1 April 2014
Lean manufacturing and the digital chain hold no secrets for this company specialized in the design and manufacture of industrial closures. An organization configured around TopSolid.
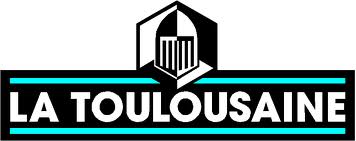
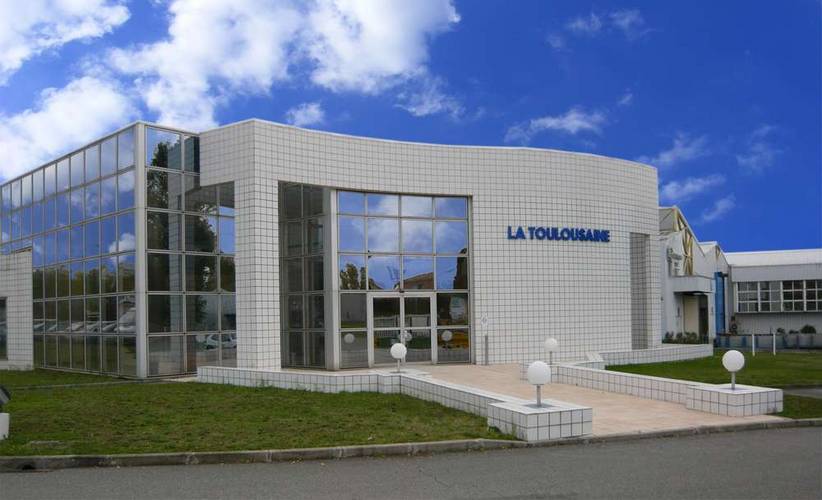
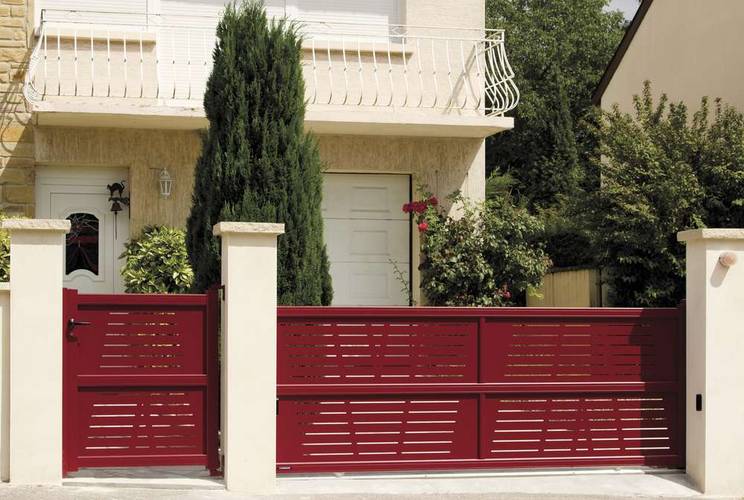
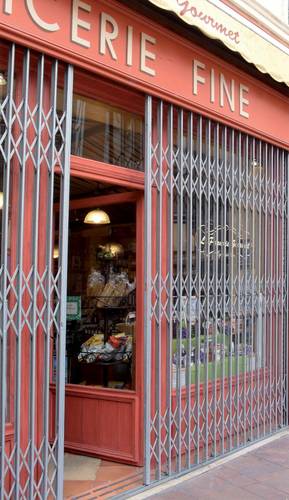
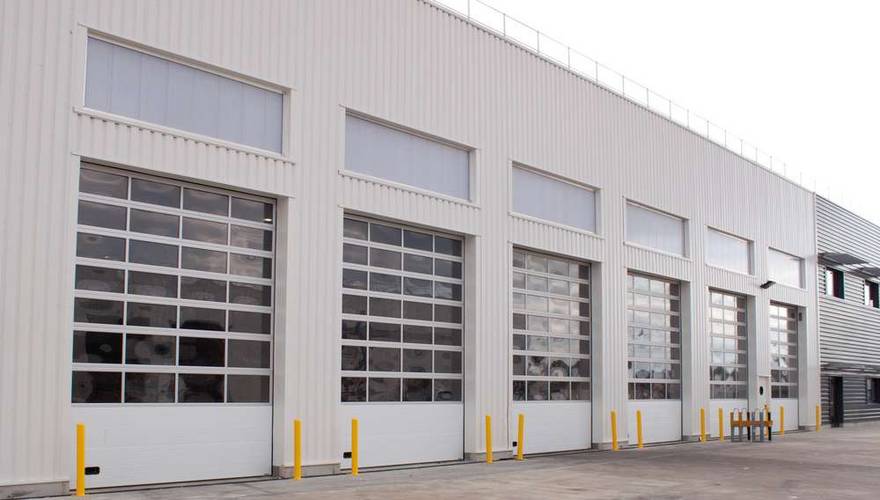
Based in Escalquens, near Toulouse, France, La Toulousaine manufactures some 60,000 products a year, from grids and shutters, to sectional doors and aluminum gates, for professional customers only. A headache, in terms of design and production. To solve the problem, this subsidiary of the Stella group, which employs 300 people and posts revenues of €55 million per year, drew inspiration from methods that have been tried and tested in the automotive industry. “All our products are made to measure, rapidly and according to a quality charter that makes no compromises”, explains Didier Simon. The company manager is a seasoned veteran of automotive manufacturing, who knows a thing or two about rapid production solutions capable of meeting two major targets: customer service and industrial efficiency.
A battery of tools, based on the TopSolid CAD/CAM software from Missler Software, was deployed to produce more, better and faster. “We chose TopSolid for its rich functionality, its configurability and its ease of use. Three advantages that still meet our needs”, explains the manager. The users of the TopSolid software also appreciate the fact that the Missler Software branch office is nearby and is always ready to intervene rapidly, whenever necessary. The CAD/CAM tool is interfaced with an integrated management software application in a genuine digital chain that starts in the order-taking office.
Personalized orders thanks to the CAD/CAM software
14 people take 1,200 phone calls every day and, using the home-made configuration engine, raise one quote every 30 seconds. “That means one thousand quotes every day”, points out Didier Simon. Quotes that are converted into firm orders and are entered every day in the company’s enterprise resource planner (ERP). The parts required to build a gate, a shutter or a sectional door are selected according to the dimensions and the customer’s requirements. The company currently has some 10 licenses for the CAD/CAM software, which it also uses to personalize each order by taking parts from the company’s electronic catalog, or by incorporating customer demands for a specific pattern. And the same goes for the materials. The company’s specialists have to choose between plastics, wood and aluminum, or even hybrids, and find the right motor for motor-driven products. “The fact that all of these operations are automated significantly shortens our production cycles and improves quality”, emphasizes Didier Simon. This organization allows the company to fulfill orders to very tight deadlines.
TopSolid allows products to be personalized, while maintaining the same standards of industrial precision in the manufacturing process. “With its powerful and realistic 3D viewing tools, the software is capable of displaying special cases”, explain Thibaut Estanove and Hervé Guillem, respectively technician and industrial draftsman in the company’s design office. “For example, we can view the position of objects, such as electrical cabinets, and avoid collisions”.
The automatic systems in the digital chain logically extend to the CAM (computer-assisted manufacturing) side of things too. Once the order has been configured, the ERP raises the work order. The machining programs corresponding to each of the parts to be machined are selected amongst the programs stored in the CAD/CAM system, and then sent to the machine’s numerical controller.
Quasi-autonomous manufacturing
The three lines, specialized by product type, work according to the rules of lean manufacturing, 5S and just-in-time. The products are assembled at the end of each line. “Each production run is organized as flow that is pulled by the delivery trucks”, explains Didier Simon. Human interventions are limited all along the production chain and every workstation is self-controlled. The boxes of accessories are prepared in a picking zone and then checked by weighing. The Quality department regularly checks the products from the three lines by taking samples. Automation is used pragmatically, and whenever it can achieve gains in productivity. Consequently, the company opted for machining centers fitted with automatic input-output systems that allow the machines to operate in a quasi self-contained manner. The machines are controlled by a single operator. “At night, the operator in charge of the paint system also keeps an eye on the machine loaders”, explains Didier Simon. A new machine of the same type, but fitted with a loader with a higher capacity, will be operational by the end of this year. The new machine will boost productivity, allowing the company to break into markets where prices are being driven down. A vision also reflected by the €3.5 million invested by the company in a brand new building that will house the future technical and logistics center. “This technical center will bring together in the same place all the vital departments, from the design office to production engineering, quality and purchasing, that are currently scattered around the company”, explains the manager. Another means of benefiting from even more of the CAD/CAM software’s functionality, and looking to the future with confidence.
Daha fazla bilgiye ihtiyacım var
ÜRÜNLERIMIZ VEYA ÇÖZÜMLERIMIZ HAKKINDA BIR SORUNUZ MU VAR?
Size en yakın satış noktasını bulunBize ulaşın Fiyat teklifi alın