24 juillet 2012
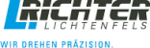
Si tous les amateurs de VTT connaissent bien le moyeu Rohloff 14 vitesses intégrées, en revanche, il est peu probable que le nom L. Richter leur évoque quelque chose. Située à Lichtenfels, dans le land de la Hesse, cette entreprise fabrique des pièces complexes en aluminium destinées aux dérailleurs qui répondent aux normes de qualité et de précision les plus exigeantes. Pour les centres d’usinage modernes, le logiciel de FAO TopSolid’Cam permet de programmer le tournage et le fraisage, afin de réduire sensiblement les temps de mise en route.
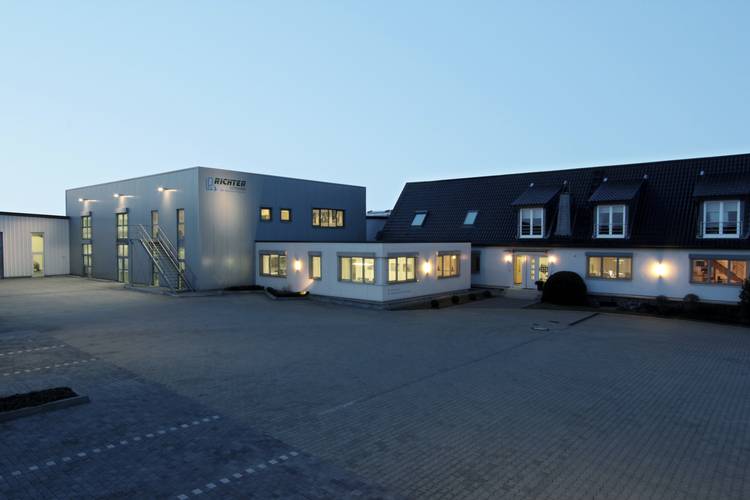
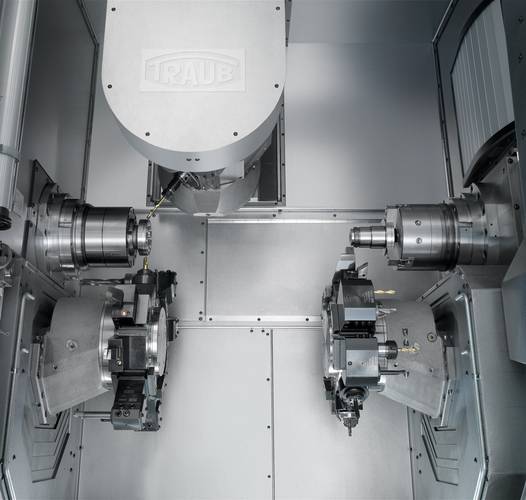
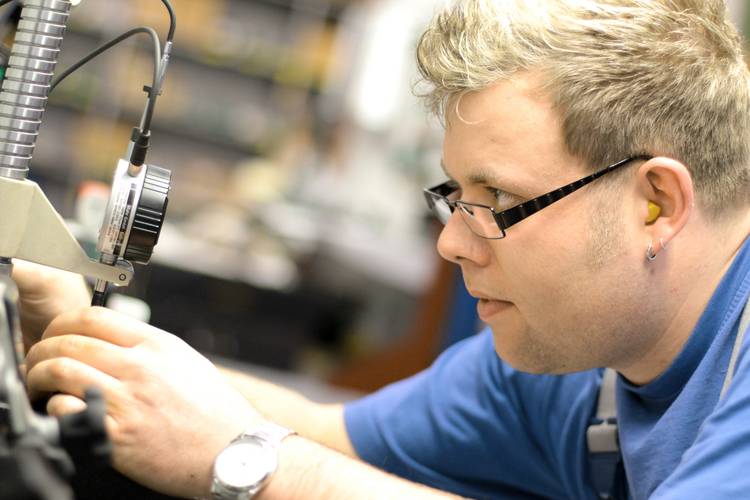
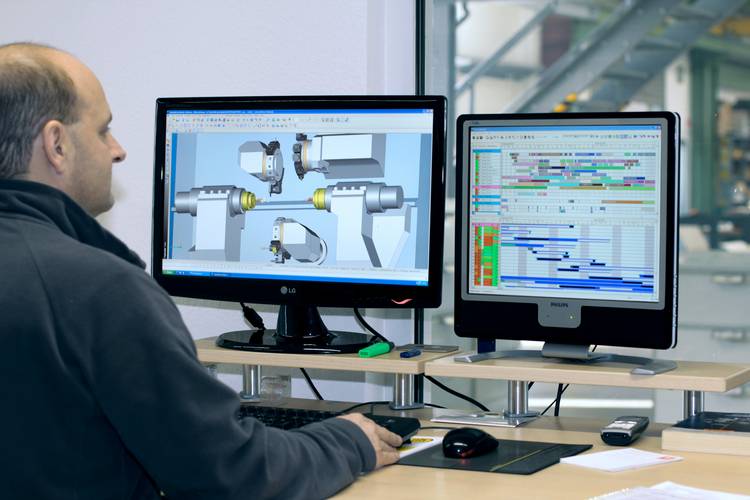
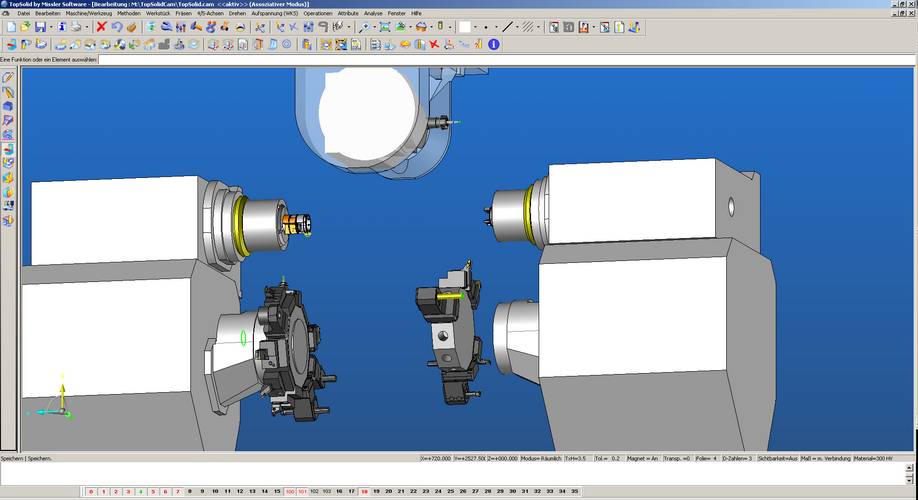
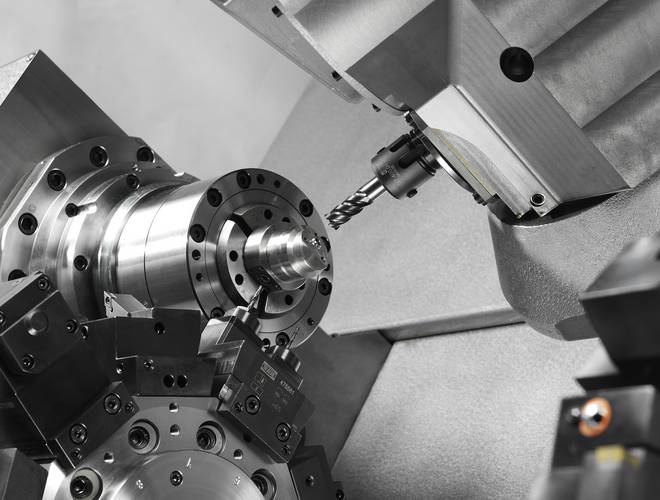
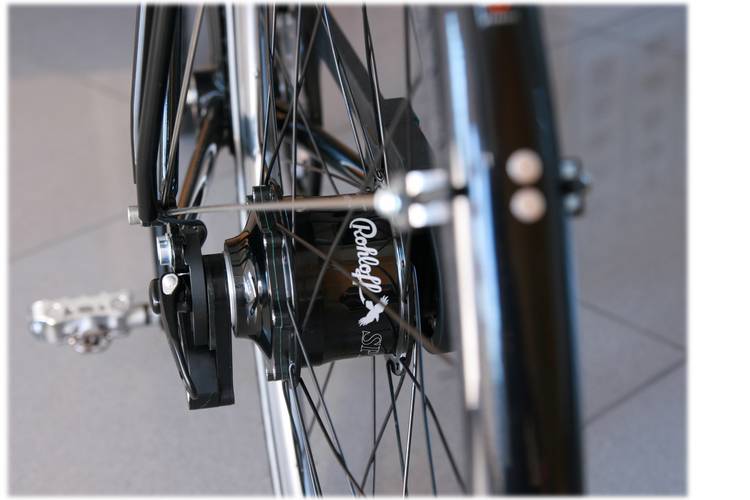
L. Richter KG fait partie de ces entreprises qui prouvent qu’en se spécialisant, même une petite usine de production allemande peut se montrer concurrentielle. Fondée il y a près de 50 ans en tant qu’atelier de tournage à façon classique, L. Richter KG produisait à l’époque de grandes quantités de pièces simples en laiton. Grâce à l’installation de machines à commande numérique et de techniques de programmation FAO modernes, la petite entreprise familiale, qui compte aujourd’hui 25 salariés, est devenue un partenaire de renommée pour la production de pièces de précision complexes, conçues dans des matériaux exigeants. Outre les aciers inoxydables, Richter travaille principalement l’aluminium, mais aussi les matières plastiques.
Pour les spécialistes du site de Lichtenfels, les pièces complexes correspondent à des pièces tournées exigeant un travail important de fraisage. Leur complexité se traduit directement par les temps d’usinage nécessaires. Le nouveau centre de tournage-fraisage Traub TNX65/42, doté d’une broche principale et d’une contre-broche, de deux tourelles porte-outils, d’une broche de fraisage pivotante et d’un magasin de chaîne, permet désormais d'usiner entièrement une pièce en acier inoxydable. Bien que les quelques 50 outils de tournage et de fraisage interviennent à certains moments simultanément ou de manière entrecroisée sur les deux broches, l’usinage dure au total 24 minutes. « En temps normal, l’usinage d’une pièce tournée nous prend deux à trois minutes », explique Matthias Richter, directeur appartenant à la deuxième génération de dirigeants de l'entreprise.
Des pièces d’une qualité constante
Richter travaille pour des clients issus de branches différentes qui souvent ne disposent pas d’atelier de fabrication de pièces. Pour bon nombre d’entre eux, Richter est même l’unique fournisseur de pièces spécifiques. « La fiabilité et la qualité sont deux points que nos clients apprécient dans notre travail », déclare M. Richter. « Notre force réside dans l’association de pièces complexes et de matériaux, le respect des délais et la qualité constante. Concernant les interfaces, nous définissons des critères souvent plus rigoureux que ceux imposés par le client. » Une précision visible et mesurable : pour contrôler le respect des dimensions des pièces, la société a développé son propre processus d’assurance qualité assisté par ordinateur. Il garantit ainsi des retours produits quasi nuls.
Aux côtés de la qualification des employés, l'intégration de nouvelles technologies joue un rôle prépondérant dans le succès de l’entreprise. Le père de M. Richter a investi dans la première machine (une Traub) en 1979, afin de pouvoir travailler des pièces et des matériaux plus complexes. Depuis 1989, toutes les machines sont programmées hors ligne afin de limiter la durée des arrêts de service. « Pour une entreprise de notre taille, l’acquisition du premier système de programmation Index, qui s’exécutait à l’époque sur des ordinateurs VAX, représentait un investissement énorme », se souvient le directeur, lui-même programmeur. Il y a trois ans, l’entreprise a remplacé sa solution 2D½ par le système de CAO/FAO 3D TopSolid’Cam, afin d’exploiter au maximum le potentiel des machines multiaxe et de réduire les temps de mise en route. Cette nouvelle solution de CAO/FAO est aujourd’hui installée sur trois postes de travail.
La réduction des temps de mise en route est un critère primordial pour la société. Cela lui permet en effet de répondre rapidement aux demandes des clients et de fabriquer des pièces dans des quantités moindres de manière encore plus économique. « Sur les machines les plus complexes, nous fabriquons des quantités comprises entre 250 et 5 000 pièces maximum par lot, et sur les machines moins complexes, nous produisons également des quantités inférieures », explique M. Richter. « Chez nous, rares sont les machines qui s’exécutent sur une même commande pendant plus de dix jours d’affilée. En général, elles sont reconfigurées tous les jours, et parfois même plusieurs fois par jour. »
Avantages de la nouvelle machine Traub
En plus du nouveau centre de tournage-fraisage Traub TXN65/42, le parc de machines de la société se compose de centres de tournage productifs de type Index C100, qui sont dotés de trois tourelles porte-outils destinées à la fabrication d’importantes quantités de pièces, ainsi que plusieurs centres d’usinage 4 axes de type Index G200, dotés chacun de deux broches et tourelles équipées d’outils à entraînement pour le tournage-fraisage combiné. En outre, le parc est équipé de centres de tournage plus simples pour l’usinage de pièces moins complexes. Les opérateurs Richter sont formés de manière à savoir utiliser chaque machine, et ce bien que la machine Traub, contrairement aux machines Index, soit équipée d’un système de commande TNX ou Mitsubishi, et non d’une commande Siemens.
L’acquisition du nouveau centre d’usinage a engendré des frais supplémentaires associés à la broche de fraisage qui se sont finalement avérés rentables en tout point de vue. Grâce à ce nouveau centre, l’entreprise peut assurer l’usinage complet de pièces tournées dont le fraisage est particulièrement exigeant et complexe. « La diversité des pièces proposées nous permet d’entrer dans une nouvelle dimension et de nous distinguer toujours plus de la concurrence », déclare M. Richter. « Peu de prestataires disposent de cette machine. »
Richter exploitait aussi les machines Index pour l’usinage complet des pièces ; cependant, les opérateurs étaient de plus en plus confrontés aux limites des outils à entraînement des tourelles (fixes), notamment lors de l’usinage d’alésages et de filetages obliques, ou bien parce que les tourelles ne pouvaient pas accueillir suffisamment d’outils. « De plus, les outils à entraînement sont nettement plus chers que les porte-outils HSK standard ; ils ont un taux d’usure plus élevé, sont plus difficiles à mettre en place et n’offrent pas la même vitesse de rotation », poursuit M. Richter. « Concernant les pièces tournées, nous sommes plus efficaces sur la machine Traub, tant au niveau de la mise en place que de l’usinage. Cela nous permet de compenser les taux horaires élevés des machines. »
Trouver le bon partenaire
Toutes les machines sont reliées à TopSolid’Cam via des post-processeurs performants et sont fournies avec le code NC à partir de la nouvelle application de CAO, à l’exception de quelques opérations. Chargée des raccordements du parc de machines, la société AdeQuate Solutions, revendeur TopSolid en Allemagne, s’est notamment occupée de la programmation des post-processeurs, de la création des maquettes 3D destinées à la simulation ou encore de la représentation de la cinématique des maquettes (si fournie par le fabricant). Afin de réduire au minimum les dépenses liées à l’entretien du logiciel, Richter a renoncé au réglage personnalisé des post-processeurs, à l’exception de quelques cycles d’usinage qui n’étaient pas compris dans la version par défaut.
La programmation des post-processeurs pour le centre de tournage-fraisage Traub était une première pour la société AdeQuate Solutions. C’est pourquoi les programmeurs ont dû prendre en compte certaines particularités de la commande TNX, par exemple le fait que la correction du rayon de coupe est calculée à l’envers sur la contre-broche, ce qui a au début créé des problèmes au niveau des contours. Le principal défi consistait surtout à reproduire les nombreuses options d’usinage. Par exemple, la broche de fraisage a une capacité de rotation à 180° et peut également tourner autour de son propre axe et se bloquer, afin d'installer un burin supplémentaire pour le tournage à l’aide de deux outils en quinconce. Autrement, il est également possible de soutenir les longues pièces tournées à l’aide d’une poupée mobile placée dans la tourelle de la contre-broche.
« En tant que fournisseur, cette machine est optimale par sa polyvalence ; il est cependant nécessaire que les post-processeurs prennent en charge cette polyvalence », explique M. Richter qui, à ce sujet, attribue tout le mérite à la société de services informatiques basée à Lahr tout en louant ses compétences et sa qualité de service : « Tous les post-processeurs étaient en état de marche ce qui nous a permis de les programmer immédiatement. Si une opération n’est pas prise en charge de manière optimale, nous recevons dans un délai de 24 heures un post-processeur mis à jour. Nous n’avons vraiment rien à reprocher au service de la société AdeQuate Solutions. »
Le système TopSolid : un choix mûrement réfléchi
Sans la société de services informatiques AdeQuate Solutins, l’entreprise aurait certainement opté pour une autre solution de FAO. Lors du choix du système, le logiciel TopSolid avait été présenté par un autre fournisseur mais n’avait pas été sélectionnée en premier lieu. Bien que TopSolid’Cam offre la meilleure prise en charge du tournage et du fraisage parmi tous les systèmes envisagés, il avait paru trop compliqué aux utilisateurs lors de la présentation du système. Sur les conseils d’une connaissance, la société est entrée en contact avec AdeQuate Solutions. « Au départ, nous avions surestimé les dépenses liées à la modélisation 3D. Nous étions perplexes lorsqu'un collaborateur d’AdeQuate Solutions nous a démontré, à partir d’une pièce complexe, à quel point il est facile de créer une maquette à partir d’un dessin 2D et de programmer les étapes d’usinage », explique Richter. « Nous avions non seulement besoin du bon système, mais également du bon partenaire. »
Comme le souligne Matthias Richter, les fonctions de CAO intégrées comptent parmi les principaux atouts de TopSolid’Cam. Elles sont particulièrement importantes pour les programmeurs dans la mesure où ils ne reçoivent pas des données 3D de la part de tous leurs donneurs d’ordres et doivent d’abord modéliser les pièces avant de pouvoir lancer la programmation. Et même lorsqu'ils reçoivent des données 3D, il est souvent nécessaire d’ajuster la géométrie étant donné que les constructeurs des clients créent généralement des maquettes en cote nominale sans se préoccuper des tolérances de fabrication. Bien que TopSolid prennent facilement en charge ce type d’ajustements, il est parfois plus efficace de reconcevoir entièrement la maquette afin de profiter des avantages de l’associativité entre la modélisation CAO et FAO. « Il est plus facile de mettre à jour les programmes de FAO en cas de modification de la géométrie », explique M. Richter.
Même si l’utilisateur doit d’abord créer une maquette 3D, un processus qui a gagné en rapidité grâce au savoir-faire acquis au cours de ces deux dernières années, il gagne ensuite du temps lors de la programmation des opérations de tournage et de fraisage. Ensuite, il ne reste plus qu’à cliquer sur les surfaces à usiner, à sélectionner l’outil et à définir les paramètres de coupe. Auparavant, les opérateurs devaient en partie transférer les cotes et les points de coupe manuellement à partir du dessin de CAO, ce qui constituait une opération relativement fastidieuse. Le processus de modifications est désormais plus rapide car il n’est plus nécessaire de recréer tout ou partie du programme de FAO ; il suffit simplement de relancer le calcul. « Si les données 3D du client ne sont pas claires, aujourd'hui nous n'hésitons pas longtemps, nous refaisons tout simplement les dessins », déclare Richter. Parfois, les spécialistes de la fabrication mettent leurs données de modélisation à la disposition de leurs clients qui ne possèdent pas encore de système 3D.
Optimisation de l’usinage multiaxe
Pour M. Richter, la chaîne de processus CAO/FAO comprend également d’immenses avantages en matière d'assurance qualité. Les cotes et les tolérances définies dans la maquette ou le dessin peuvent ensuite être transférées au logiciel de gestion de la qualité développée par Richter, au format DXF, et être utilisées pour la création automatique de plans de test. Chaque pièce est testée et documentée à 100 % par Richter avant la validation de la série. Les fabricants sont responsables de la qualité de leurs pièces et vérifient aléatoirement les cotes importantes de la série en cours. « Nous programmons l’usinage en partie en fonction de la géométrie à tester et garantissons ainsi une sécurité élevée du processus », souligne M. Richter.
Les programmeurs utilisent également les fonctions de CAO pour intégrer tous les outils, les porte-outils et les systèmes de serrage dans TopSolid’Tool. Comme l’explique Matthias Richter, il a fallu travailler dur au début, mais aujourd’hui, cela se révèle payant. Grâce à la reproduction complète de l’environnement des machines, les utilisateurs peuvent simuler et optimiser leur programme de FAO en toute sécurité sur leur ordinateur. La nouvelle solution de FAO permet entre autres de calculer la durée d’exploitation des machines et de la réduire au minimum en déterminant les étapes d’usinage au niveau de la broche principale et de la contre-broche, à l'aide d'un diagramme prévisionnel. Dans le passé, les programmeurs devaient prévoir tout cela mentalement, pour parfois s’apercevoir seulement à l’exécution initiale du programme que le processus ne fonctionnait pas comme ils l’avaient imaginé.
Grâce à la simulation et à la visualisation de l’usinage FAO, Richter équipe aujourd’hui ses machines nettement plus rapidement. Cela tient principalement au fait que les programmes exécutés sur les machines sont technologiquement irréprochables et fonctionnent correctement. Auparavant, les opérateurs rencontraient de nombreuses difficultés de réglage qu’ils ne pouvaient résoudre qu’au moment de l’exécution initiale. Il était donc difficile de comprendre ce que faisait ou devait faire la machine. Aujourd’hui, ils peuvent voir tout cela depuis l’ordinateur et aborder l’étape de l’exécution initiale avec plus de confiance. « Pour les pièces complexes, nous réduisons les temps de mise en route de 25 à 30 % environ, grâce à la préparation optimale des programmes, » déclare M. Richter. « La synchronisation optimale de l’usinage multiaxe permet en outre de réduire au minimum les durées d’exploitation des machines. »
Besoin de plus d'informations
UNE QUESTION SUR NOS
PRODUITS OU SOLUTIONS ?
Trouvez le point de vente le plus proche Contactez-nous Demandez un devis