20 February 2017

TopSolid'CAM helps achieve hundredths-of-a-millimeter precision
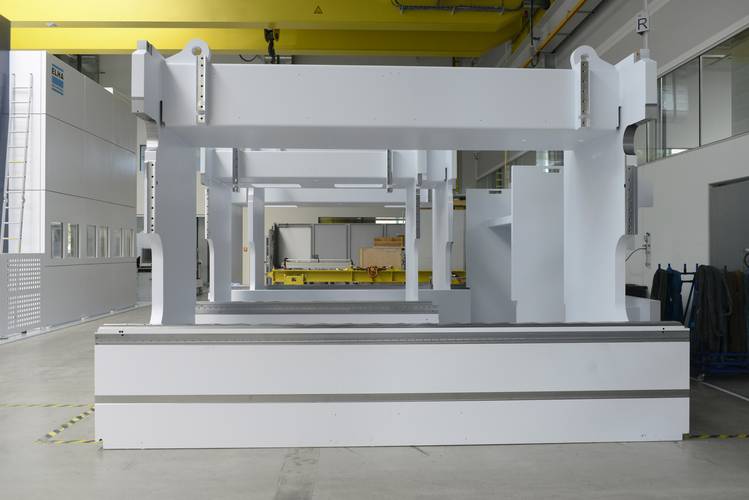
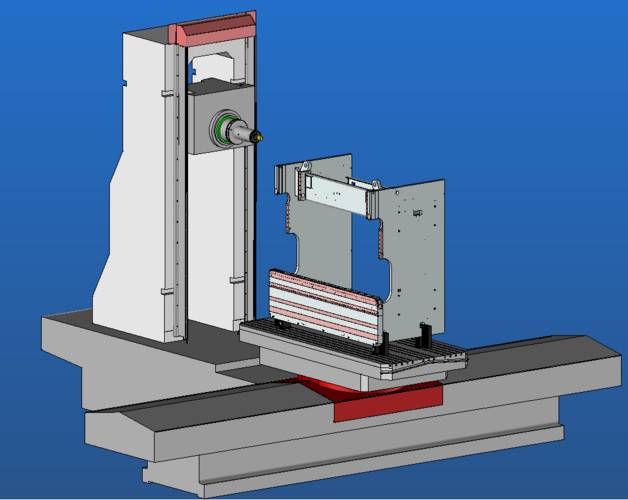
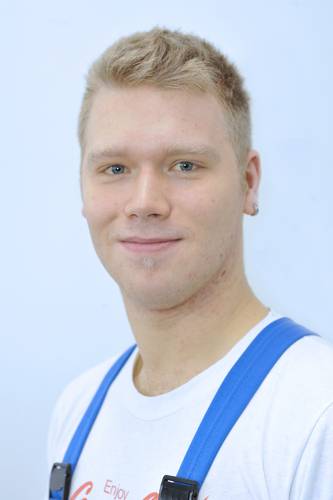
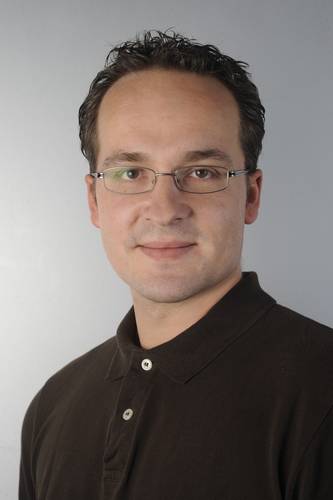
"Framework conditions"
The Austrian subsidiary of the TRUMPF Group plays a leading role in the corporation, with TRUMPF Maschinen Austria serving as a skills center for bending technology. The new ELHA 6-axis horizontal large machining center is used to produce the frames and pressure bars for the bending machines for shipment. These parts can be up to four-and-a-half meters in length, requiring observance of manufacturing tolerances to within hundredths of a millimeter. TECHSOFT provided support in setting up the software framework conditions for this demanding manufacturing process.
In early 2015, the machine pool of TRUMPF Maschinen Austria GmbH & Co KG in Pasching, near Linz, received reinforcement. An ELHA SMX 5239 machining center was introduced for the manufacturing of the frames, which can measure up to 3 m high and 4.5 m long, for the TruBend bending machines. This type of machining center is designed for manufacturing frame components for machine tools. The basic structure consists of a massive, moving column (W-axis) for secondary positioning, with a dynamic 2-axis unit (Y-/Z axis) for the main machining movements. "We produce 48 different models on this machining center, on a just-in-time basis. This means that the cycle times must be short, but the precision very high. Even for four-and-a-half meter long frames we onluy allow two hundredths of a millimeter tolerance" says Manuel Mayrhofer emphatically, the man in charge of mechanical manufacturing and painting at TRUMPF Maschinen Austria. "The core aspect of the machine, the Z-axis, accelerates at 6m per second squared, and can be swiveled simultaneously," adds the TRUMPF employee, referring to a particular specialty of the ELHA SMX 5239, the commissioning of which was once more supported by TECHSOFT, a company specializing among other things in CAD/CAM solutions. "We have known the people we deal with at TECHSOFT very well for many years. We've a history of getting things up and running in intensive collaboration, such as simulation programs for example, whereby it is possible to simulate not only in 3D but also in 5D", Mr Mayrhofer goes on to say. For the ELHA project, however, TECHSOFT had a particular hurdle to clear: the programming had already been done, with virtual reproduction in TopSolid'CAM, even before the machining center to be simulated had actually taken form. "The first collision checks were already underway before the ELHA SMX itself had even arrived in Pasching" recalls Daniel Plos, Sales Manager for production solutions at TECHSOFT. Consequently, during the entire project phase there were permanently adaptations, readjustments and modifications to be made. "This sometimes placed considerable demands on us" Daniel Plos acknowledges. The biggest challenge, according to Daniel Lovrenovic, TECHSOFT project manager/technician, was simulating the changing of the head unit or the tool head. "At TRUMPF, up to three angle heads / units can be used during a machining process, of varying dimensions and with sometimes starkly differing geometries and alignment possibilitiesµ. And these machine change capacities had to be reproduced in the simulation. Fortunately, TopSolid provides the option of taking into account several units and/or heads in one document" Mr Lovrenic explains.
TopSolid helps save time
The ELHA 6-axis horizontal large machining center is now up and running in three-shift operation at TRUMPF. While one part is being machined, two further (mainly) welded assemblies are being equipped concurrently. In all, 360 different tools are used in producing the desired machine frames and pressure bars. Depending on the complexity and size of individual parts, the manufacturing time can vary from between one and seven hours. Thanks to TopSolid'CAM, the running-in times involved in this can be reduced by up to 50%. "TopSolid'CAM is for us an extremely helpful software tool, with which we work on a daily basis. " says Manuel Mayrhofer in praise of the solution, and his namesake and work colleague, Andreas Mayrhofer, one of the most active TopSolid'CAM users at TRUMPF in Pasching, chips in to say: "Thanks to software support, I only need a maximum of 3 to 4 days for the programming of our components, including simulation. If I had to do all this manually, or copy it from other programs, it would be sure to take twice as long, if not longer"
Andreas Mayrhofer is the TRUMPF employee who, from 2013 to 2015, worked particularly intensively in cooperation with TECHSOFT, together to create, as he calls it: "a sensible CAM system including simulation and post-processor." What was particularly important for him in this regard was the most user-friendly design possible for the post-processor:"Because as the interface between CAM program and CNC format, say as translator of geometrical information into G-Codes, this is of the utmost importance in the product engineering process."
Machining duplication as a favourite feature
Today, Andreas Mayrhofer is a "TopSolid'CAM pro". He now knows which options he can all upon in "his" CAD/CAM programming system, and where these are to be found. Three years ago this is not the case. Back then, the TRUMPF employee was getting his first taste of TopSolid on a basic training course over several days at TECHSOFT, with successful results. "For me personally, learning to use this software was relatively easy. In the course apprenticeship I'd already had programming experience on Heidenhain and Siemens CNC controls, and I'm generally someone who gets to grips quite quickly with new systems" says Andreas Mayrhofer of himself.
In the TopSolid'CAM basic training proposed by TECHSOFT, he found out how to set up and mill components, while paying attention when determining the machining cycles to how the simulation and the collision testing work, along with many other things. What he says he found most enjoyable at the time was the short introduction to 3D milling, although this is a functionality that is rarely if ever required in his position at TRUMPF. Instead, what turned out over the course of time to be his absolutely favorite feature in TopSolid'CAM is machining duplication. "With this functionality, I can transfer already existing milling programs from the WALDRICH COBURG machine, in just a few mouse clicks, to the ELHA machining center. These can be adopted 1:1 with the adjustments, the tool and the approach strategy. This saves me from having to rewrite a complete new cycle" says a delighted Andreas Mayrhofer in reference to a function in TopSolid'CAM that is particularly labor-saving for him personally.
User-friendly automation
Worldwide, there are now more than 10,000 customers who place their trust in the TopSolid product family from Missler Software. One of the reasons for this is that this fully-integrated CAD/CAM solution for the machining industry offers comprehensive functions for the cost-effective programming of complex processing machines, since so much is fully automated with this software. In conjunction with the topological component recognition, TopSolid(CAM can for example calculate differences / concordances between two componentns. The tool paths are then adapted to the new tool. In combination with intelligent blanks management, this signifies practically automatic programming.
Any programming errors are also automatically recognized, moreover. For example, the software will immediately issue a warning loud and clear, if an attempt is made to machine different thread depths in one cycle. "If several M6 threads are 10mm deep, but one is out of sequence with a depth of 10.25 mm, I'm immediately notified of this topology difference if I should try execute all bores in a single cycle" says Andreas Mayrhofer, speaking from experience. What he also uses pretty frequently as a TopSolid'CAM user is the generation of "milling methods", when certain machining step combinations need to be transferred to components of different sizes. "With this I can prepare templates for various components and, for example, combine roughing and finishing tool in a single method" he explains. Last but not least, the TRUMPF employee is highly impressed by the simulation possibilities in TopSolid'CAM, even though at TRUMPF they have specific software for this (VERICUT) "When doing CNC programming, I must first of all position the Z-axis correctly, in order to be able to mill a component at all. In such situations, I then always switch for a short time into simulation mode, in order to check that the chosen orientation really works," declares Andreas Mayrhofer. This is how he sums up his appreciation of TopSolid'CAM: "It's a super system and, in combination with VERICUT, it's absolutely indispensable to us." The TRUMPF employee has similar words of praise for TECHSOFT: " The support team was always really quick to come up with answer" he effuses, and the head of mechanical production at TRUMPF, Manuel Mayrhofer, declares for his part: "From our experience, this is the crucial factor when it comes to the trickier projects: knowing the people involves and being able to rely on one another. With TECHSOFT, this is definitely the case. The Linz-based company supported us comprehensively and competently in the drafting of the technical brief, the adaptation of the post processor, the commissioning of the ELHA machining center, and lots more still."
Daha fazla bilgiye ihtiyacım var
ÜRÜNLERIMIZ VEYA ÇÖZÜMLERIMIZ HAKKINDA BIR SORUNUZ MU VAR?
Size en yakın satış noktasını bulunBize ulaşın Fiyat teklifi alın