25 août 2010
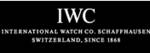
International Watch Company utilise TopSolid'Cam pour usiner.
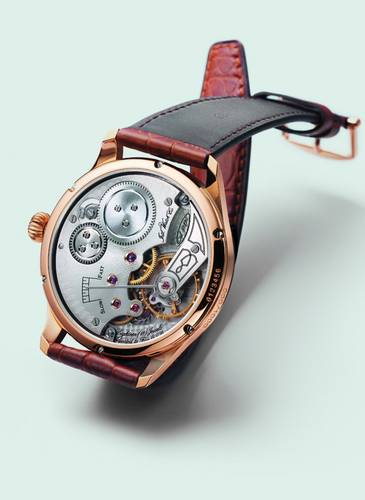
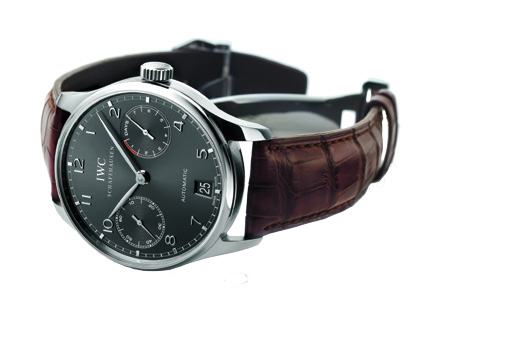
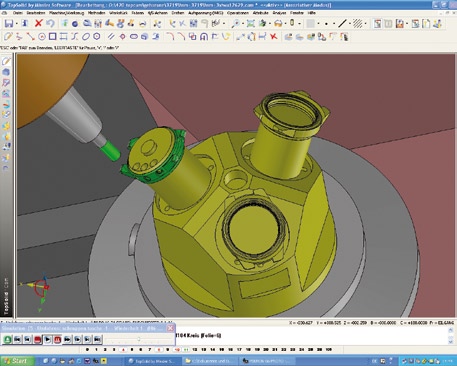
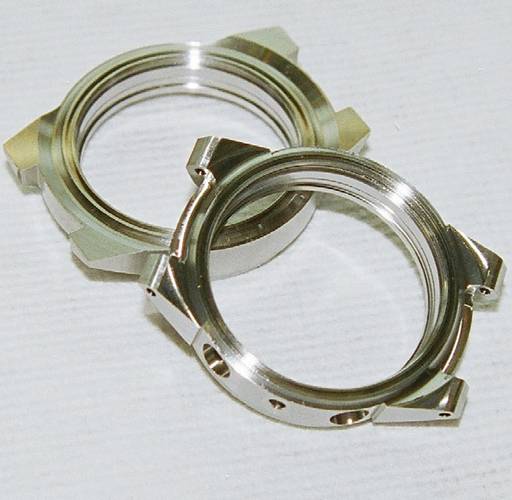
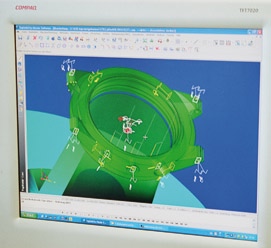
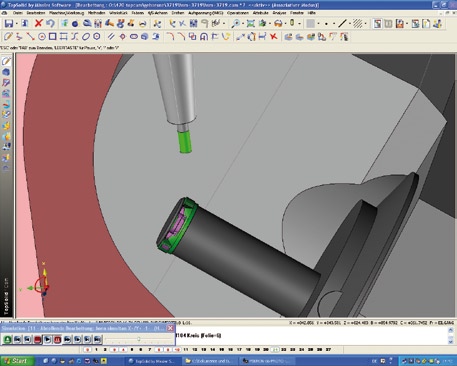
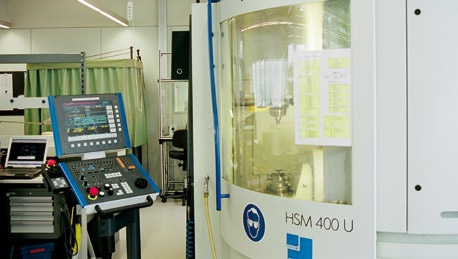
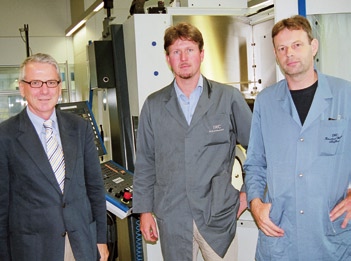
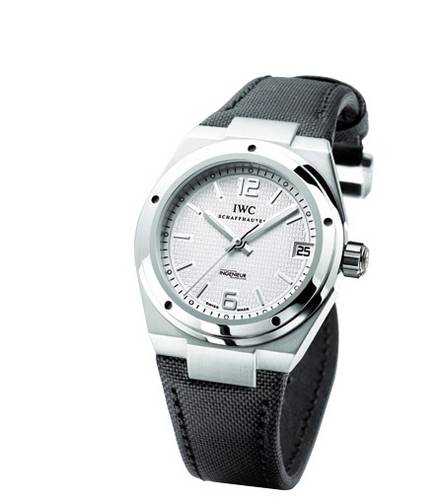
Précision et durabilité
Inutile de présenter IWC, International Watch Company, aux véritables amateurs de montres: les chronomètres de Schaffhouse sont connus dans le monde entier. D’aussi beaux objets que les montres IWC, font appel - comme on s’en doute - à une extrême précision. Dans le secteur CFAO, tout repose sur le système TopSolid’Cam de Missler Software, qui permet de réaliser tous les programmes à commande numérique nécessaires à la fabrication des mouvements, des boîtiers et des moyens et auxiliaires de production.
Schaffhouse – beaucoup de gens pensent en premier lieu aux chutes du Rhin, qui sont les plus grandes d’Europe. Les amateurs de belle horlogerie savent que Schaffhouse est également le berceau d’IWC, l’une des manufactures horlogères les plus connues et les plus réputées au monde. Les montres IWC sont devenues des objets cultes! Mais pourquoi en est-il ainsi ?
La réponse à une telle question se trouve déjà dans le titre. Les montres IWC sont extrêmement précises. Tous ceux qui ont le privilège de porter de telles montres vous diront qu’ils n’ont nul besoin de remettre leur montre à l’heure pendant des semaines, voire des mois entiers puisque le décalage par rapport à l’heure exacte est absolument insignifiant. Les montres IWC sont en outre d’une extrême longévité. On rencontre couramment des personnes qui exhibent avec fierté une IWC des années '50 et qui la portent vraiment puisqu’elles sont encore parfaitement fonctionnelles. Quel autre bien de consommation aurait de nos jours une telle durabilité ?
IWC réalise des montres d’une extrême robustesse, la série « Ingénieur » par exemple. Un horloger de Nuremberg l’exprimait ainsi: « Si vous l’achetez, vous n’aurez plus besoin d’aucune montre durant cette vie!“ Voilà un témoignage fort éloquent.
IWC réalise des montres dans diverses collections axées sur les principaux éléments tels que la terre, l’eau, l’air. L’Aquatimer est clairement liée à l’eau, l’Ingénieur à la terre et les montres d’aviateur qui ont été fortement remaniées cette année, sont indissociablement liées à l’air.
Parallèlement aux montres tout à fait conventionnelles, on en trouve certaines chez IWC qui disposent de complications plus ou moins grandes, telles que réserve de mouvement, phases de la lune, fonctions de chronométrage, répétition des minutes et calendrier perpétuel. C’est avec « Il Destriero Scafusia », véritable cheval de bataille de Schaffhouse, qui compte au nombre des « grandes complications » et qui a vu le jour en 1993 à l’occasion du jubilé des 125 ans d’IWC, que l’on a véritablement dépassé et surpassé tout ce qui existait ou s’était fait jusqu’alors.
La société IWC
L’entreprise a été créée en 1868 par un américain de Boston, F. A. Jones. Il a posé la première pierre de toute la carrière de cette usine horlogère. IWC emploie aujourd’hui près de 500 collaborateurs et appartient au groupe d’articles de luxe Richmont au même titre que A. Lange & Fils et Jaeger-LeCoultre.
Outre les boîtiers qui sont présentés ici, IWC construit elle-même toute une série de mouvements et de modules annexes et la tendance est à la hausse. Les familles de calibres 5000 et 8000 en font naturellement partie.
Le développement et la construction, ainsi que la programmation CN et l’ensemble de la fabrication proprement dite font nécessairement appel à des technologies dernières cri.
Pour la FAO IWC travaille avec TopSolid’Cam de Missler Software, et fait appel à Kern et Mikron pour les centres d’usinage. Les postprocesseurs viennent de chez NCDATA (revendeur TopSolid en Suisse).
Programmation à commande numérique et usinage réel en symbiose parfaite
WC a jadis travaillé avec un système de programmation à commande numérique de DLog, qui semble relativement élémentaire aujourd’hui. « Lorsque nous avons introduit un système de CAO et diverses machines modernes d’usinage 5 axes, la programmation à commande numérique a dû faire également un grand pas en avant“, souligne Beat Pletscher, responsable de la fabrication des boîtiers. « Nous avons effectué une recherche de marché durant laquelle nous nous sommes adressés à quatre ou cinq fournisseurs de systèmes“, ajoute Christian Graber, gérant de NCDATA à Schlieren, près de Zürich.
Après une présentation très poussée du système, Graber et son équipe ont obtenu le contrat. IWC a choisi TopSolid’Cam pour les raisons suivantes:
- TopSolid’Cam était le seul système de programmation à commande numérique avec lequel nous pouvions (et pouvons encore) travailler « comme si l’on se tenait juste devant la machine“ (Graber). La logique de fonctionnement correspond exactement à la logique des opérateurs des machines d’usinage. IWC en fut heureux puisque les quatre postes de travail TopSolid’Cam sont décentralisés et sont directement assumés par les praticiens dans les départements spécialisés.
- Nous continuons à apprécier les possibilités de simulation qui ne concernent pas seulement le travail de coupe, mais englobent l’ensemble de l’espace de travail.
- TopSolid’Cam possède une interface directe avec SolidEdge. Les données peuvent ainsi être reprises dans le système de programmation à commande numérique.
- TopSolid’Cam offre la possibilité de mémoriser des processus et le savoir-faire du client et permet ainsi d’accroître notablement la productivité
Le système de programmation à commande numérique est aujourd’hui utilisé sur les centres d’usinage de tournage, fraisage et érosion par fil dans les départements de fabrication des pièces de mouvement, de fabrication des boîtiers et de fabrication des moyens de production. La programmation actuelle s’effectue en 2, 3 et 5 axes.
"Dans la fabrication des boîtiers, nous travaillons de plus en plus en 5 axes simultanément", explique Beat Pletscher, "et par exemple, les boîtiers du modèle actuel « Ingénieur », et de « l’Aquatimer » ont vu le jour ainsi".
TopSolid'Cam : un logiciel complet de FAO
TopSolid´Cam est un système de programmation à commande numérique pour la production et le calcul d’outils principalement destinés aux modes d’usinage tournage, fraisage et perçage ainsi qu’à des combinaisons de ces modes d’usinage. Le système fonctionne sur la base de solides. Tous les parcours d’outils sont générés par mise en référence constante de deux modèles géométriques, celui de la pièce brute et celui de la pièce finie. Le modèle de pièce brute est actualisé après chaque usinage, ce qui permet de toujours travailler sur une géométrie actualisée. Ce procédé présente les avantages suivants:
- Evitement de collisions et
- Réalisation de déplacements d’outils optimisés puisque l’on connaît de façon continue et avec précision la quantité de matière résiduelle.
On dispose de trois « niveaux de confort » lors de la réalisation de programmes à commande numérique:
- Analyse topologique exclusive du modèle de pièce
- Programmation semi-automatique sur la base de courbes 2D
- Elaboration automatique de programmes à commande numérique en utilisant la technologie basée sur des features automatiquement identifiées à partir de modèles importés
L’importation des données s’effectue au moyen d’interfaces standard telles qu’IGES, STEP, Parasolid, DXF/DWG, SAT ou d’interfaces directes vers Catia V4/V5, Pro/Engineer, ME10, Solidworks et Solidedge.
Le système propose toute une ample bibliothèque d’outils qui peut et devrai être complétée de façon spécifique en fonction de l’utilisateur.
TopSolid´Cam dispose d’un système de simulation moderne permettant de vérifier la qualité des déplacements d’outils. Le confort d’utilisation est tel qu’il est possible d’intégrer l’ensemble de la machine outil dans la simulation, ce qui permet d'éviter des collisions éventuelles et de raccourcir la durée ultérieure du démarrage.
TopSolid´Cam soutient en continu les usinages à grande vitesse. Le logiciel dispose naturellement de fonctions étendues pour un usinage simultané 5 axes.
En fin de compte
Le premier avantage essentiel que TopSolid’Cam apporte à l’entreprise de Schaffhouse, est celui du gain de temps. « Lorsque les post processeurs fonctionnent parfaitement, nous pouvons économiser 50% de la durée initiale de programmation à commande numérique“, explique Jörg Demmerle, qui programme les boîtiers sur le système.
Le second point, est la faisabilité. Le « design » des boîtiers actuels ne pourraient pas être réalisés de façon rentable sans technologie 5 axes, on a tout simplement besoin pour la programmation d’un système haut de gamme, tel que celui qui a été présenté.
Les nombreuses possibilités de simulation ont largement fait leurs preuves. Chez IWC on fait appel à des usinages multiples sur les boîtiers. Il est de plus en plus difficile d’éviter toute collision « au jugé ». Seule une simulation d’une extrême précision permet d’y parvenir.
L’autre avantage majeur de TopSolid’Cam est que nous avons toujours atteint nos objectifs de programmation. Nous n’avons jamais dû abandonner et nous avons pu travailler avec des moyens pratiquement conventionnels.
Compte tenu de la perfection du travail réalisé en étroite collaboration entre le système de programmation et la machine, la part de travail manuel sur les boîtiers a tendance à baisser. Un tel avantage permet également d’économiser de l’argent.
Que peut-on ajouter à tout ce qui vient d’être dit?
IWC et Missler Software semblent parfaitement s’harmoniser. Exigences et possibilités se correspondent. Précision et disponibilité existent des deux côtés. On ne peut que se réjouir des futurs développements passionnants…
Besoin de plus d'informations
UNE QUESTION SUR NOS
PRODUITS OU SOLUTIONS ?
Trouvez le point de vente le plus proche Contactez-nous Demandez un devis