2 September 2010

Close-hauled with TopSolid.
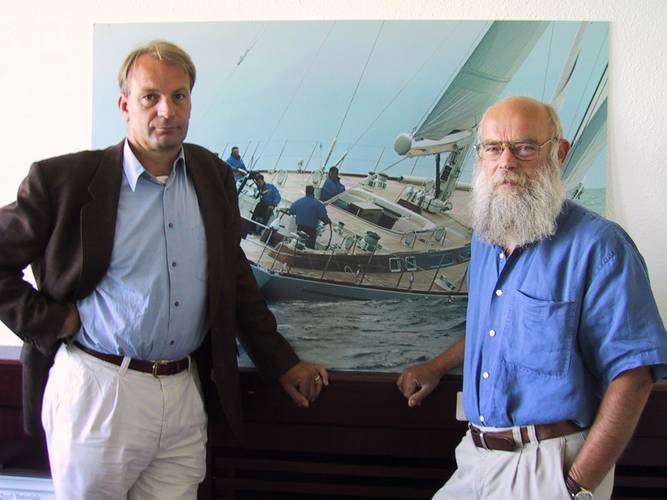
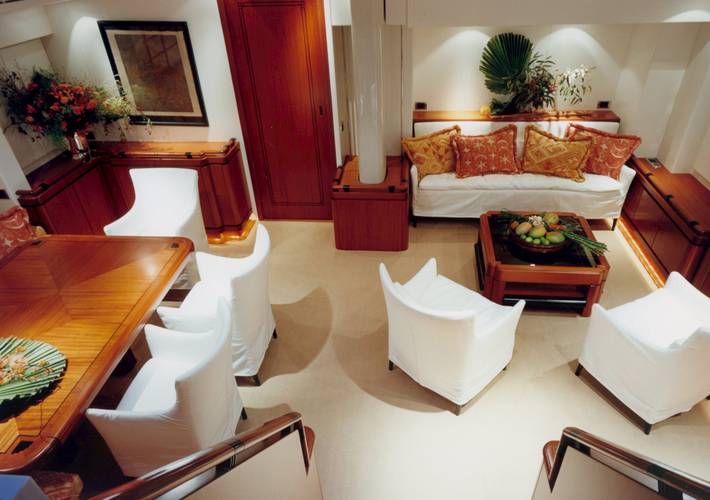
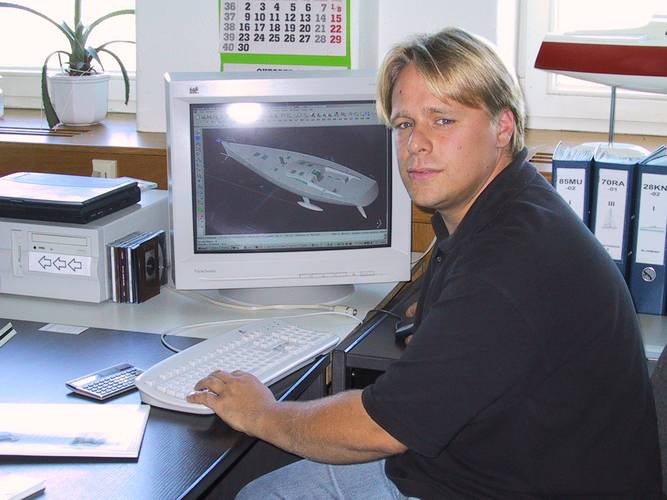
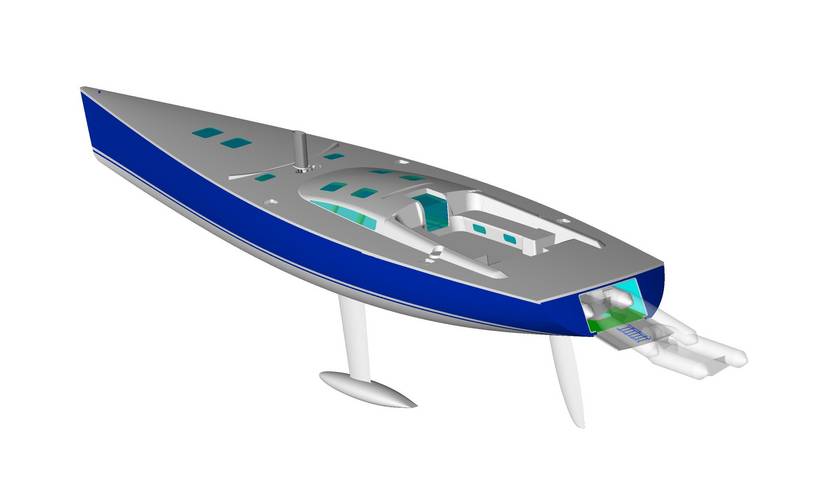
Just imagine the designers of Michael Schumacher’s racing car would start to develop cars for mass-production. Impossible you think? Not so in sailing. Judel/vrolijk & co is among the world leaders in designing racing yachts for international competitions such as America’s Cup, Admirals’s Cup, Copa del Rey, Whitbread Race Around The World, Daimler Chrysler North Atlantic Challenge or Sardinia’s Cup. The engineering company is headquartered in Bremerhaven, Germany, and is also very successful in designing cruising and serial yachts. In order to achieve comfort in little space collision-free, all boats are designed in 3D with Missler’s TopSolid software.
Judel/vrolijk & co engineering gmbh plans and designs sailing and motor yachts and also implements small commercial shipbuilding projects on an international plane. The company was founded in 1978 by Friedrich Judel and Rolf Vrolijk. In 1986, Torsten Conradi became third partner. Their first serial yacht called Popcorn opened up the doors to the racing scene in which they are well established today. Their designs have been successful in numerous international regattas such as the Admiral's Cup, the unofficial team world championships in offshore sailing which their yachts won three times.
Thanks to its many victories, judel/vrolijk & co is among the few yacht designers of today that work for the crème de la crème of sailing. The Bremerhaven-based company was involved in the development of the German America’s Cupper for the Illbruck team and is also designing the new racing yacht for the Spanish king Juan Carlos. However, racing is not the only business of the company and is not top selling anymore. Over the past years, judel/vrolijk & co has become one of the leading companies in cruising yacht design.
Individual customer requirements
Eight employees at judel/vrolijk & co design racing yachts and cruiser-racers as well as cruising yachts for individual customers and serial yachts for renowned shipyards such as Baltic Yachts (Finland), Najad Varvet (Sweden), Dehler Yachtbau or Yachtzentrum Greifswald. The portfolio of boats includes heavy displacement yachts made of steel as well as ultra-light sandwich designs made of carbon fiber reinforced plastic. The company also increasingly designs luxurious motor yachts.
Over the years, judel/vrolijk & co has produced more than 350 yacht designs. On average, the company works on ten projects per year. Depending on their scope, however, individual projects can take up to two years to completion. The company is committed to fulfil individual customer demands in a consequent way. If required by the customer, the designers will accompany a project from the conceptual design and bidding process up to the christening of the ship. Currently, judel/vrolijk & co is designing two 45 meter yachts by customer order for a Finnish shipyard.
Customer demands vary depending on the type of boat, e.g. racing or cruising yachts. For regatta boats, great importance is attached to the design of shape and hull while luxurious cruising yachts require more interior work. “Sailing yachts have their own power and water supply, air conditioning and ventilation, and sanitary system,” Torsten Conradi explains. “In a way, yacht designers are architects, domestic technicians and stress analysts at the same time, and sometimes they even take on the tasks of interior designers.“
On collision course in 2D
Since the customers want to fit a lot of equipment into cruising yachts, the boats are becoming bigger and increasingly compact. For this reason, there were overlaps in 2D designs which could not be identified until the boat reached the shipyard and caused unnecessary redesign. “In three out of four cases, the parts drawn did not fit or collided with each other,“ Conradi explains. He had wanted to implement a 3D CAD system long before. The German America`s Cupper was to be developed in 3D and thus gave reason to install the first TopSolid workstation.
Most interestingly, Missler’s integrated CAD/CAM solution was not at all taken into account when choosing the system, but appeared on the scene by a mere coincidence. Missler’s Bochum-based sales partner ISK CAD/CAM-Systeme introduced the software at Bremerhaven, and the ship designers were almost instantly convinced of its qualities. “We immediately thought that TopSolid was exactly what we were looking for,“ Conradi recalls. “Supported by ISK, we customized the software to meet special requirements in yacht design. We are very positive about this program and are considering to introduce TopSolid throughout the office.“
At present, judel/vrolijk & co has three TopSolid workstations on a Windows 2000 platform. All computers are PCs with a main memory of 600MB, 30GB of disk space and a powerful graphics card. They are connected via a data server to enable all users to access project information at any time. In addition to the basic TopSolid package, the system configuration comprises the sheet metal module, which is used for unfolding acrylic glass window panes, and the kinematics module for performing collision checks on moving parts.
TopSolid is quick and easy to learn and also very intuitive. After only two days of training, all users were able to design models. It took a little longer, however, to become familiar with the parametric design approach. “If you want to use TopSolid efficiently, you need to follow a highly structured approach from the very beginning in order to simplify the process,“ Conradi explains. According to Tim Ulrich, who is one of the users of TopSolid, the boat designers have developed a standardized method for certain areas such as deck superstructures. Thus, they can reuse existing parametric models in other projects.
Retrieval of hull surfaces
The new 3D system perfectly integrates into the existing system environment and workflows. Next to TopSolid, judel/vrolijk & co also uses the Euclid Styler surface modeler, the 2D CAD system AutoCAD as well as MultiSurf for hull design. “Hull design requires special tools since the geometric shape needs to be calculated and optimized with respect to hydrostatic issues in order to achieve a certain position of the center of gravity and displacement distribution,“ Conradi explains. “Therefore, one of our requirements was a perfect transition from the hull generation in TopSolid.“
The hull shape depends on the type of boat, e.g. heavy and comfortable cruising yachts or light racing yachts. The center of gravity and the displacement required are identified by weight calculation. The displacement itself determines the rough shape of the boat’s body surface and is then optimized in an iterative process with respect to hydrostatic properties. “You have to check over and over again if the weights match the defined body of the boat until you finally have an optimized shell,“ Ulrich illustrates. The resulting shell can be imported into TopSolid via an IGES interface with a high degree of accuracy.
Within the 3D CAD system the imported hull surfaces are supplemented around the deck and then transformed into a solid, which is subsequently hollowed. Afterwards, the yacht designer generates the transom by cutting off the stern, chamfers the boat body at the stem in the front and then places the cockpit on the deck. “TopSolid’s functions for importing free-form surfaces and the combination of surface models and solids are very powerful,“ Ulrich states. “However, there are limitations to processing free-form surfaces. We need to be able to control these surfaces very precisely since the location of a single point can be crucial for a boat’s hydrodynamics.“
According to Friedrich Judel, TopSolid’s function for chamfering surfaces with variable radii, which are common in shipbuilding, needs to be improved particularly. A typical application is the transition from hull to keel beginning with a small radius at the front that increases towards the middle and is almost zero towards the end. “Consistent chamfers are not a problem at all, but chamfering from a wider to an extremely small radius, or even chamfering corners, takes ages,“ Judel explains. “That is the reason why in the beginning, we kept on cutting that type of surface with MultiSurf and then transferred the geometries to TopSolid via the IGES interface.“
Detailing with a 2D system
Yacht designers do not only shape the body of a boat using a 3D system, but also its entire interior, albeit not including all details. “We use 3D whenever components will be mounted in order to ensure that everything matches perfectly,“ Ulrich says. “Simplified 3D models are used to determine a boat’s geometries, to adjust the interior to structural components and to control the ropes on winches or blocks.“ Additionally, TopSolid calculates the volume centers of gravity of the boat structure’s double bottom tanks.
The boat design is detailed with a 2D system. For this purpose, the users cut the 3D model and then transfer the geometry to AutoCAD. “In TopSolid the transition from 3D to 2D is child’s play since the system can output DWG data directly,“ Ulrich explains. If required, the cuts are altered so that 3D model and 2D drawings do not perfectly match. Data are mostly inconsistent until the boat is finished since numerous change requests from the customer or the shipyard need to be implemented in the design process. These changes are not transferred to the data model. This holds true for both building ships and houses.
2D drawings still are the most important documents in shipbuilding. They can be generated in AutoCAD in no time since ready-to-use snippets already exist for many supplied parts which can easily be incorporated into the drawing. For interior design and furnishing, judel/vrolijk°&°co supplies manufacturing drawings with a scale of up to 1:1. All 3D data are reused for boat manufacturing only selectively, e.g. for milling the keels or frames which are subsequently planked and serve as a skeleton form for building the plastic hull. It is primarily the shipbuilders who benefit therefrom and according to Conradi, they meanwhile take this use for granted.
Communication via 3D models
Friedrich Judel emphasizes that 3D models are crucial for the communication between yacht designers, shipbuilders and customers. “If there are discussions with the shipyard about the position of certain parts, you can for instance visualize the engine room in 3D. In 2D, you can only identify potential problems after the part has been assembled.“ On top of that, customers can more easily picture the finished boat with the help of a 3D model and therefore express change requests earlier on in the design process. With TopSolid you can easily generate video sequences of 3D models and show the customer how certain mechanisms will work.
The major benefit of 3D is the identification of part collisions on the digital boat model which greatly reduces the number of errors due to overlapping features. “This is why I strongly support the use of 3D,“ Conradi says. The kinematic functions of TopSolid enable the users to simulate the most complex 3D kinematics on screen in order to avoid collisions. “A good case in point is the anchor at the bow that needs to swing around the forestay during opening,“ Ulrich explains. “In the past, we would have needed to build a realistic model.“
However, using 3D does not save a lot of design and manufacturing time since the company’s requirements have increased. “The time you gain is used up for working on variations and for inspecting things in detail that you would not have looked at before,“ Conradi says. “We just try out more things and optimize to a greater extent. This in turn makes our boats more perfect and we can better meet the customers’ requirements.“
By Michael Wendenburg, Sevilla
Photos BG Concept Marketing Communication
Need more information