27 September 2019
Der Stoff aus dem die Zukunft ist „Dank TopSolid‘Cam können wir die wachsende Komplexität und Funktionsvielfalt der heutigen Fertigungsmaschinen virtuell darstellen und erhalten gut durchdachte, einwandfreie Postprozessoren für störungsfreie Programmabläufe auf unseren Werkzeugmaschinen.“ Karl-Heinz Kragl, Fertigungsleiter, Lindauer Dornier GmbH

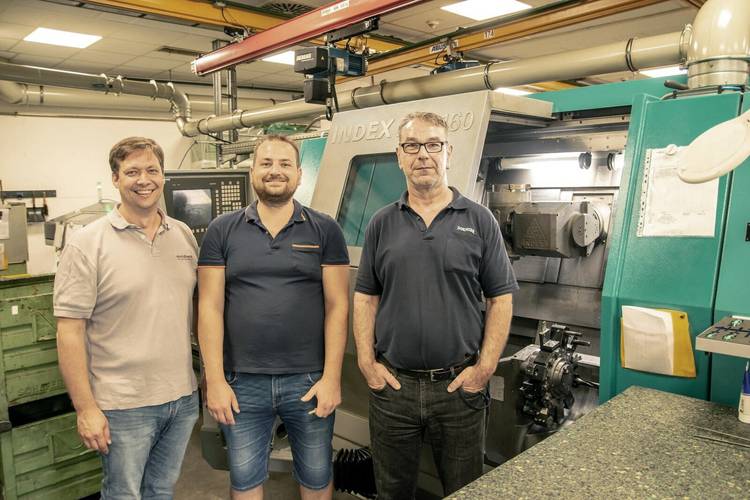
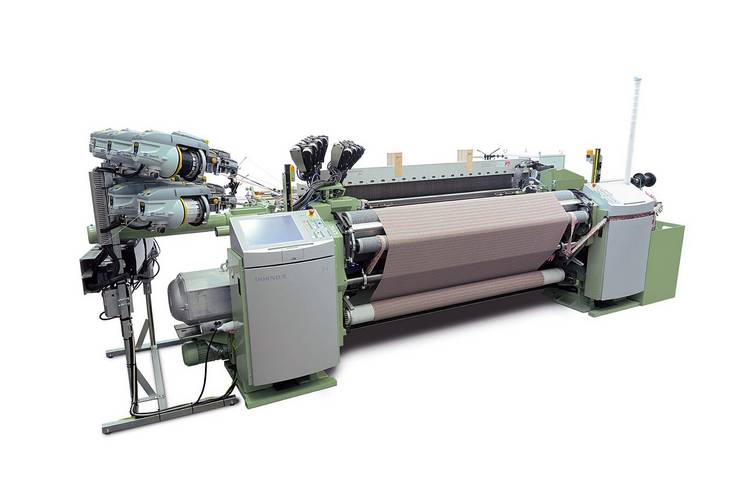
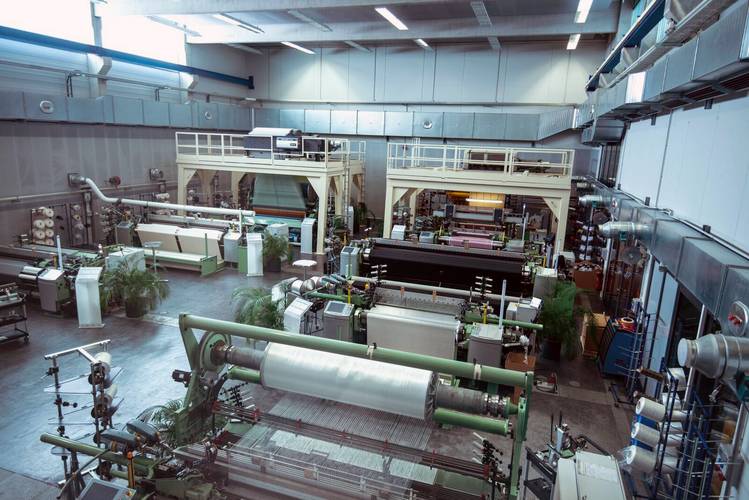
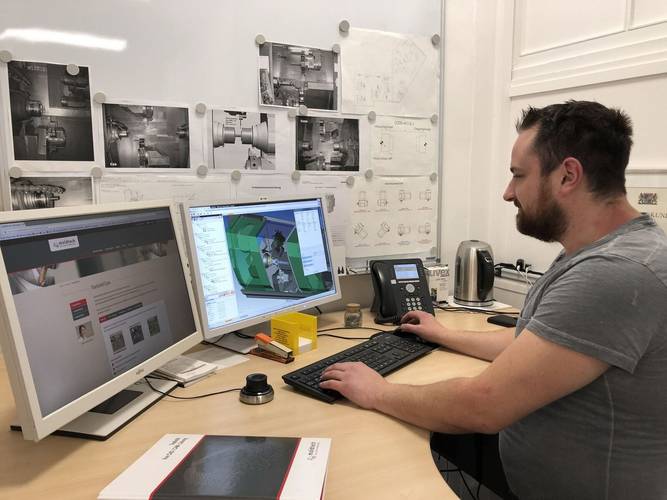
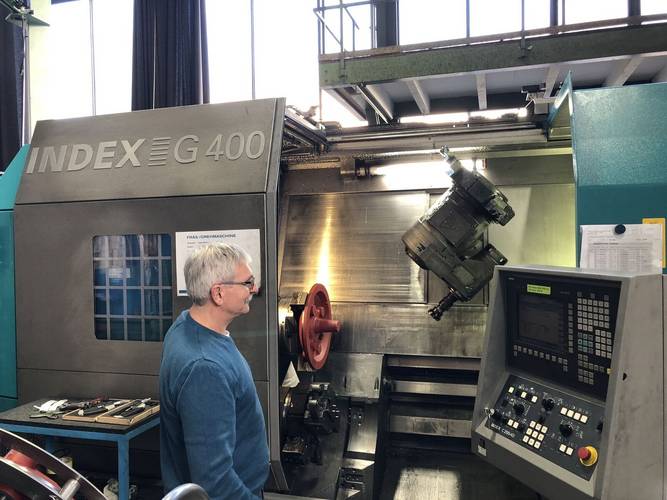
Den Namen Dornier verbindet man bis heute mit Erfindergeist und Zuverlässigkeit. Eine solch stete Erfolgsgeschichte lässt sich allerdings nur mit einer hohen
Anpassungsfähigkeit und dem Mut zu Veränderungen realisieren. Mit Moldtech als
Partner und unterstützt durch dessen leistungsstarke 3D-Software-Lösung
TopSolid’Cam erschloss sich der Webmaschinenhersteller vom Bodensee neue Geschäftsfelder, die ihn weiterhin erfolgreich zukunftsfähig machen sollen.
Unternehmen | Die Lindauer DORNIER GmbH zählt weltweit zu den Technologieführern im Bau von Hochleistungswebmaschinen, Textilausrüstungsmaschinen und Folienreckanlagen. Die Fertigung sämtlicher Maschinen und Anlagen erfolgt in den deutschen Produktionsstätten. |
Projekt | Begleitung des Einstiegs in die Dreh-Fräs-Technologie durch optimale Programmierbarkeit der neu erworbenen CNC- Maschinen |
Software | TopSolid‘Cam |
Leistungen | Einführungsbegleitung, Postprozessor-Programmierung, Anwenderschulung, Integrationsunterstützung |
Nutzen | Volle Nutzung der Maschinenmöglichkeiten, Optimierung der Arbeitsprozesse und damit höhere Produktivität und flexible Produktion |
1950 wurde die Lindauer DORNIER GmbH am heutigen Stammsitz in LindauRickenbach gegründet. Der bis dato weltweit renommierte Flugzeughersteller
Dornier begann nach Ende des Krieges notgedrungen mit dem Bau von Webmaschinen, weil der Flugzeugbau in Deutschland von den Alliierten verboten worden war. Heute entwickelt und produziert der einzige deutsche Hersteller von Textilwebmaschinen außerdem Folienreckanlagen für dünnste Kunststofffolien u.a.
für Halbleiter, Kondensatoren für Hybridfahrzeuge und Foliendisplays von Mobiltelefonen sowie für höchst anspruchsvolle Gewebe wie Airbags und
Aramidgewebe für feuerfeste oder schusssichere Anwendungen. In den zwei
Werken Lindau und Esseratsweiler werden die Maschinen mit ca. 1.000 Mitarbeitern hergestellt und zu 90 % exportiert. Mit Tochtergesellschaften in den USA, China, Indien und der Türkei ist die „LiDO“ auch international vertreten.
Vielseitig zuverlässig
Mit dem Kauf mehrerer INDEX Dreh-Fräszentren wurde ein 3D-CAM-System erforderlich, um den neu geschaffenen Geschäftsbereich schnell und möglichst unkompliziert produktiv zu machen und optimal an den bestehenden
Maschinenpark anzubinden. Das Systemhaus Moldtech erwies sich als kompetenter
Partner, der mit TopSolid’Cam ein leistungsstarkes Programmiersystem für die Implementierung, Schulung und den laufenden Support vorweisen konnte.
TopSolid‘Cam überzeugt durch
- Volle Kollisionskontrolle auch bei komplexen Spannsituationen
- Einfaches Setzen von Synchronisationsmarken
- Fremddatenimport und Skalierung auf Toleranzmitte
- Schnelle und sichere NC-Satzausgabe
- Rohteilmanagement in Echtzeit
- Einfache Bedienbarkeit
Weben macht viele Dinge möglich
Das Weben gehört, nach Holz- und Steinbearbeitung, zu den ältesten Handwerken der Menschheit und gilt bereits seit 32.000 Jahren als nachgewiesen. So hat man etwa in Grabkammern des ägyptischen Altertums Gewebereste von Gewändern gefunden. Heutzutage wird natürlich nicht mehr auf klappernden Webstühlen aus Holz das Schiffchen hin- und hergeschickt. Auf hoch technologisierten
Webmaschinen werden Wolle, Seide und Leinen zu hochwertigen Stoffen für Kleidung, Möbel und Gardinen verwoben. Und noch mehr: „Gewebte Materialien stecken in mehr Produkten, als man denkt“, sagt Karl-Heinz Kragl, Teamleiter NCProgrammierung bei der Lindauer DORNIER GmbH. Etwa in Airbags oder in Reifen – in den Millionen von Autos, die täglich über unsere Straßen rollen und auch bei Flugzeugen, dient sogenannter Reifencord zur Verstärkung des Gummiprofils. Die Luftkissen aus extrem dichtem Stoff, die sich bei einem Unfall in Sekundenschnelle aufblasen, werden ebenfalls gewoben, überwiegend auf Maschinen der Lindauer DORNIER GmbH.
Diese sogenannten technischen Textilien machen inzwischen über die Hälfte des Umsatzes aus. Dabei verbinden viele den Namen DORNIER bis heute erst einmal mit der Entwicklung und dem Bau von Flugzeugen. Das war bis zum Ende des Zweiten Weltkrieges auch der Fall. Das Werk bei Lindau diente als Zulieferbetrieb, in dem unter anderem Leitwerkteile gefertigt wurden. Nach dem Krieg allerdings verboten die alliierten Besatzungsmächte den Flugzeugbau und so musste sich DORNIER nach einem neuen Geschäftsfeld umsehen. Ein Textilwerk in der Nähe hatte Bedarf an Webstühlen und Ersatzteilen, nachdem die Webereien während des Krieges brachlagen. Die hohe Nachfrage gab den Anstoß. Mit Innovationen verschaffte sich DORNIER wie früher im Flugzeugbau, auch auf diesem Gebiet aus dem Stand heraus Weltgeltung.
Produziert wurden zunächst Schützenwebmaschinen – die kein Webschiffchen, sondern den sogenannten „Schützen“ hin und her schießen – und Trocknungsanlagen für die Pappe-, Papier- und Baustoffplattenindustrie. 1967 brachte dann die Einführung der Greiferwebmaschine die Basis für den Aufstieg und inzwischen hat sich Lindauer DORNIER als größter deutscher und gleichzeitig international renommierter Webmaschinenhersteller etabliert.
Der Stoff aus dem die Zukunft ist
Mit der 2015 gegründeten Sparte „Composite Systems“ konzentriert sich die Firma neuerdings auf die Entwicklung von speziellen Anlagen zur Herstellung von Faserverbundkunststoffen. Hier sieht das Unternehmen einen großen
Zukunftsmarkt. Die 3D-Webmaschinen verbinden verschiedene Materialien auf Basis von Carbon- und Glasfasern miteinander, die äußerst vielfältig einsetzbar sind, zum Beispiel in Turbinenschaufeln für Düsenflieger.
Für das neue Geschäftsfeld wurde eigens eine neue Halle in Betrieb genommen.
Von der Planung über die Komponentenfertigung bis hin zur Montage werden die Textilwebmaschinen seit jeher komplett im Hause LiDO gebaut und das soll auch bei den hochmodernen Kunststoffindustriemaschinen so bleiben.
Damit die renommierten Webmaschinen reibungslos funktionieren, wird schon bei der Produktion der einzelnen Maschinenteile auf Qualität geachtet. Dazu stehen modernste Dreh-/Fräszentren in der neuen Produktionshalle. Sie sind flexibel einsetzbar und erlauben es, die verschiedensten Werkstücke quasi vom Reißbrett her komplett zu bearbeiten.
Die geometrisch anspruchsvollen und hochgenauen Werkstücke müssen noch dazu eine hohe Oberflächengüte besitzen. Wenig Platz, viele Achsen und noch mehr Störkonturen im Maschinenraum der INDEX-Maschinen setzen also nicht nur das jahrzehntealte Know-How der Mitarbeiter voraus, sondern es braucht darüber hinaus ein modernes CAM-System, das dem Anwender das Programmieren in einer virtuellen Maschine ermöglicht. „Uns war von Anfang an klar, dass man so komplexe Bearbeitungen nur mit einem 3D-Modell programmieren kann“, erinnert sich Kragl.
Überzeugend simuliert
Nicht zuletzt gab also die hervorragende Maschinensimulation in TopSolid’Cam den Ausschlag dafür, dass das Systemhaus Moldtech den Zuschlag bekam, den neuen
Maschinenpark anzubinden. Moldtech erzeugte dazu in TopSolid’Cam zunächst die
3D-Modelle der INDEX-Maschinenmodelle inklusive der damit einhergehenden Kinematik. In TopSolid’Cam programmiert der Anwender sein Werkstück also bereits in der virtuellen Aufspannsituation und kann alle Komponenten am PC optimal aufeinander abstimmen. Das beinhaltet auch die Abbildung der zur Verfügung stehenden Werkzeuge. Die systemeigene Werkzeugbibliothek kann – und sollte – der Anwender um seine realen Werkzeuge samt Schnittwerten erweitern und verwalten. TopSolid’Cam errechnet dann anhand der hinterlegten Schnittwerte, Vorschübe und Zeitwerte für die Werkzeugwechsel die Dauer der Prozesse und stellt die Prozessfolge auch grafisch dar. Kollisionen können frühzeitig behoben und optimale Werkzeugwege erstellt werden, auch dank des automatischen Rohteilmanagements in TopSolid‘Cam. Sämtliche Maschinenwege werden im ständigen Abgleich zwischen zwei geometrischen Modellen generiert, dem Rohteil und dem Fertigteil. Dabei wird das Rohteil nach jeder Bearbeitung aktualisiert, so dass jeweils auf der aktuellen Geometrie weitergearbeitet wird. „Wenn wir weiterhin so gut zusammenarbeiten, schaffen wir unser Ziel, die Störungsfreiheit unserer NC-Programme auf nahezu 100 Prozent anzuheben“, erklärt Kragl. Lediglich beim Import von 3D-Modellen aus der Konstruktion sind bei LiDO kleinere Anpassungen nötig, die allerdings über die integrierte
Modellierfunktion für importierte CAD-Daten schnell umzusetzen sind. Dank der Flächenfunktion in TopSolid’Cam lassen sich die Daten bequem importieren, nach Belieben fertigungsgerecht verändern und sogar auf Toleranzmitte skalieren.
Mit zuverlässigen Postprozessoren alle Fäden in der Hand
Nach der Simulation und gegebenenfalls Optimierung der Programme erfolgt der Postprozessorlauf. TopSolid’Cam verfügt bereits in der Standardausführung über ausgezeichnete Postprozessoren, die in enger Zusammenarbeit mit den Maschinenherstellern entwickelt werden. Sämtliche Multitaskingmaschinen in der neuen Fertigungshalle hat Moldtech inzwischen über leistungsfähige
Postprozessoren an TopSolid‘Cam angebunden. Diese werden aus der CAMAnwendung mit einem NC-Code versorgt. „Geht nicht, gibt’s bei Moldtech nicht“, erklärt Kragl: „Alle Postprozessoren waren schon nach kurzer Zeit soweit lauffähig, dass wir damit programmieren konnten. Wenn eine Bearbeitung mal nicht zufriedenstellend unterstützt wird, bekommen wir binnen eines Tages einen aktualisierten Postprozessor“. Das stimmt das Lindauer Unternehmen auch zuversichtlich für das neueste Projekt, das mit Moldtech und TopSolid‘Cam realisiert werden soll: ein Postprozessor für einen Langdreher mit 3 Kanälen und 10 Achsen.
Ein starkes Team
Begleitend zur Implementation erstellte Moldtech für LiDO ein stufenweise aufgebautes Schulungskonzept, dass an die Bedürfnisse des Webmaschinenherstellers angepasst wurde. Die Mitarbeiter lernten dabei nicht nur die Grundlagen im Umgang mit TopSolid’Cam kennen, sondern erhielten auch Sonderlehrgänge zu den Themen CAD, CAM und Dreh- und Fräswerkzeuge. Und wenn doch mal ein LiDO-Mitarbeiter in der Arbeitsvorbereitung feststeckt, ist der Softwarepartner via E-Mail, Telefon und Fernwartung zu erreichen. Auch in Sachen Betreuung hat LiDO also den richtigen Partner gefunden. Durch die Anpassung an den technologischen Fortschritt und die immer höher werdenden Ansprüche an die Fertigung von Bauteilen wird sich der Maschinenpark einer jeden Firma mit der Zeit ändern müssen. Aber das schreckt ein innovationsfähiges Unternehmen wie die Lindauer DORNIER GmbH gar nicht. „Dank des Umstiegs auf das innovative TopSolid‘Cam 7 sind wir zuversichtlich, auch die künftigen Anforderungen stemmen zu können, die auf uns zukommen“, so Kragl.
Benötigen Sie weitere Informationen
EINE FRAGE ZU UNSEREN PRODUKTEN ODER LÖSUNGEN?
Finden Sie die nächstgelegene VerkaufsstelleKontaktieren Sie unsAngebot einholen