4 avril 2012
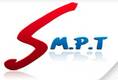
Pièces complexes, petites séries, temps d'usinage long, exigence qualité élevée, forte réactivité, telles sont les contraintes auxquelles l'entreprise SMPT doit faire face pour assurer sa pérennité. Faire mieux et plus vite reste la clé, pas seulement lors de l'usinage, mais également lors de la programmation des machines.
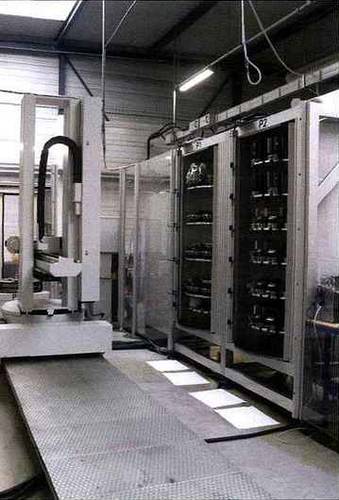
Créée en 1980 à Tierce près d’Angers l’entreprise réalisait à l’origine 90% de son activité dans l’usinage de matériaux plastiques techniques. Un positionnement qui a beaucoup évolué puisque qu'aujourd’hui elle consacre la même proportion de son activité à produire des pièces en alliage d’aluminium, mais toujours par usinage. Ce sont en fait des choix stratégiques qui ont conduit I’entreprise à acquérir de nouvelles compétences dans le travail des alliages légers, même si Michel Talland actuel président de I’entreprise, reconnaît que « ceux qui sont restés dans le domaine de I’usinage des plastiques techniques ont des marchés moins difficiles que les nôtres où la concurrence est devenue très rude avec une concurrence étrangère très forte ».
Un outil de production exemplaire
Le cœur de métier de SMPT est aujourd’hui l’usinage de boîtiers électroniques taillés dans la masse pour des applications aéronautiques et spatiales civil ou militaire. Des pièces complexes qu’il fournit directement à des clients comme Thales, Safran ou encore Zodiac mais également à des intégrateurs comme Tronico ou Eolane produisant des systèmes pour ces mêmes Groupes. Or, pour se maintenir dans la course sur de tels secteurs, il faut être à la pointe de la technique en usinage, mais également faire preuve d’attractivité en termes de prix. Une équation pas toujours facile à résoudre. Une des pistes choisie par I’entreprise, c’est l’investissement dans des moyens de productions performants et un coup d’œil jeté au part machine de l’entreprise suffit à s’en convaincre. Il ne contient pas moins de 4 centres d’usinage 5 axes DMG-Mori sur les 15 que compte l’entreprise au total, sans parler des deux centres de tournage bi-broche/bi-tourelle qui caracole en tête du parc de tournage. Cette liste de machines n’est pourtant que partiellement représentative des efforts que fait I’entreprise en termes d’investissement. « Il y a deux ans nous avons investi dans une cellule d’usinage automatisée », explique Michel Talland. De marque Erowa, cette installation assure I’alimentation de quatre centres d’usinage de manière autonome. Les pièces à usiner sont chargées dans un magasin de 166 palettes. Les machines préalablement préparées sont ensuite approvisionnées à partir de ce magasin au fur et à mesure des besoins des machines. Une installation remarquable qui a coûté autour de 2 millions d’euros. « C'est un investissement lourd pou une entreprise de notre taille, mais sans lequel nous serions en grande difficulté aujourd’hui », explique Michel Talland.
Le meilleur programme, le moins cher possible
ll y a plusieurs raisons à cela. La première, c’est quelle représente une vitrine à laquelle ses clients sont sensibles car elle en dit long sur le niveau technologique de ce partenaire. Ensuite, en tournant 7j/7, elle permet à SMPT de se placer en termes de prix, même par rapport a certains de ses concurrents hors frontières qui ne sont pas les plus faciles à battre sur ce terrain. C’est également cette quête permanente de performances qui est à I’origine de I’adoption des solutions de Missler Software au sein du bureau de programmation. Cet aspect de la prestation est en effet devenu des plus stratégiques avec le temps. ll est en effet indispensable de réaliser le programme le plus optimisé tout en y consacrant le moins de temps possible. « Le coût de programmation d’une pièce est loin d’être négligeable aujourd’hui », explique Michel Talland, « et la charge de travail générée par ce poste est de 5 personnes à plein temps » Une charge de travail qui pèse sur les marges comme l'explique Michel Talland « la programmation n’est plus totalement à la charge du client ». L'entreprise en assume une grande part en espérant que les séries soient récurrentes pour que cet investissement ne soit pas fait en pure perte
Par ailleurs, au-delà du nombre de programmes à réaliser il y a I’obligation de reprendre complètement la définition numérique fournie par le client. « C’est le plan qui fait foi, nous explique un préparateur, il est donc indispensable de mettre la CAO à plat pour que la définition de pièce que nous utilisons pour la programmation soit la définition exacte en cote moyenne de la pièce ». C'est pour cette raison que l'usage de TopSolid représente un avantage au regard d une solution de FAO classique « Le point fort de TopSolid, c’est I’associativité entre la CAO, la mise en plan et la FAO », explique un autre préparateur. Un point de vue que confirme un de ses collègues : « nous disposons maintenant d’une chaîne numérique non interrompue entre la définition de la pièce, les programmes et les montages d’usinage associés de sorte qu’une modification de la pièce se répercute en cascade automatiquement Avec les autres solutions, il faut manuellement reprendre toutes les définitions d’outillages et les programmes »
Une vision réaliste de l'usinage
Autre aspect qui explique la réduction de 30% réalisée sur les temps de programmation chez SMPT, c'est la simulation. « Le fait de disposer de I’environnement machine lors de la simulation d’usinage permet d’éviter tout risque de collision et d’optimiser les trajectoires sans les marges de sécurité que nous nous imposions avant ». Point qui devrait encore s'améliorer avec l'intégration des solutions de Spring Technologies au sein de TopSolid, tout comme la gestion des outils qui présente quelques lourdeurs dans la version actuelle, mais que l'éditeur a planifie d'optimiser grâce à ce nouveau partenariat commercial ».
Besoin de plus d'informations
UNE QUESTION SUR NOS
PRODUITS OU SOLUTIONS ?
Trouvez le point de vente le plus proche Contactez-nous Demandez un devis