-las, o que pode levar a colisões durante o processo de usinagem com o ferramental e o suporte. Foram considerados vários sistemas CAD/CAM que estavam no mesmo nível do TopSolid em termos de programação de fresamento, mas o que acabou sendo decisivo para a escolha do TopSolid foi o excelente suporte para usinagem multifuncional complexa, como Andreas Hammele, gerente de programação CNC, faz questão de enfatizar: "Em máquinas de múltiplos eixos com eixos-árvore duplos, não é mais possível calcular a parada síncrona das operações individuais em sua cabeça. Portanto, estávamos procurando uma solução que nos permitisse simular a sincronização da usinagem no computador, de modo a evitar que tivéssemos que descobrir na própria máquina que a parada não funcionava e, então, ter que reorganizar todas as ferramentas. Também precisávamos de um módulo CAD poderoso para projetar nossos dispositivos."
A solução CAD/CAM integrada da Missler Software agora está sendo executada em Unterschneidheim em seis estações de trabalho de PC, todas com Windows XP. Três delas estão equipadas com o software TopSolid'Design, o módulo TopSolid'Cam ME para programação de fresas de 3 eixos e o módulo de torno TopSolid'Cam, e as outras três apenas com o software CAD. Eles são usados principalmente para o projeto de equipamentos de produção, como diz o Sr. Hammele: "Peças com formas complexas geralmente não podem ser usinadas com dispositivos de fixação padrão e, por isso, para a indústria automobilística, por exemplo, muitas vezes precisamos projetar dispositivos de fixação especiais e instalações de manuseio."
No entanto, a ROKU precisa das poderosas funções de CAD não apenas para o projeto de dispositivos de fixação e equipamentos de produção. Os especialistas em manufatura estão sendo cada vez mais solicitados a apoiar seus clientes no desenvolvimento de produtos e a apresentar propostas sobre como as peças podem ser produzidas de forma mais econômica ou como o peso das peças pode ser reduzido sem a necessidade de operações de manufatura dispendiosas. "O projetista do produto, de fato, muitas vezes não tem ideia de como vamos usinar a peça e, acima de tudo, como vamos montá-la. Os custos de produção de um gabarito de fixação elaborado podem ser reduzidos drasticamente se pudermos influenciar o projeto do suporte da peça", explica o Sr. Kuhnhaus.
SUPORTE COM CLIPES DE VÍDEO GRÁFICOS
A nova solução CAD/CAM foi implementada há cerca de dois anos pelo parceiro de vendas da Missler Software, a AdeQuate Solutions, de Lahr, que também forneceu treinamento para os operadores e continua a fornecer suporte para a solução de problemas até hoje. Os usuários estão muito satisfeitos com o suporte, como Hammele faz questão de enfatizar. Em 24 horas, eles recebem respostas às suas consultas de suporte, geralmente na forma de videoclipes que demonstram a maneira correta de proceder. A ROKU também faz uso do serviço de manutenção remota que o fornecedor de sistemas oferece aos seus clientes. O treinamento básico sobre como usar as funções CAD e CAM levou cerca de dois a três dias para cada um, e os usuários tiveram cerca de quatro a seis semanas para colocar em prática o que aprenderam, antes de embarcarem em vários dias de treinamento avançado. Após cerca de oito semanas, eles já estavam tão familiarizados com o sistema CAD que podiam usá-lo com confiança. A familiarização com a funcionalidade CAM demorou um pouco mais, pois os programadores também tiveram que aprender a incorporar suas ferramentas no TopSolid.
A representação das ferramentas, máquinas e dispositivos de fixação é um pré-requisito fundamental para a simulação realista da usinagem CAM. Hoje, na ROKU, nenhum novo programa de fresamento ou torneamento é gerado sem, ao mesmo tempo, projetar as ferramentas necessárias. Isso envolve o armazenamento de todos os parâmetros de corte para que o tempo de usinagem das operações individuais possa ser calculado com bastante precisão. As máquinas também tiveram que ser modeladas inicialmente no TopSolid, com os operadores da AdeQuate Solutions lidando com a tarefa de representar as sequências de trabalho nos modelos. Eles também adaptaram os pós-processadores para os centros de usinagem Makino e Okuma, muitos dos quais estão em uso na ROKU.
SIMULAÇÃO DAS ETAPAS DE USINAGEM
Quando disponível, a ROKU hoje obtém conjuntos de dados 3D dos componentes a serem usinados de seus clientes, normalmente em um formato de dados neutro, como STEP ou IGES. Os usuários importam esses dados para o TopSolid, onde muitas vezes ainda precisam de algum pós-processamento. "O problema é que, basicamente, fabricamos e também programamos usando a tolerância média, mas nem todos os clientes projetam dessa forma. Isso significa que os dados convertidos precisam ser continuamente adaptados", diz Hammele. Se o cliente ainda não estiver projetando em 3D ou não puder fornecer dados STEP, os operadores deverão, em primeiro lugar, produzir um modelo de produto 3D usando os desenhos 2D. Em seguida, eles definem a geometria das peças brutas, que servem de base para o projeto dos dispositivos de fixação e dos equipamentos de produção. Os modelos 3D dos gabaritos de fixação podem ser usados diretamente para a simulação dos programas de usinagem.
Com base nas peças brutas e na geometria do componente, o material a ser removido pode ser determinado. O programador CAM determina como e com quais ferramentas ele deve ser removido, com o sistema oferecendo sugestões específicas sobre a estratégia de usinagem. Após cada etapa de usinagem, a geometria das peças brutas pode ser atualizada, de modo que o usuário possa ver rapidamente onde o material permanece. O software oferece a possibilidade de definir ciclos de usinagem reutilizáveis para elementos geométricos que ocorrem com frequência. Esses recursos de automação são, no entanto, de importância subsidiária para a ROKU, como ressalta o Sr. Hammele: "Para nós, o foco está claramente na otimização dos tempos de usinagem. Precisamos ver como podemos atingir os tempos de usinagem estimados e, por isso, nos concentramos mais na programação."
A otimização dos tempos de usinagem é um processo interativo. Usando a simulação de remoção de material, o usuário pode reconhecer quais operações de usinagem exigem mais tempo e pode fazer correções adequadas, por exemplo, escolhendo uma estratégia de usinagem diferente ou fazendo um pré-desbaste com uma ferramenta maior antes de usinar com uma menor. Na opinião do Sr. Hammele, as funções de simulação são alguns dos principais pontos fortes do TopSolid, pois permitem que você veja com bastante precisão quanto tempo duram as operações individuais e como elas podem ser distribuídas de forma ideal entre os vários eixos e fusos.
REDUÇÃO DOS TEMPOS DE USINAGEM
Como a simulação permite determinar de forma confiável o material restante e as possíveis colisões, os operadores da máquina podem se concentrar, ao executar os programas, nos aspectos que não podem ser simulados ou que são desproporcionalmente complexos para simular no computador (por exemplo, os efeitos das forças físicas ou os comportamentos de materiais específicos de alto desempenho). "O artesão que trabalha na máquina sempre será responsável por fazer a última diferença vital", diz o Sr. Kuhnhaus com convicção. "Mesmo com o mesmo material, as circunstâncias nunca são idênticas. Um meio de corte que funciona bem com uma peça pode, de repente, apresentar problemas em uma geometria de componente diferente. Portanto, a experiência do operador deve ser constantemente levada em conta no processo de usinagem."
Graças à melhor qualidade dos programas CNC, os tempos de execução na ROKU diminuíram significativamente. Há menos erros de máquina que podem gerar custos extras desnecessários. Também foi observado que os tempos de operação da máquina foram reduzidos por meio da otimização dos programas CNC, embora seja difícil quantificar com precisão a economia que isso proporciona. Esse é particularmente o caso, uma vez que a introdução do sistema ainda não foi totalmente concluída. "Presumo, no entanto", diz o chefe da empresa, Roland Kuhnhaus, "que no estágio final de atualização, quando todas as máquinas tiverem sido mapeadas e todos os pós-processadores adaptados, será possível reduzir os custos do programa em 50% mais X, sendo que X aumentará proporcionalmente à complexidade crescente do componente a ser usinado". A ROKU espera obter um potencial de economia adicional com a introdução do gerenciamento de dados de produtos, que promete uma administração mais eficiente dos muitos dispositivos e equipamentos de produção.
Precisa de mais informações
PERGUNTA SOBRE NOSSO
PRODUTOS OU SOLUÇÕES?
Encontre o ponto de vendas mais próximo Contate-nos Obter uma cotação