20 August 2010
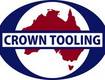
"I strongly recommend TopSolid because it runs the Macturn without fault, from simple milling and turning on one spindle to fully synchronized simultaneous machining with both spindles and all 9 axis together." Andrew King from Crown Tooling.
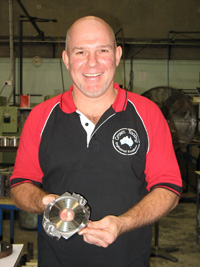
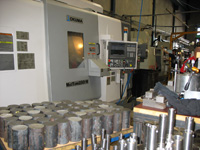
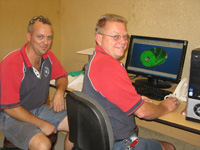
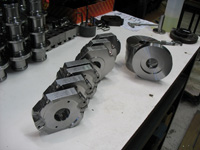
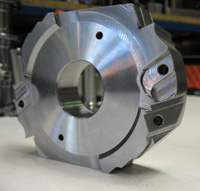
Company background
Crown Tooling was established in 1986. It was started by Andrew King as a Tool making and general Engineering business however right next door was a Saw Sharpening company. Although the company started as a traditional toolmaker it's probably no surprise that having a saw doctor right next door Crown soon began manufacturing tools for the Timber industry.
The local furniture manufacturers and joineries now had a locally based source of top quality tooling which meant that they could finally get Hydro serrated back knife heads and Hydro planer head tools manufactured quickly and to order instead of relying on the long lead times of overseas suppliers. Andrews's business grew and before long it was almost completely dedicated to the design and manufacture of wood related tooling.
The arrival of CNC machinery
Crown Tooling bought its first CNC machine in 1992 and saw the benefits of CNC immediately and today the company has 6 CNC machines with another on order. Until last year however the machine tools were the usual mix of milling and turning with one machining centre having an additional fourth axis; however it was clear to Andrew that in order to stay competitive and to grow the business he needed to reduce cycle times and improve productivity and quality. He needed to reduce or if possible completely eliminate the re-setting of components during manufacture and he found exactly what he needed in the Okuma Macturn 250.
This 9 axis machine from Okuma Australia has the capability of both turning and milling a component using up to 4 simultaneous axis. The machine has 2 turning spindles that can automatically transfer a part from one spindle to the other under program control so that both ends of the part can be completely finish machined in one setup. It was clear that the Macturn 250 was exactly what the company needed but Andrew also knew that in order to get the full benefit of a machine of that complexity you had to have a CAD/CAM system capable of programming it efficiently.
Important time gains thanks to TopSolid
Crown design all their tools in-house and so it also made good sense to the company to look for a completely integrated CAD/CAM system which allowed the manufacturing department to use the same 3D software as the design office. Whilst evaluating the various CAD/CAM products on the market Crown was disappointed to find that this is certainly not the norm, in fact a lot of the vendors he spoke to tried very hard to convince him that their “mix & match” products from independent developers was his only choice. Then he got a call from Steve Thomas from Cim Solutions who suggested that he take a look at TopSolid from Missler Software.
TopSolid fitted the bill perfectly as it's a totally integrated product, offers a full featured 3D parametric design modeler that can handle even the most complex parts and assemblies and then machine them using the most up to date machine tools, including the Macturn all in the one software package. Andrew intended to get the most he could from his machine including multi spindle work, simultaneous cutting with both turrets and multi axis milling and it was TopSolid's ability to utilize all of the MacTurn's features that really convinced Andrew that he had found the right software.
The combined investment of the machine and the software was put to the test with the very first job, a Floorboard cutter which previously needed 6 separate machining operations each with its own set up time on 2 different machines. This particular cutter has a multitude of complex angled faces for seating and clamping cutting inserts in it and is very difficult to machine correctly, so as a first job for the new TopSolid operators it presented a real challenge.
Andrew King says “We relied heavily on Cim Solutions for support during this first project as it has a total of 22 machinable features all at different angles but they worked closely with us and answered every question in great detail, especially when it came to the machining. At the same time we asked Okuma Australia's applications engineer Greg Williams to advise on any post processor changes needed to ensure that that the software produced CNC code was fully compatible with the machines as imported into Australia.”
As a result the cutter is now completed in one operation on one machine in only 1.5hrs, Andrew is very happy with the results as the cycle time is greatly reduced and the part is far more accurate than the previous components. Since then he and his team have modeled and programmed a large proportion of Crown's extensive range of cutters and thanks to TopSolid's powerful design capabilities they are already planning some new and innovative additions to the range.
Andrew summarized by saying “Investing in new technology is not simply a matter of buying the latest machines; you have to realize that to get the most from these machines you need the right software as well. I strongly recommend TopSolid because it runs the Macturn without fault, from simple milling and turning on one spindle to fully synchronized simultaneous machining with both spindles and all 9 axis together. Coupled with TopSolid's complete on screen machine simulation you know exactly what you are going to get on the machine even before cutting any metal, making it a highly efficient system.
There is a lot of talk by Cad/Cam companies about their respective abilities in this area but I know for a fact that TopSolid delivers what it claims.”
Daha fazla bilgiye ihtiyacım var
ÜRÜNLERIMIZ VEYA ÇÖZÜMLERIMIZ HAKKINDA BIR SORUNUZ MU VAR?
Size en yakın satış noktasını bulunBize ulaşın Fiyat teklifi alın