24 July 2012
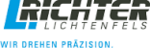
The 14-speed gear hub from Rohloff is no doubt quite familiar to any enthusiastic mountain biker, yet very few of them would be familiar with the name L. Richter. The company based in the German town of Lichtenfels, Hesse, manufactures the complex aluminium parts for couplings fulfilling the highest requirements of quality and precision. The millturn machining is programmed on modern machining centres using TopSolid’Cam from Missler Software, which reduces the tooling times considerably.
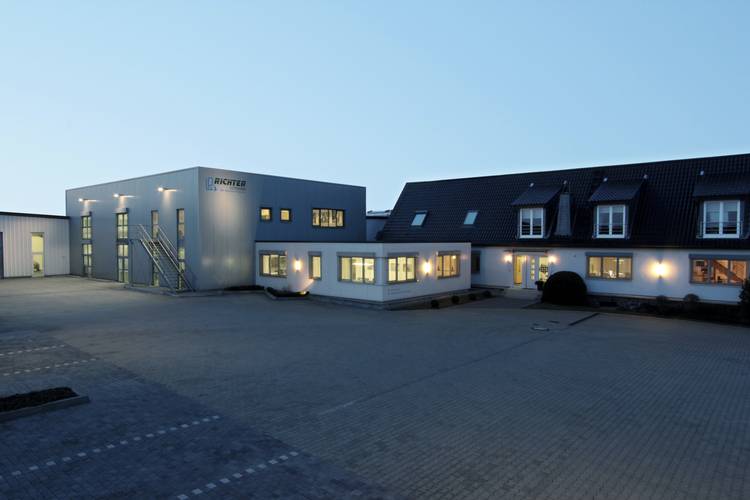
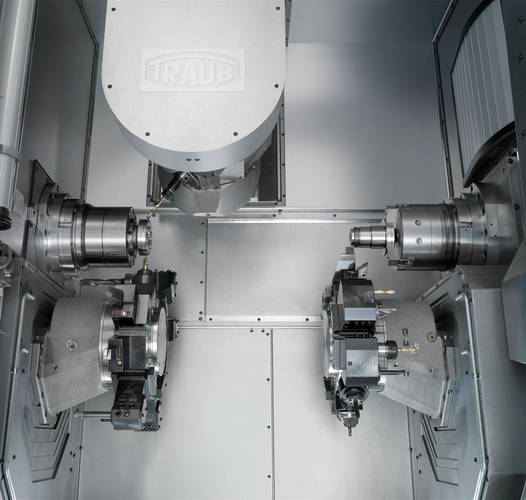
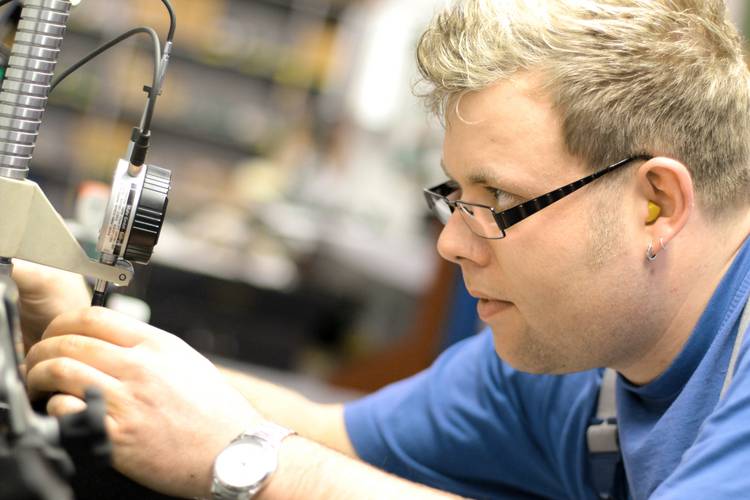
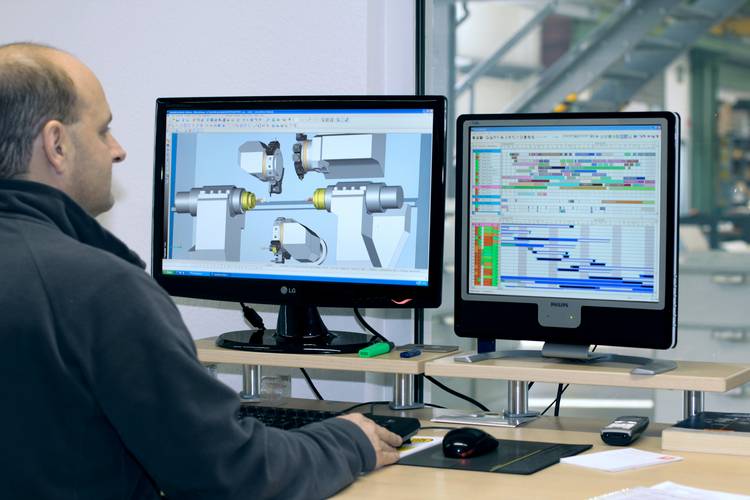
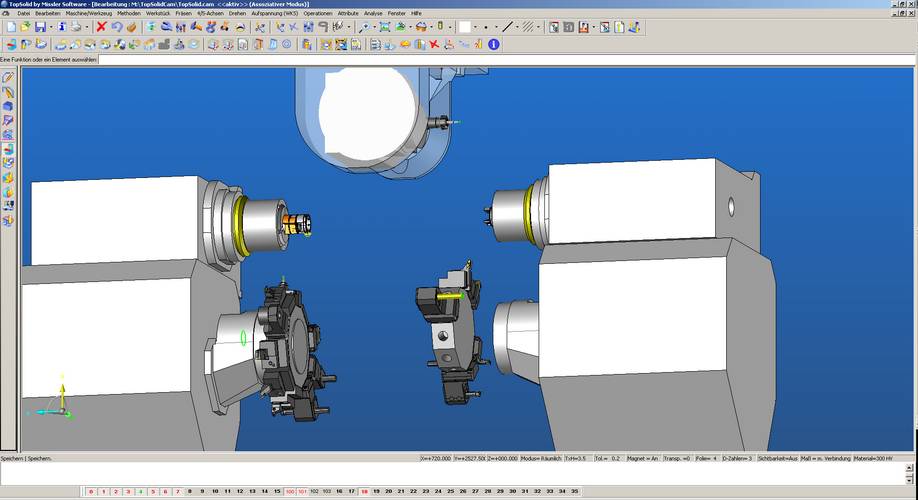
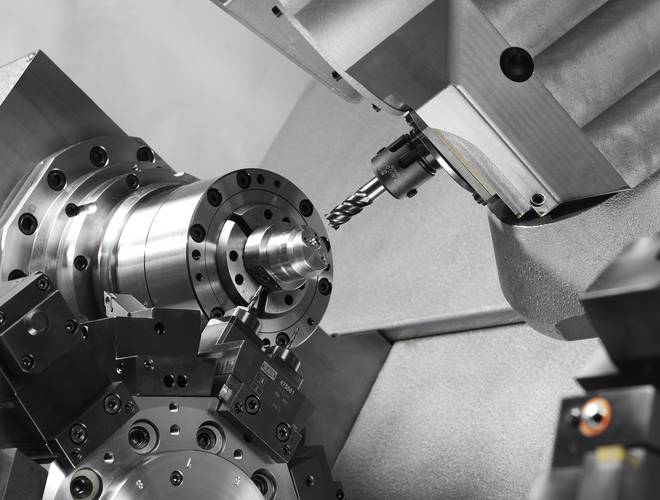
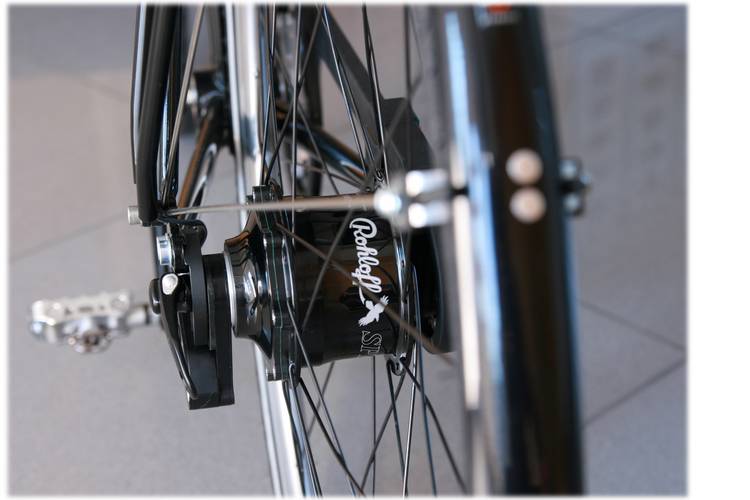
L. Richter KG of Lichtenfels is one of those companies which demonstrate that even in Germany you can remain competitive as a small manufacturing company if you specialize judiciously. Founded almost 50 years ago as a traditional metal forming works, which produced simple brass parts in high batch quantities, this family company with currently 25 employees has developed through the implementation of modern CNC machines and CAM programming technology to become a recognised manufacturing partner for the production of complex precision parts made from challenging materials. Along with stainless steel, Richter works predominantly with aluminium, but also with plastics.
For the Lichtenfels-based manufacturing specialists, complex parts are turned parts involving a high degree of milling. The degree of their complexity can be gauged by reference to the machining times. On the new Traub TNX65/42 millturn centre, which is equipped with a main and counter spindle, two tool turrets, pivoting milling spindle and chain magazine, a stainless steel part can now be completely machined. Although the 50 or so turning and milling tools are working simultaneously or overlapping on both spindles, the machining takes in all 24 minutes. "Normally, a turned part runs here for 2 to 3 minutes," says Matthias Richter, the second-generation company boss.
Consistent quality of parts
Richter works for customers in various industries, who often do not have their own manufacturing facilities, and for many it is even the sole supplier for certain components. "Reliability and quality are what our customers value in us," says Mr. Richter. "Our strength is the combination of complicated parts and materials, sticking to schedules and consistent quality. Our self-imposed standards are often higher than those dictated by the customers, particularly where surface finishing is concerned." Precision that is visible and measurable: in order to check the dimensional accuracy of parts, the company has set up its own computer-supported quality assurance. This means that there are practically zero returns.
The use of new technologies plays a key role in the company’s success, alongside the qualification of the employees. The first CNC machine - a Traub – was procured in 1979 by Mr. Richter's father, for the machining of complex parts and materials. Since 1989, all machines are programmed off-line, in order to keep downtime to a minimum. "The procurement of the first programming system from Index, which still ran on VAX computers, represented a massive investment for a company of our size," recalls the company boss, who himself is a programmer. Three years ago the company replaced the 2½-D solution with the TopSolid’Cam 3D CAD/CAM system, in order to better exploit the potential of the multiple axis machines and reduce tooling times. The new CAD/CAM solution is currently in use on three workstations.
Short tooling times are an important criterion for the company, in order to react flexibly to customer desires and be able to manufacture parts in small batch sizes while remaining cost-effective. "On the more complex machines we manufacture, per batch, from 250 up to a maximum 5000 units; on the simpler ones, smaller batches still," Mr. Richter explains. "Here we have only very few machines which run for longer than 10 days on any given job. Normally, their tools are changed every day, sometimes even several times a day."
Benefits of the new Traub machine
The company's machine pool comprises, along with the new Traub TXN65/42 millturn centre, Index C100 automatic lathes, equipped with three tool turrets for the manufacturing of larger batch volumes, and several Index G200 4-axis machining centres each configured with two spindles and turrets, fitted with driven tools for combined turning and milling. For the machining of less complex parts, they also have simpler automatic lathes. The operators at Richter are so comprehensively trained that they can operate every machine, even though the Traub - unlike the Index machines - is not equipped with a Siemens but with a TNX or Mitsubishi controller.
The procurement of the new machining centre meant additional costs for the extra milling spindle, but these have paid for themselves in every respect. The company is now capable of the complete machining of turned parts with complex milling requirements. "We have leapt from the parts spectrum into whole new dimensions, and have marked ourselves out even more clearly from the competition," says Mr. Richter. "Service providers who use a machine like this are few and far between."
Richter was already using the Index machines for complete machining, but increasingly came up against limits with the driven tools in the - rigid - turrets, for example, when machining steep bores and threads, or because not as many tools as were required could be housed in the turrets. "Driven tools also have the drawback of being considerably more expensive than normal HSK tools, they wear more quickly, they take longer to change and they do not reach the same rotation speeds," explains Mr. Richter. "For turned parts involving a great deal of milling, we are therefore quicker with the Traub both with the tooling and with the machining, which makes up for the higher machine hourly rate."
Finding the right partner
All the machines are connected via high-performance post-processors to TopSolid’Cam and are, apart from a very few operations, supplied with the NC code from the new CAM application. The connection with the machine pool was handled by the Missler Software sales partner AdeQuate Solutions, which not only programmed the post-processors, but also generated the 3D machine models for the simulation and, if made available by the manufacturer, mapped out the kinematics in the models. In order to minimize the software maintenance effort, Richter largely dispenses with customer-specific adaptations to the post-processors, with the exception of some machining cycles that were not contained in the standard.
The programming of the post-processor for the millturn centre from Traub was virgin territory for AdeQuate Solutions. This involved the programmers having to take account of a number of particularities with the TNX control; for example, the fact that the cutting radius correction when machining on the counter spindle is calculated in reverse, which initially led to contour problems. The real challenge however consisted in mapping out the many machining options. Not only can the milling spindle, for example, pivot through 180°, but it can also turn on its own axis and lock out, so that it is possible when turning with two offset tools to load a further cutting tool. Or else it is possible to brace longer turned parts against a tailstock that is clamped in the turret of the counter spindle.
"For us as a supplier, the machine is optimal because it can be deployed in so many ways, but this must also be supported by the post-processor," explains Mr. Richter, who in this regard is full of glowing praise for the competence of the Lahr-based software company and the service quality: "All post-processors were usable straight away, so that we could program with them immediately, and if an operation is not optimally supported, we receive an updated post-processor within 24 hours. We really get the best possible support from AdeQuate Solutions."
System selection at the second attempt
If the Lahr-based systems vendor had not existed, the company would have probably opted for a different CAM solution. In the processor system selection, TopSolid was initially rejected, as presented by another provider. Although the software offered the best support for turning and milling out of all the systems under consideration, in the course of the system presentation it appeared to the operators to be too complicated in use. Then, thanks to a tip from an acquaintance, contact was made with AdeQuate Solutions. "We initially overestimated the effort required for the 3D modelling. When an employee from AdeQuate Solutions demonstrated to us on a complex part just how simply you could create your model and program the machining steps on the basis of a 2D drawing, we were quite taken aback," says Mr. Richter. "It goes to show that you don't just need the right system, you also need the right partner."
The integrated CAD functions are a key strength of TopSolid’Cam, as Mr. Richter goes on to demonstrate. They are important for the CAM programmers because the latter do not receive 3D data from all customers, and they have to initially model the parts in order to be able to do any programming whatsoever. Yet even if they do receive 3D data, adaptations often have to be made to the geometry, since the customer's designers normally create their models with nominal dimensions without taking into account the manufacturing tolerances. Although TopSolid offers good support for such adaptations, it is sometimes more efficient to completely recreate the model in order to be able to exploit the benefits of the associativity between CAD and CAM models. "The CAM programs then make it still easier to update the geometry in the event of changes being made," explains Mr. Richter.
Even if users must first of all generate a 3D model which, thanks to this becoming increasingly routine, also proceeds more quickly than it did two years ago, they subsequently save time on the programming of the turning and milling operations. All they then need to do is to click on the surfaces to be machined, select the tool and define the cutting parameters. Previously, they had to transfer dimensions and cutting points, manually in part, from the CAD drawing, which was relatively time-consuming. Above all, they can proceed far more quickly with changes, since they do not need to recreate the CAM programs (or even only parts of them), they simply need to recalculate. "If the 3D data from the customer is not clean, today we have no hesitation in simply reworking the data," says Mr. Richter. Sometimes the manufacturing specialists make available their model data to customers who are not yet deploying any 3D system.
Optimisation of multiple axis machining
The integrated CAD/CAM process chain also has massive benefits in terms of quality assurance, as Mr. Richter goes on to say. The measurements and tolerances defined in the model or drawing can then be transmitted in DXF format to the company’s computer aided quality software and used for the automatic generation of the test plans. Each part at Richter is 100%-tested and documented prior to release for serial production. The finishers are responsible for the quality of their parts, and they also measure critical dimensions on samples taken from serial production. "We program the machining partly by matching it up to the geometry that is to be examined, and thereby guarantee high process reliability," stresses Mr. Richter.
The programmers also use the CAD functions for incorporating tools, tool holders and clamping systems one-by-one in TopSolid’Tool. Initially, this required no small effort, but today this is paying off, as Mr. Richter explains. Thanks to the comprehensive mapping of the machine environment, users can reliably simulate and optimize their CAM programs on the computer. The new CAM solution offers the possibility, among other things, to calculate and minimize the machine running times through the optimal organization of the machining steps on the main and counter spindle with the aid of a graphic flowchart. Previously, the programmers had to do this in their heads, in order sometimes then to find out only when running-in the program that this did not function as had been intended.
Thanks to the simulation and visualization of the CAM machining, Richter machines are today tooled considerably faster. This above all is down to the fact that the programs running on the machines are technologically flawless and run entirely smoothly. Previously there were many adaptation difficulties that could only be eliminated during running-in, and for the machine operators it was not easy to understand what the machine was doing or what it should actually be doing. They can now take a look at this on the computer and can therefore have greater confidence when it comes to the running-in. "With complex parts, thanks to the optimal preparation of the programs, we have definitely gained 25 to 30% on the tooling times," says Mr. Richter. "The optimal synchronisation of multiple-axis machining also contributes to the minimization of the machine running times."
Need more information