15 septembre 2010

TopSolid'Cam transforme les rêves en réalité. Avec les logiciels de dessin actuels, les concepteurs disposent d’une palette d’outils pour élaborer des formes complexes. Le défi consiste toutefois à réaliser ces formes. Plusieurs conditions sont imposées aux machines, principalement au niveau de la commande et de la programmation, mais aussi au concepteur qui doit déterminer ce qui est faisable et ce qui ne l’est pas. Un logiciel de CAO performant permet d’établir un lien entre les deux et de tirer le maximum du concepteur et de la machine.
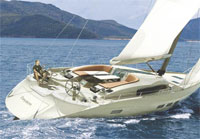
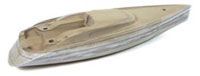
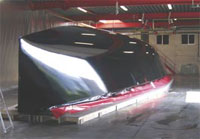
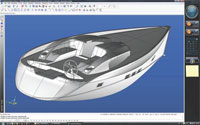
Réaliser des formes complexes en 3D implique bien souvent l’acquisition d’une machine à 5 axes. La broche avec la fraise peut se déplacer sur les axes X, Y et Z et basculer sur deux axes supplémentaires. Cela augmente l’accessibilité et permet de définir des trajets pouvant suivre des courbes complexes en trois dimensions. La définition de trajets complexes n’est pratiquement plus faisable manuellement car les interpolations classiques entre deux points ne suffisent plus. En outre, plus la complexité augmente, plus il est difficile de tenir compte de toutes les conditions périphériques, ce qui fait augmenter le risque de collisions ou d’erreurs. Un progiciel de FAO avancé répond à ces deux attentes car la conversion d’un objet dans un programme NC pour machine est automatique et tient compte des possibilités et des limites de cette machine spécifique. De ce fait, la liberté des concepteurs augmente, car la faisabilité de chaque concept peut être vérifiée à l’écran. Grâce à un système de FAO performant, on a en principe moins besoin d’une expérience de la machine car une grande expertise sur les traitements est intégrée dans le logiciel.
Ben Van Hool, fondateur de l’entreprise Zeydon à Arendonk, est un utilisateur de CAO/FAO convaincu. Fin 2004, cette entreprise s’est lancée dans la conception et la construction de yachts luxueux. Le premier prendra la mer cet été à Zeebrugge. Industrie Technique et Management s’est entretenu avec Ben Van Hool et Serge Ulrich, directeur général de 3D Ultra Surfaces, l’entreprise qui fournit le logiciel CAO/FAO TopSolid et qui encadre les nouveaux venus pour une production opérationnelle.
Intégration de la CAO et de la FAO
Ben Van Hool est le petit-fils du constructeur de bus Van Hool, il a donc l’esprit d’entreprise dans le sang mais aussi une passion pour la voile. Un autre mobile a joué un rôle crucial dans la création de Zeydon: l’entreprise voulait briller sur le plan technologique et travailler d’emblée avec des outils et de l’équipement à la pointe de la technologie. On l’a souvent entendu : pour développer une production dans notre pays, il faut se concentrer sur des produits de grande valeur. Ce raisonnement a été suivi. Le yacht de 18 mètres de long allie luxe et sportivité, et est bourré de matériaux et de technologies de pointe. La mise en forme a, elle aussi, bénéficié de toutes les attentions. Le design du yacht a été réalisé en collaboration avec Designworks USA, une filiale de BMW. Cela se voit au concept car les formes typiques des voitures de cette marque se retrouvent aussi dans le navire. Mais le design est avant tout fonctionnel car la forme extérieure détermine l’aspect intérieur du yacht. Et inversement car si le client veut apporter des modifications à l’intérieur, celles-ci auront une influence sur l’aspect extérieur, ne fut-ce que la pose de hublots par exemple. Pour mener tout cela à bien, il fallait bien plus qu’un logiciel de dessin. Les formes complexes qui peuvent être une conséquence de ce type de concept ne peuvent plus être réalisées manuellement. Il fallait donc une machine CNC et un progiciel de FAO pour transposer les formes du logiciel de dessin en un programme pour la machine.
Le choix s’est porté sur TopSolid, un progiciel permettant de concevoir tant des objets 3D que des surfaces. En soi, ce logiciel ne se distingue pas par rapport aux autres, mais lors de la sélection, il a été tenu compte de l’intégration avec le logiciel de FAO apparenté. Cette intégration permet, dès la phase de conception, d’introduire des paramètres pour la production de façon à ce que la conversion en un programme NC par le logiciel de FAO se fasse de manière rapide et efficiente.
C’est important pour l’entreprise car cela permet de discuter, d’évaluer et de modifier les concepts jusqu’au dernier moment, et de transposer les éventuelles modifications sans peine via le progiciel de FAO. 3D Ultra Surfaces a fourni un post-processeur spécialement élaboré pour la machine Thermwood de Zeydon. Un modèle 3D de la machine a également été développé de façon à pouvoir réaliser une simulation de la manière dont se passera la production sur la machine dans le logiciel. Il s’agit d’une manière efficiente de s’assurer au préalable qu’il n’y aura pas de collisions ou d’autres erreurs.
Toutes les pièces commencent sur un centre d'usinage
La Thermwood est un centre d’usinage à 5 axes d’une superficie de travail de 1,5 sur 3 mètres, et un axe Z d’un mètre. Cette machine joue un rôle crucial dans l’entreprise car toutes les formes du yacht y ont pris vie. Elle a aussi été utilisée lors de la phase de conception pour produire les premiers modèles à l’échelle. Le modèle utilisé en bassin d’essai, pour tester le comportement hydrodynamique du bateau, vient lui aussi de cette machine. Cette dernière a encore servi à la réalisation des moules de la coque, du pont et de nombreuses autres pièces du navire. Ces parties sont réalisées dans un matériau composite à base de fibres de verre, d’époxy et de mousse, avec ça et là des renforts en fibres de carbone. La mise en forme a eu lieu par injection sous vide : le matériau est apposé sec dans le moule puis recouvert d’un film et mis sous vide. De la résine est alors injectée. L’avantage de cette technologie est sa grande flexibilité pour la création de formes, et un gain de poids car la proportion de fibres dans le produit fini est de 60 %, alors que ce pourcentage est limité à 40 dans le cas du laminage. Un laminage rigide est appliqué pour les volets et autres : on enduit une forme sur un moule que l’on place ensuite sur le centre d’usinage pour obtenir la forme souhaitée avec une grande précision.
Les moules pour la coque et le pont sont réalisés par morceaux sur le centre d’usinage puis assemblés. La machine produit d’abord une forme positive sur laquelle le moule est réalisé. Viennent ensuite une soixantaine de moules pour les volets et les éléments intérieurs. Les composants métalliques sont sous-traités mais réalisés selon les concepts de Zeydon. Ici aussi, le progiciel de CAO/FAO offre des avantages car il permet de faire le travail préparatoire du sous-traitant, et donc d’avoir un contrôle maximal sur la qualité du résultat final. La mise en forme est cruciale car, pour ce yacht luxueux, c’est l’un des éléments qui lui permettra de se distinguer sur le marché. La partie hydrodynamique du bateau a été élaborée par un architecte naval, mais toutes les parties au-dessus de la ligne de flottaison et l’intérieur sont déterminants pour le prestige et le style du bateau. La manière flexible dont la conception et la production sont intégrées permet d’aller très loin.
Pour chaque détail, comme les points de raccordement pour le carburant et l’eau potable, il est possible d’élaborer des solutions élégantes et d’intégrer ces éléments dans des volets. Avec le progiciel de FAO et la fraiseuse à 5 axes, ces éléments sont pratiquement intégrés dans les moules. L’opérateur de la machine doit juste insérer un bloc et appuyer sur start.
Opérationnel en quelques semaines
La valeur du travail avec une solution de CAO/FAO s’exprime encore mieux quand on sait que Ben Van Hool, lors de la création de son entreprise, n’avait aucune expérience en techniques d’usinage. Il a découvert la machine, en fait un centre d’usinage du bois - de nombreuses formes pour les moules sont réalisées en MDF - à un salon à Paris. Quelques semaines à peine après sa livraison, les premières formes étaient fabriquées. Il faut disposer ici d’un bon post-processeur, élaboré pour cette machine spécifique. Le progiciel de FAO calcule les courbes ISO nécessaires sur base d’un concept et c’est le post-processeur qui les convertit en un code NC pour la machine, en tenant compte des possibilités précises et des limites de la machine. Etant donné que l’entreprise de Ben Van Hool est la première en Belgique à utiliser cette machine américaine, il a été demandé à 3D Ultra Surfaces de développer un post-processeur spécifique. Ce fut assez simple, par la suite, de transférer les concepts du logiciel de dessin vers la machine. Des tâches spécifiques de la technique d’usinage, comme la gestion des outils, se déroulent aisément avec ce logiciel. Pour les usinages à 5 axes, on travaille principalement avec des fraises rondes. Une fois celles-ci polies et que le diamètre ne correspond plus au diamètre originel, il suffit d’introduire les nouvelles dimensions dans le logiciel et de relancer le programme de FAO. Un nouveau programme NC est alors généré, avec de nouveaux trajets adaptés au “nouvel” outil. De la sorte, le lien entre le concept et le résultat est conservé, même si les conditions changent. Une autre tâche pour le logiciel est la gestion du Bill of Material, permettant d’importer toutes les données pertinentes des listes d’achat et d’avoir dans le logiciel un aperçu complet de tous les composants et des paramètres pertinents.
SOURCES : INDUSTRIE TECHNIQUE ET MANAGEMENT
Besoin de plus d'informations
UNE QUESTION SUR NOS
PRODUITS OU SOLUTIONS ?
Trouvez le point de vente le plus proche Contactez-nous Demandez un devis