18 décembre 2009
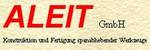
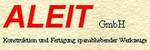
La société Aleit GmbH est elle-même son client le plus exigeant : elle fabrique des outils d’usinage de précision grâce à la toute dernière technologie d’enlèvement de copeaux. En programmant ses centres de fraisage et ses machines multitâches à l’aide du logiciel TopSolid’Cam de Missler Software, elle réduit sensiblement la période de rodage.
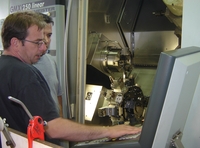
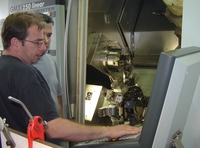
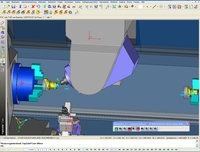
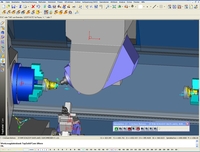
L’outil adéquat pour un usinage complet
Fondée en 1961 par le père de son propriétaire actuel, Holger Aleit, la société Aleit, basée à Steffenberg, emploie aujourd’hui 31 collaborateurs. Spécialiste de la construction et de la fabrication de systèmes et d’outils de précision destinés à l’usinage par enlèvement de copeaux, elle se positionne, dans cette activité, comme un prestataire de services qui propose des solutions complètes : du conseil et de l’analyse jusqu’à la programmation FAO et à la fabrication, en passant par la conception et la production des outils, le tout dans le respect de normes de qualité ISO rigoureuses. Parmi ses clients se côtoient grandes multinationales et petits fournisseurs d’outils de coupe et de plaquettes.
Si elle commercialise une gamme d’outils standard, Aleit est avant tout un producteur de solutions « sur mesure », élaborées et mises au point à la demande de fabricants d’outils ou de grandes entreprises du secteur industriel. Les exigences de qualité, de productivité et de précision de ces outils grandissant à chaque génération de machines, Aleit élabore constamment de nouvelles technologies qui accélèrent et optimisent l’usinage par enlèvement de copeaux. Certaines sont mêmes brevetées, à l’instar d’une fraise à surfacer munie de plaquettes amovibles en diamant polycristallin qui, une fois montée, dépasse une précision axiale et radiale de 5 µm.
« Nos principaux atouts résident dans la capacité d’innovation de nos collaborateurs et la souplesse que nous prête la petite taille de notre structure », explique Holger Aleit. « La plupart de nos concurrents sont de grandes entreprises. Il est difficile de trouver une société de notre taille qui possède le personnel, les machines et les instruments de mesure nécessaires pour travailler sur ces outils complexes et précis. Notre entreprise est une forge ultramoderne qui emploie des collaborateurs qualifiés, capables de manier des machines et des logiciels sophistiqués. »
Tournage-fraisage de haute précision
Prévoyant d’usiner des pièces de plus en plus complexes et de plus en plus précises, la société s’est munie de deux centres de tournage-fraisage de marque DMG à neuf axes et 80 emplacements d’outils. En outre, elle utilise plusieurs fraiseuses à cinq axes, une fraiseuse à quatre axes de type DMC et un centre de tournage bi broche de type MF Twin provenant de chez DMG, ainsi qu’un centre d’usinage à cinq broches de marque STAMA. Une rectifieuse Studer flambant neuve complète l’équipement. Par ailleurs, Aleit a récemment installé une chambre de mesure de coordonnées climatisée et protégée des vibrations, qu’elle souhaite faire homologuer par les services d’étalonnage allemands du DKD (Deutschen Kalibrierdienst). Elle sera ainsi à pied d’œuvre pour l’intégration du raccord Coromant Capto à la norme DIN. Aleit est en effet l’un des premiers entrepreneurs capables de fabriquer des outils et des systèmes avec ce raccord, résultat qui implique l’usinage de tronçons polygonaux d’épaisseur constante et le respect d’une précision de contours inférieure à 4 µm. « Lorsque l’on déclare atteindre une précision inférieure au millième de millimètre, il faut également être en mesure de le prouver », remarque Holger Aleit.
L’acquisition des machines multitâches est l’une des principales raisons qui ont poussé Aleit à adopter le logiciel TopSolid de Missler Software, début 2006. « La réduction du temps de préparation et de mise en route joue un rôle crucial dans une production en petite série comme la nôtre, surtout avec des machines aussi chères », souligne Aleit. « L’optimisation du fonctionnement des machines et la synchronisation des nombreux axes utilisés constituent un véritable défi pour les programmeurs. Les logiciels du type TopSolid leur sont particulièrement utiles, puisqu’ils leur permettent aussi bien d’analyser les collisions possibles dès la programmation que de voir comment l’usinage se répartit entre les tourelles et les broches. »
Soucieuse de maîtriser la complexité des outils, Aleit a investi dès 1999 dans un système de construction 3D qui interagit avec GOelan, un outil de FAO de Missler Software. Toutefois, cette solution ne permettait ni l’exploitation multitâche, ni la simulation de l’usinage dans un environnement virtuel. « Nous étions très contents des fonctions de fraisage de GOelan, mais nous ne voulions pas multiplier les systèmes de programmation ; c’est pourquoi nous avons décidé de passer à TopSolid », explique Volker Michel, responsable de production. Aujourd’hui, le logiciel tourne sur trois PC, dont deux sont consacrés à la construction et à la programmation FAO, le troisième étant essentiellement réservé à la formation.
Intégration CAO – FAO
Les puissantes fonctions de CAO de TopSolid, combinées à l’interaction entre CAO et FAO, favorisent grandement la satisfaction des besoins de l’utilisateur. Souvent, le client ne fournit pas d’outil fini, mais seulement des dessins ou une géométrie de plaquettes, qu’Aleit prend pour base du développement d’outils. « Nous effectuons beaucoup de travail de construction, non seulement pour les petits clients, mais aussi, désormais, pour certains des grands », déclare Michael Weber, constructeur et programmeur chez Aleit : « Dans ce cas, nous modélisons les outils dans TopSolid, puis nous programmons l’usinage à partir de la géométrie obtenue ; cela nous permet de répercuter directement les modifications de géométrie dans le programme de FAO. »
L’élément qui a emporté la conviction d’Aleit, c’est la fiabilité des fonctions de simulation et de mise à jour automatique du brut de TopSolid’Cam, même si la conversion par le post-processeur ne se juge naturellement qu’après coup, comme l’affirme Weber : « Aussi performant que soit votre logiciel de FAO, le développeur du post-processeur doit avant tout avoir les compétences requises. Avec AdeQuate Solutions, nous étions toutefois presque certains d’obtenir de bons résultats : ils sont déjà à l’origine du développement des post-processeurs de GOelan. » La société AdeQuate Solutions, partenaire commercial de Missler Software basé à Lahr, ne s’est pas contentée de fournir les post-processeurs attendus, mais a également aidé Aleit à préparer et à reproduire ses modèles de machines, alors que le fabricant de ces dernières fournissait juste une partie des données de base nécessaires, l’autre partie étant à modéliser dans TopSolid.
Si l’adaptation de la plupart des post-processeurs a progressé assez vite, les centres de tournage-fraisage DMG ont, quant à eux, connu quelques ratés de départ. Ces difficultés, dues notamment à la complexité des machines et à la spécificité de leur structure de programmes, tenaient aussi à l’inexpérience des opérateurs amenés à utiliser les programmes CNC issus des post-processeurs. Le fonctionnement de ces derniers a néanmoins été stabilisé, de sorte qu’il ne reste désormais que de légers ajustements à effectuer.
Formation des utilisateurs
Si les utilisateurs ont bénéficié de cinq jours de formation à TopSolid sous la conduite d’AdeQuate Solutions, il s’est néanmoins écoulé un semestre entier avant que la productivité ne revienne au niveau précédant le changement d’outil. Le nouveau système a bouleversé les méthodes de travail, obligeant les utilisateurs à revoir leur démarche de fond en comble, comme le précise Weber : « Auparavant, je pouvais programmer des pièces simples en quelques minutes. Maintenant, cela me prend plus de temps : il me faut d’abord créer le brut et l’équipement avant de programmer l’usinage sur la machine virtuelle. Les outils doivent s’accorder avec le montage et le reste pour que nous puissions prévoir les éventuelles collisions. Ainsi, une fois que j’ai regardé la simulation et équipé la machine d’outils identiques à ceux de TopSolid, je suis sûr à 99 % que mon programme de FAO ne provoquera pas de collision. »
Plus les pièces sont complexes, plus le logiciel TopSolid accélère la programmation, résultat auquel concourent sa facilité d’utilisation et la simplification du contrôle des étapes de l’usinage. La prévisualisation de ce dernier révèle les courses et les collisions possibles. Enfin, la programmation demande moins d’efforts, car TopSolid permet de définir des cycles d’usinage réutilisables pour les perçages, les poches et d’autres éléments de géométrie. « Malheureusement, cela ne concerne pas nos supports de plaquette, qui sont géométriquement trop complexes et trop divers », regrette Michel.
Qualité de la synchronisation de l’usinage
L’un des points forts de TopSolid, concernant la programmation de machines multitâches, réside dans la synchronisation des opérations d’usinage, fonction qui vise aussi bien à empêcher les collisions qu’à répartir harmonieusement la charge de travail entre les machines. Accédant aux valeurs de coupe de tous les outils, le logiciel peut calculer avec précision la durée d’usinage de chaque opération. Les résultats sont présentés sous la forme d’un diagramme à barres très lisible, ce qui facilite l’optimisation du temps machine : « Si la tourelle montée sur la broche principale fonctionne pendant une minute, j’essaie, par exemple, de programmer la tête de fraisage de la broche secondaire pour deux opérations courtes », mentionne Weber.
Exceptées quelques demandes d’améliorations mineures, les utilisateurs sont très contents de TopSolid. L’adoption du logiciel n’a pas seulement accéléré la programmation : elle contribue fortement à la réduction du temps de préparation et de mise en route. Il serait toutefois difficile d’évaluer les économies réalisées, car les outils sont devenus plus complexes et le matériel a totalement changé en cinq ou six ans. « Pour gagner du temps en production, nous transférons le travail au bureau technique, car un ordinateur coûte moins cher qu’une machine », indique Michel. « Souvent, nous passons près de trois jours à programmer un outil et seulement une journée à l’installer. Auparavant, cela nous aurait pris plus de temps. »
Naturellement, le temps gagné lors de la mise en route dépend aussi de la machine et de l’opérateur. Devant un centre d’usinage qui s’adapte aux changements d’outils entre copeaux en 1,8 seconde à peine, c’est l’utilisateur qui ne « suit » plus. Les jeunes collaborateurs qui ont évolué avec cette génération de machines sont donc plus enclins à se fier aux programmeurs que les « anciens » de la fabrication, qui contrôlent tous les détails lors de la mise en route. « Nous devons être d’autant plus exigeants lors du contrôle de nos programmes de FAO », déclare Weber, fier de la forte baisse du nombre de collisions observée depuis l’introduction de TopSolid. Quant à la société, elle a bon espoir de dépasser la production d’outils KM ou HSK et d’usiner des outils et systèmes Coromant Capto de haute qualité en s’appuyant sur TopSolid.
Besoin de plus d'informations
UNE QUESTION SUR NOS
PRODUITS OU SOLUTIONS ?
Trouvez le point de vente le plus proche Contactez-nous Demandez un devis