14 septembre 2010
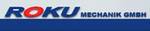
Des temps d'usinage plus courts avec TopSolid’Cam.
Pour ROKU Mechanik GmbH, qui est un spécialiste de l'usinage complet pour des « pièces A » (des pièces classées de très haute qualité), des temps machine courts sont plus importants que des temps de programmation réduits. Avec TopSolid, l'entreprise simule et optimise non seulement les parcours d'outils mais également les durées d'usinage. Le patron de ROKU, Roland Kuhnhaus, compte bien réduire les frais globaux d'au moins 50 % grâce à la mise en œuvre du logiciel TopSolid.
ROKU Mechanik GmbH, basée à Unterschneidheim, est une entreprise de production classique qui assure l'usinage complet de composants complexes munis de n'importe quel revêtement courant, tout en offrant également une assistance logistique aux clients : "Nous livrons les pièces prêtes à monter directement au poste de montage du client ; souvent, il s'agit de jeux de pièces complets réunissant entre 200 et 300 éléments, le tout étant mis à disposition dans des conteneurs KANBAN," comme l'explique Roland Kuhnhaus, le directeur de la société. Dans ce cas, l'entreprise coordonne également l'approvisionnement de pièces de catalogue et la production d'éléments plus simples réalisés par découpage à la presse ou au laser qu'on ferait normalement sous-traiter.
ROKU est un spécialiste de composants appelés "pièces A", destinées à la construction de véhicules, aux motorisations, à l'industrie aérospatiale, aux équipements médicaux et à l'industrie optique, avec des tailles de lots de production variables, soit entre une et 10 000 pièces par an. La société emploie actuellement environ 140 salariés. Parmi ses prestations figurent par exemple l'usinage d'un carter d'arbre de différentiel destiné aux moteurs d'un grand groupe automobile allemand, et le fraisage des boîtiers en aluminium de caméras professionnelles et microscopes d'opération pour le compte d'un fabricant d'équipements optiques allemand. Une partie de ces produits sont des composants de sécurité à livrer directement sur la chaîne – on comprend alors les exigences élevées en matière de qualité et de fiabilité des processus auxquelles ROKU doit se conformer.
Afin de garantir une transition dans la continuité entre productions prototypes et série, ROKU a adopté le principe de production des pièces prototypes sur machines de série - y compris l'ensemble des moyens de production et de serrage, qui sont fabriqués dans l'entreprise même. "Nous devons être capables de lancer la production série dans un délai court, y compris pour des pièces à haute complexité," résume Kuhnhaus quant à l'un des défis auxquels l'entreprise est confrontée. "Pour cette raison, nous lançons désormais la production des pièces en parallèle avec le développement, au risque de rebuter ces pièces dans le pire des cas s'il y a des problèmes. De nos jours, les clients prennent ce risque en connaissance de cause afin d'accélérer la mise sur le marché."
Durant ces dernières années, ROKU a fortement uniformisé son équipement en machines, et les nombreux tours à fraiser et à tourner ont été remplacés par des centres d'usinage hautement complexes avec jusqu'à huit axes, qui usinent quasiment n'importe quelle matière usinable : acier, titane, aluminium, pièces de fonderie et de forge, ainsi que des matières plastiques. De même, au lieu de la multitude d'automates d'autrefois, seules les commandes Fanuc et Okuma sont utilisées maintenant. Cette uniformisation est garante de la souplesse en matière d'ordonnancement ; en effet, les programmes de CNC et les outillages s'adaptent ainsi à quasiment toutes les machines. Néanmoins, des outils puissants de CFAO sont nécessaires si on veut pleinement exploiter les potentiels des machines. "Lorsqu'un usinage ne peut pas être simulé et visualisé sur ordinateur, la complexité croissante des pièces fait qu'on subit des temps morts machine pour la mise en route et le changement de production tels que personne ne peut plus se les permettre," relève Roland Kuhnhaus.
Des atouts pour le tournage
Confrontée à une complexité qui ne cesse pas d’augmenter des machines et des composants à usiner, ROKU a pris la décision fin 2005 de se doter d'un système de CFAO en 3D. Ses collaborateurs du bureau de préparation programmaient certes déjà leurs machines hors ligne, mais en se basant sur un éditeur 2D classique et les plans production. Or, avec cette manière de faire, ils ne pouvaient ni calculer la géométrie de l'ébauche ou l'épaisseur de l'enlèvement, ni détecter les conflits d'arêtes. La prise en compte des collisions revêt une importance particulière pour ROKU puisque de nombreux composants sont tellement complexes que leur fixation exige des outillages spécifiques ; ce sont ces outillages qui risquent ensuite de générer des collisions avec l'outil ou le porte-outil.
Lors de la sélection du futur système, plusieurs solutions de CFAO ont été évaluées, dont les capacités en matière de programmation du fraisage valaient tout à fait celles de TopSolid. Le critère qui a finalement départagé les logiciels en faveur de Missler Software était la bonne assistance aux usinages complexes par tournage et fraisage, comme l'indique Andreas Hammele, le responsable de la programmation CNC : "Sur des machines multi-axes à double broche, la gestion synchrone des différentes opérations devient impossible à calculer de tête. Nous étions donc à la recherche d'une solution permettant de simuler la synchronisation de l'usinage sur ordinateur, ceci pour éviter de nous rendre compte seulement au stade pratique sur la machine que la gestion de cette répartition ne fonctionne pas, et donc, d'avoir à recommencer à trier les outils. D'autre part, il nous fallait un module de CAO puissant pour l'étude de nos outillages."
Actuellement, la solution CFAO intégrée de Missler Software tourne à Unterschneidheim sur un total de six postes de PC sous le système d'exploitation Windows XP. Trois d'entre eux sont équipés du logiciel TopSolid’Design, du module TopSolid’Cam pour la programmation de fraisages 3 axes et du module de tournage TopSolid’Cam, tandis que trois autres n'utilisent que le logiciel de CAO. Ces derniers servent essentiellement aux conceptions des moyens de production, selon Hammele : "Les pièces de géométrie complexe sont généralement impossibles à usiner sur des serrages standard. C'est ce qui nous oblige souvent à concevoir des fixations et des dispositifs de manipulation spéciaux, en particulier pour le secteur automobile."
Cependant, ROKU a encore besoin de fonctionnalités puissantes en CAO dans d'autres domaines que la seule construction d'outillages et de moyens de production. Les spécialistes de la production doivent en effet de plus en plus souvent assister leurs clients dès le stade de développement de produits pour faire des propositions en vue d'une fabrication moins chère des pièces, ou encore, d'une réduction du poids des pièces sans alourdissement des opérations de production. "Souvent, le concepteur du produit ne sait pas après tout comment nous allons usiner, et surtout fixer, sa pièce. Le coût d'un système de serrage complexe pourra être largement réduit si on nous donne l'occasion d'intervenir sur la fixation de la pièce," analyse Kuhnhaus.
Un support avec des clips vidéos très parlants
La nouvelle solution de CFAO a été déployée il y a un peu moins de deux ans par le distributeur local de Missler Software, AdeQuate Solutions basé à Lahr, qui a également formé les utilisateurs et les assiste désormais activement en cas de souci. Les utilisateurs se montrent très satisfaits du support, comme le souligne Hammele. Ils reçoivent une réponse à leur demande de support sous 24 heures, et ce souvent sous forme de clips vidéo pour illustrer la procédure à suivre. ROKU profite également de la télémaintenance proposée par la SSII à ses clients.
Les formations de base aux fonctions de CAO et FAO durent chacune de deux à trois jours. Ensuite, on laisse environ quatre à six semaines aux utilisateurs pour assimiler les acquis avant de retourner pendant plusieurs jours en formation pour utilisateurs plus expérimentés. Il leur a fallu environ huit semaines jusqu'à ce qu'ils soient suffisamment familiarisés avec le système de CAO pour le maîtriser. La phase d'adaptation aux fonctionnalités de FAO a été légèrement plus longue car les programmeurs ont dû apprendre également à saisir leurs outils sous TopSolid.
La visualisation des outils, machines et fixations fait partie des conditions essentielles pour qu'un usinage puisse être simulé en FAO au plus près des réalités. Chez ROKU, on ne crée actuellement plus aucun nouveau programme de fraisage ni de tournage sans créer en même temps les outils requis. En même temps on saisit l'ensemble des paramètres de coupe, ce qui permet de calculer les temps d'usinage pour chaque opération avec une précision très correcte. Il a également fallu que les utilisateurs modélisent d'abord les machines sous TopSolid ; les salariés d'AdeQuate Solutions ont quant à eux été chargés de rendre les cinématiques dans ces modèles. Ils ont d'autre part adapté les post-processeurs aux centres d'usinage Makino et Okuma, dont ROKU utilise un assez grand nombre.
Simulation des étapes d'usinage
Lorsqu'ils existent, les fichiers de données 3D des pièces à usiner sont fournis par les clients à ROKU, le plus souvent sous un format de fichier neutre tel que STEP ou IGES. Les utilisateurs importent ces fichiers dans TopSolid, mais il faut encore souvent intervenir pour les adapter. "Le problème est que notre principe en fabrication et également en programmation est basé sur la tolérance médiane, alors que tous les clients ne conçoivent pas suivant la même approche. On est donc régulièrement obligés d'adapter les données après conversion," explique Hammele. Pour les clients dont les études ne sont pas encore en 3D ou impossibles à exporter sous format STEP, les collaborateurs doivent tout d'abord créer un modèle du produit en 3D à partir des plans en 2D. Ensuite ils définissent la géométrie du brut, qui fournit en même temps la base pour construire des outillages et moyens de production. Les modèles des fixations en 3D peuvent être directement utilisés dans la simulation des programmes d'usinage.
En partant de la géométrie de l'ébauche et du composant final, on peut définir l'enlèvement de copeaux. Le programmeur de FAO décide comment et avec quels outils aura lieu le vidage tandis que le système émet des propositions de stratégie d'usinage. Après chaque étape d'usinage, la géométrie de la pièce brute peut être actualisée, de sorte que l'utilisateur puisse saisir d'un seul coup d'œil les endroits où il reste encore du matériau en surépaisseur. Le logiciel offre la possibilité de définir des cycles d'usinage réutilisables pour des éléments de géométrie fréquemment rencontrés. Cependant, selon Andreas Hammele, de tels automatismes n'ont qu'une importance mineure pour ROKU. "Chez nous, ce qui compte, c'est clairement l'optimisation des temps machine. Il nous faut regarder comment arriver à réaliser les temps d'usinage estimés, et pour y arriver, nous sommes prêts à investir davantage dans la programmation."
L'optimisation des temps machine constitue un processus interactif. À partir de la simulation de l'enlèvement de copeau, l'utilisateur détecte quelles sont les opérations particulièrement gourmandes en temps, ce qui lui permet d'intervenir et d'améliorer – par exemple, en sélectionnant une stratégie d'usinage différente, ou encore, en dégrossissant telle géométrie avec un outil de grande taille et en confiant la finition à un outil plus petit. D'après Hammele, les fonctions de simulation font partie des atouts fondamentaux de TopSolid puisqu'elles donnent une vision relativement précise de la durée de chaque opération, permettant ainsi de les répartir au mieux entre les différents axes et broches.
Réduction des temps d'usinage
Étant donné que la simulation est fiable pour détecter les surépaisseurs résiduelles et d'éventuelles collisions, les opérateurs qui mettent en route les programmes sur machine sont libres de se concentrer sur des aspects que l'ordinateur ne simule pas du tout, ou seulement au prix d'opérations trop lourdes. Citons l'exemple des conséquences de certaines forces physiques ou le comportement d'un matériau à haute performance particulier : "L'opérateur spécialisé sur la machine restera toujours celui qui gagne les quelques derniers pour cent," selon la conviction de Kuhnhaus. "Même avec un seul et même matériau, les conditions ne sont jamais identiques. Une matière de coupe qui marche bien sur telle pièce va subitement poser problème sur un composant avec une géométrie différente. Pour cette raison, les retours de l'expérience des opérateurs doivent constamment être réintégrés dans l'usinage. »
Du fait de la meilleure qualité des programmes de CNC, ROKU a pu nettement réduire les temps de mise en route. Sur la machine, on observe moins de défauts susceptibles de générer des frais inutiles. Par ailleurs, il est à noter que les temps d'usinage sur machine ont été raccourcis par l'optimisation des programmes CNC, bien que les gains propres à cet aspect soient difficiles à quantifier. Cela est d'autant plus vrai que la phase de lancement du système n'est pas encore arrivée à son terme ultime. "Néanmoins, je pars du principe qu'à terme, lorsque tout sera en place, que toutes les machines auront été modélisées et que tous les post-processeurs seront adaptés, la réduction du travail de programmation pourra atteindre les 50 % plus x, avec un x d'autant plus élevé que le composant à usiner sera complexe,“ assure le chef de l'entreprise, Roland Kuhnhaus. ROKU anticipe même un potentiel d'économies supplémentaires par l'introduction d'une gestion des données de production, qui permettra une administration plus efficace des nombreux outillages et moyens de production.
Besoin de plus d'informations
UNE QUESTION SUR NOS
PRODUITS OU SOLUTIONS ?
Trouvez le point de vente le plus proche Contactez-nous Demandez un devis