26 septembre 2011
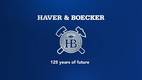
Au début de l'année 2010, le fabricant de machines Haver & Boecker, spécialiste internationalement reconnu du remplissage et du conditionnement de matériaux en vrac, s'est équipé d'un nouveau centre d'usinage à colonne mobile AXA. Le logiciel TopSolid’Cam de Missler Software fournit les programmes de commande numérique requis à la machine, qui fonctionne inlassablement en 3x8. En l'espace de six mois, les programmeurs FAO ont généré plus de 500 programmes pour la machine AXA.
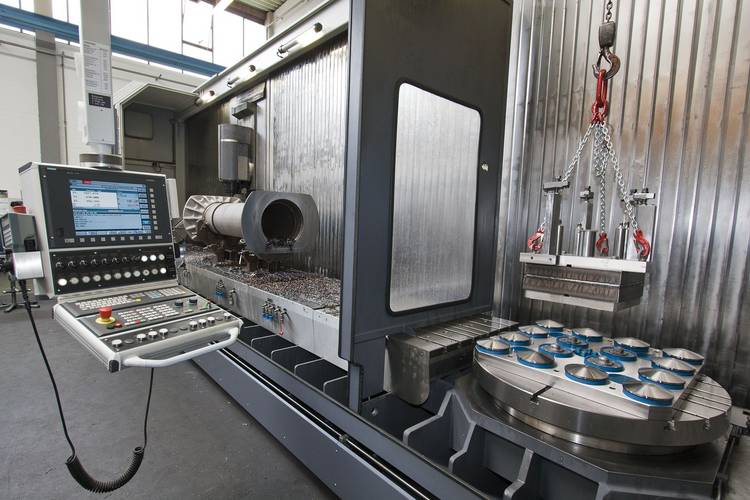
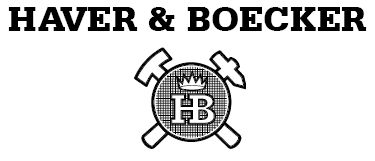
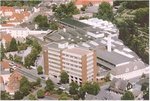
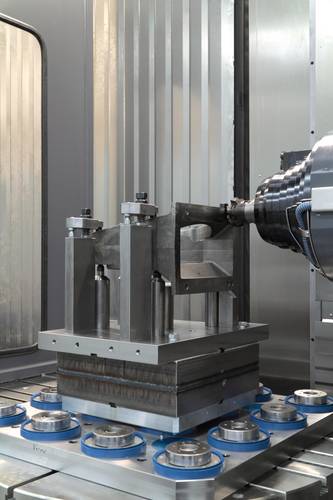
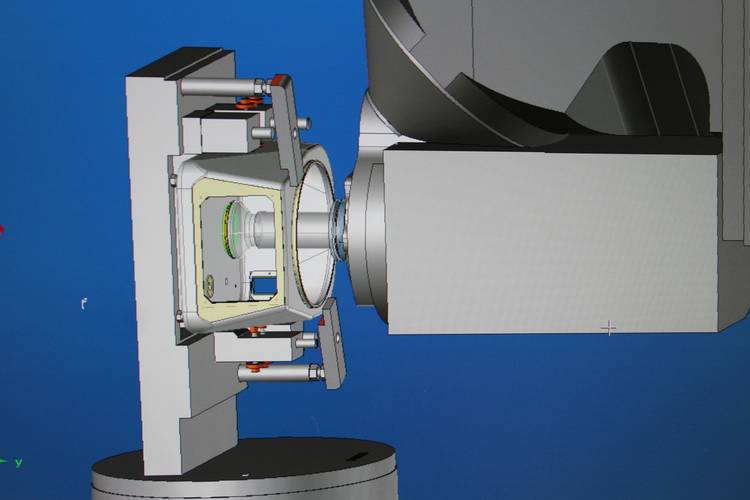
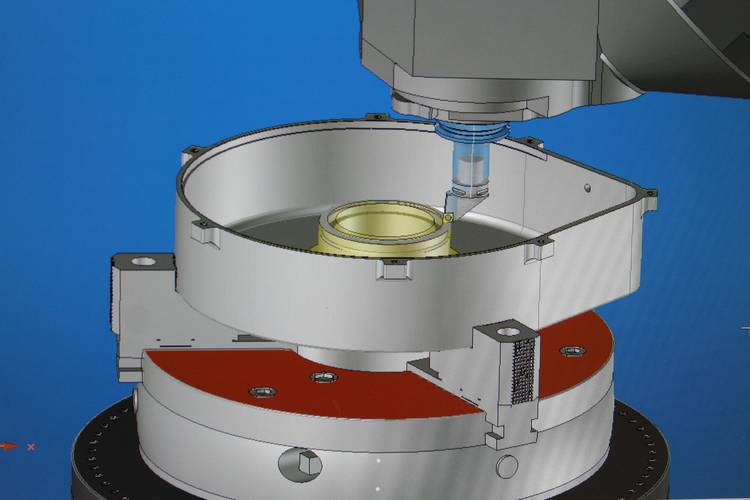
Fondée en 1887 en tant qu'atelier de tissage métallique, la société Haver & Boecker entreprit, dès 1925, de développer des ensacheuses et des tamiseuses pour l'industrie des matières premières. Aujourd'hui, le groupe est l'un des principaux fournisseurs mondiaux de systèmes de conditionnement pour sacs (à valve ou à gueule ouverte) et d'ensacheuses automatiques FFS (Form/Fill/Seal) dans lesquelles sont emballés aussi bien le ciment, les matériaux de construction et les produits minéraux, que les produits chimiques, les matières premières à usage pharmaceutique et les produits destinés à l'industrie agro-alimentaire. L'ensacheuse rotative HAVER-ROTO-PACKER™ mise en service en 1960, qui offre une cadence de remplissage de 6 000 sacs de ciment par heure, est devenue la marque caractéristique de l'entreprise. Haver & Boecker ne se contente pas de fournir des machines autonomes, mais développe, en tant qu'entreprise généraliste, des installations complètes pour la préparation, le conditionnement et le stockage des matières premières.
À l'échelle mondiale, ce sont environ 2 300 salariés qui travaillent pour le groupe, qui a son siège à Oelde et qui, en plus de différentes usines en Allemagne, compte des sites de production en Grande-Bretagne, en Belgique, aux États-Unis, au Canada, au Brésil, en Chine et en Inde. Grâce à un système centralisé de gestion des documents techniques, les salariés des filiales étrangères ont la possibilité d'accéder aux informations et aux documents du référentiel Masterdesign, qui se trouve à Oelde. Il y a deux ans, Haver & Boecker a commencé à développer un concept de plateforme modulaire, afin de faciliter la mise en œuvre de variantes spécifiques aux clients ou aux pays.
Savoir développer des machines et des systèmes parfaitement adaptés aux besoins du client ou du produit à conditionner est l'un des principaux atouts de l'entreprise, mais aussi son plus grand défi, comme l'explique Andreas Bauer, Directeur de production : « La variété d'agents de remplissage que nous traitons ainsi que les différences dans leur comportement d'écoulement sont énormes. Même le ciment n'est pas toujours identique. Nous devons effectuer une analyse macroscopique et microscopique des produits afin de pouvoir offrir aux clients la technique de remplissage idéale pour ses applications. » Haver & Boecker travaille en étroite collaboration avec les fabricants de sacs pour développer des solutions novatrices, par exemple, pour le conditionnement du ciment en sacs plastique stockables en extérieur.
Usinage complet en mode pendulaire
La proportion de valeur ajoutée est relativement élevée chez Haver & Boecker. A. Bauer estime que la part de production propre sur une machine complexe oscille entre 50 et 60 pourcent, même si la découpe au laser des tôles est complètement externalisée et que de nombreux composants électriques, pneumatiques et composants d'automatisme sont achetés. Dans l'usinage par enlèvement de matière, on utilise pratiquement tous les processus (fraisage, perçage, tournage et meulage), même si les opérations de fraisage et de tournage prédominent. Le parc de machines du site d'Oelde comporte, outre le nouveau centre d'usinage à colonne mobile d'AXA, plusieurs centres de fraisage et de tournage de marque Gildemeister et Index, qui fonctionnent généralement en 3x8. Pour les exploiter au mieux, Haver & Boecker fabrique en sous-traitance des arbres de transmission et d'autres composants pour des entreprises locales, ce qui inclut la préparation CAO des pièces à usiner et la programmation FAO.
L'acquisition du centre d'usinage AXA à table longue et à usinage pendulaire s'est faite dans le cadre du remplacement d'une machine verticale d'une vingtaine d'années qui, certes, autorisait le mode pendulaire, mais dont les possibilités ne correspondaient plus aux exigences technologiques actuelles. Pour la fabrication des arbres, il fallait toujours démanteler la séparation, ce qui limitait le mouvement pendulaire et générait des temps d'arrêt. Le choix d'une machine AXA s'est imposé en raison du concept modulaire de la machine et de l'acceptation, côté fabricant, d'adapter celle-ci aux exigences de Haver & Boecker en ce qui concerne l'utilisation de systèmes de serrage à point zéro et les pièces à usiner.
Le nouveau centre d'usinage est dimensionné de telle sorte que vous pouvez, dans la partie gauche, usiner verticalement et frontalement des arbres de quatre mètres de long grâce à la tête pivotante CN, et tourner ou fraiser des pièces de série complexes en mode pendulaire sur la table rotative, dans la partie droite de la machine. Le magasin peut accueillir jusqu'à 150 fraises SK50 et 36 outils de tour ; en outre, il peut être découplé et rechargé alors que la machine fonctionne. « Chez nous, tout est conçu pour minimiser les temps morts », explique Frank Hegemann, responsable Préfabrication. « Désormais, grâce à la nouvelle machine AXA, nous pouvons usiner intégralement des pièces complexes en mode pendulaire, ce qui réduit les temps d'usinage et améliore la qualité. »
Bonne prise en charge des processus de tournage
La minimisation des temps de chargement des outils joue un rôle important dans la fabrication, car il y a beaucoup de pièces différentes à usiner, dans de petites quantités. C'est pourquoi il est nécessaire de disposer de programmes de commande numérique fiables. La société a donc besoin d'un système de FAO, où l'usinage dans l'environnement de la machine, c'est-à-dire tenant compte des conditions de serrage et de l'outil utilisé, peut préalablement être simulé sur l'ordinateur : « Nous devons changer 5 ou 6 fois d'outils par équipe de 8 heures. Et lorsqu'il y a des erreurs de programmation, nous perdons beaucoup de temps », nous explique A. Bauer. « Pour arriver aussi vite que possible à la phase de production, nous voulions reproduire avec exactitude tous les contours et notre système de serrage à point zéro dans le système de FAO. »
Avec l'ancien système de programmation 2D, il était impossible de faire face à ces exigences, c'est pourquoi l'entreprise a décidé il y a trois ans de passer à un système de FAO 3D. Ce qui fut déterminant dans le choix du logiciel TopSolid'Cam, c'est qu'il prenait en charge la programmation de l'ensemble des tâches de fraisage et de tournage. C'est sur ce point qu'ont échoué la plupart des systèmes envisagés, comme nous l'explique le programmeur FAO Wolfgang Frenz. « Nous avons fourni un échantillon à la société Moldtech et avons été très surpris de la rapidité avec laquelle TopSolid a permis de trouver une solution. Même l'importation des données Solid Edge au format STEP a parfaitement fonctionné. »
À cela s'ajoutent de puissantes fonctionnalités CAO au sein du logiciel TopSolid’Cam qui ont fait pencher la balance en faveur du logiciel TopSolid’Cam. Ces fonctions sont, en effet, essentielles pour Haver & Boecker car dans la sous-traitance, les donneurs d'ordre ne fournissent généralement pas de données 3D. Pour pouvoir programmer l'usinage CN, les techniciens doivent d'abord modéliser en 3D les composants à usiner, lors de la phase de préparation. Les pièces en sous-traitance, telles que les arbres de transmission, qui se présentent souvent sous forme analogue, ont été paramétrées avec une rigueur toute particulière, de manière à ce qu'elles puissent être modifiées par l'entrée de quelques cotes. « Si je modifie la géométrie ou le modèle, le programme de commande numérique correspondant est automatiquement ajusté, grâce à l'associativité » : c'est ainsi que W. Frenz nous présente les avantages de la procédure adoptée par Haver & Boecker pour la réalisation en interne de ses gammes de pièces, permettant d’accélérer l'élaboration des programmes CN.
Actuellement, TopSolid’Cam fonctionne sur trois postes de travail chez Haver & Boecker. La société Moldtech a installé le logiciel, programmé les post-processeurs et assisté les utilisateurs pour le raccordement au parc de machines. Les quatre programmeurs FAO de l'entreprise ont été formés durant une semaine dans les locaux de la SSII à Salzkotten, pour se familiariser avec le nouveau système de FAO. En outre, en cas de questions ou de problèmes, ils peuvent à tout moment compter sur l'aide des techniciens de la hotline Moldtech qui, le cas échéant, prendront la main sur leur ordinateur via Netviewer, pour leur montrer comment résoudre le problème. Le support en ligne fonctionne parfaitement, comme le fait remarquer, de manière élogieuse, Monsieur Frenz.
Après quelques jours de formations, les programmeurs FAO étaient en mesure de produire les premiers programmes CN utilisables. « Ce que nous ne pouvons apprendre, bien sûr, que progressivement, c'est à mettre au point une méthode de travail commune. Nous essayons tous de programmer de manière identique, afin que nos collègues puissent facilement modifier nos programmes », explique Wolfgang Frenz, qui n'a pas trouvé le passage à TopSolid’Cam particulièrement difficile : « Bien au contraire. En 2D, lors de l'usinage de pièces complexes, on ne savait jamais exactement où l'on se trouvait dans l'espace et nous n'avions aucun contrôle sur l'enlèvement des copeaux. Le suivi des opérations en multi-tâches constitue une énorme charge de travail en moins par rapport à ce que nous connaissions précédemment. »
Programmation sur machine virtuelle
Contrairement aux autres systèmes de FAO, TopSolid'Cam permet à l'utilisateur de créer ses programmes de commande numérique dans un environnement de machine virtuelle. Étant donné qu'il n'existait pas de modèles 3D pour toutes les machines existantes, les programmeurs FAO ont dû parfois les prendre à l'atelier. Moldtech remodélisait alors les machines en 3D et reproduisait également la cinématique dans les modèles. Le raccordement du nouveau centre d'usinage fut nettement plus simple, car AXA et Moldtech collaboraient, ensemble sur ce point depuis le début. Le fabricant de machines s'est chargé de préparer le modèle 3D, de sorte que Moldtech puisse y reproduire la cinématique de manière optimale. Avant même la livraison de la machine, la SSII a fourni un post-processeur de base au fabricant AXA, afin qu'il puisse vérifier si les opérations de tournage et de fraisage étaient correctement traduites en langage machine.
Le post-processeur a dû encore, naturellement, être adapté aux spécificités de la machine, notamment en ce qui concerne la limitation de l'usinage 5 axes dans la zone de travail située à droite. « En raison de la paroi battante, la tête ne peut pivoter complètement que dans une seule direction, de sorte que l'on doit faire pivoter la table rotative pour usiner la face opposée », a déclaré Monsieur Hegemann, qui s'est montré très satisfait du soutien apporté par ses partenaires : « Nous n'avons encore jamais mis en service une machine aussi complexe en si peu de temps. Quatre semaines après la livraison, nous avons pu débuter la production. »
Pour pouvoir programmer rapidement et simuler fiablement les opérations d'usinage CN, Haver & Boecker a non seulement reproduit les machines, mais aussi les outils et les systèmes de serrage, un à un, dans le système de FAO. Les étaux ont été intégralement paramétrés en fonction du système de serrage à point zéro, pour pouvoir représenter toutes les situations de serrage en ne spécifiant que quelques paramètres. Wolfgang Frenz a défini 10 à 15 modèles avec des opérations de serrage standard pour chaque machine : « Lorsque je fixe la pièce à usiner sur la machine, le système me demande le modèle que je souhaite utiliser ainsi que l'emplacement où la pièce doit être bridée. La mémorisation de toutes ces données a demandé beaucoup de travail, mais économise ensuite énormément de temps lors de la programmation. » L'utilisateur peut programmer ses opérations d'usinage avec TopSolid'Cam, sans programmer l'étape de serrage, par exemple lorsqu'il estime inutile de reproduire la situation de serrage.
Chez Haver & Boecker, on fait désormais une utilisation intensive de la base de données d'outils TopSolid'Tool, qui comprend aujourd'hui quelque 1 500 à 2 000 outils définis paramétriquement. Les programmeurs FAO mettent non seulement à jour les outils dans la base de données, mais gèrent aussi les porte-outils et les rallonges. À partir des différents composants, ils assemblent les outils complets, tels qu'ils doivent l'être pour chaque phase d'usinage. Grâce à des fonctions de filtrage appropriées, ils ne voient, dans le cadre de la programmation NC, que les outils disponibles sur la machine correspondante, dans la mesure où ceux-ci ne sont pas déjà installés en standard. TopSolid’Tool permet également de mémoriser les paramètres de coupe spécifiques aux matériaux, pour les différentes stratégies d'usinage. Si l'opérateur machine modifie quelque peu les réglages en cours d'usinage, il en informe les programmeurs FAO qui actualisent immédiatement le programme de commande numérique. Nous avons ainsi l'assurance qu'en cas de réexécution du programme (par exemple, après une modification de conception), les paramètres de coupe sont toujours d'actualité.
Amélioration de la fiabilité des processus
Grâce à la reproduction méticuleuse des machines, des systèmes de serrage et des outils dans TopSolid'Cam, les temps de programmation ont pu être considérablement réduits chez Haver & Boecker. « Selon la complexité de la pièce, nous avons gagné près de 50 pourcent en matière de rapidité », nous confie W. Frenz. Autre point, et non des moindres, c’est que la fiabilité des processus s'est considérablement améliorée, grâce à la possibilité de visualiser et de simuler les opérations d'usinage sur l'ordinateur, ce qui permet de roder plus rapidement les nouveaux programmes CN. Les opérateurs machine peuvent encore modifier, ici et là, la vitesse ou l'avancement au cours de l'usinage, mais les trajectoires outil calculées sont exactes. À l'aide de la feuille d'ajustement, ils peuvent savoir s'il s'agit d'une pièce usinée pour la première fois sur la machine et si l'état des modifications du programme CN correspond à celui du tracé.
Selon A. Bauer, il est possible d'économiser encore plus de temps en parvenant à homogénéiser au mieux la conception des composants en cours et des nouveaux composants, de sorte qu'ils puissent être usinés avec un minimum d'outils spéciaux. Il voit aussi des possibilités d'amélioration dans la production : « Notre entreprise dispose d'une technologie 5 axes performante, d'un système de FAO optimal ainsi que d'une très bonne base de données. Il s'agit à présent de continuer à améliorer l'environnement de la machine et les processus logistiques. Une première étape en ce sens a été la création d'une nouvelle zone de réglage, où peuvent être préparés de manière centralisée les outils, les capteurs de mesure et les dispositifs pour la prochaine étape, l'objectif étant d'avoir sur chaque machine un « tampon d'ordres visualisable », afin que les outils puissent être rapidement changés en un délai d'attente et de préparation minimum. »
Besoin de plus d'informations
UNE QUESTION SUR NOS
PRODUITS OU SOLUTIONS ?
Trouvez le point de vente le plus proche Contactez-nous Demandez un devis