26 september 2011
At the beginning of 2010, the Haver & Boecker machine factory, internationally renowned specialist for the filling and processing of bulk goods of all types, introduced a new AXA travelling column machining centre. The Missler software TopSolid'Cam software solution programs the 'hungry' machine, which runs in three-shift operations, with the required NC programmes. Within six months, the CAM programmers have processed more than 500 programmes for AXA.
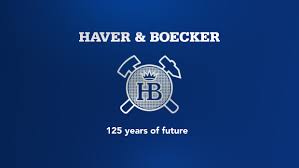
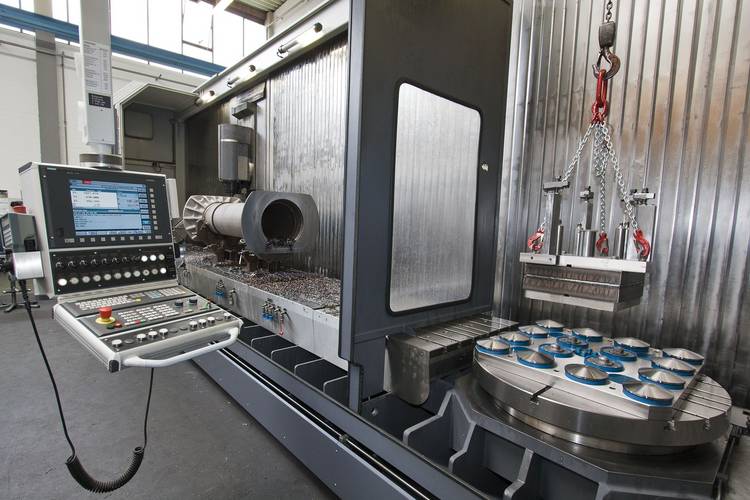
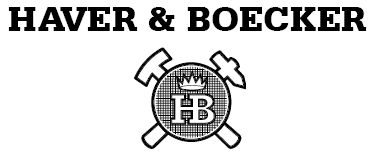
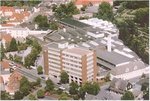
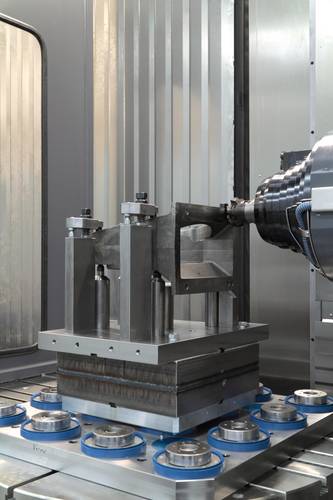
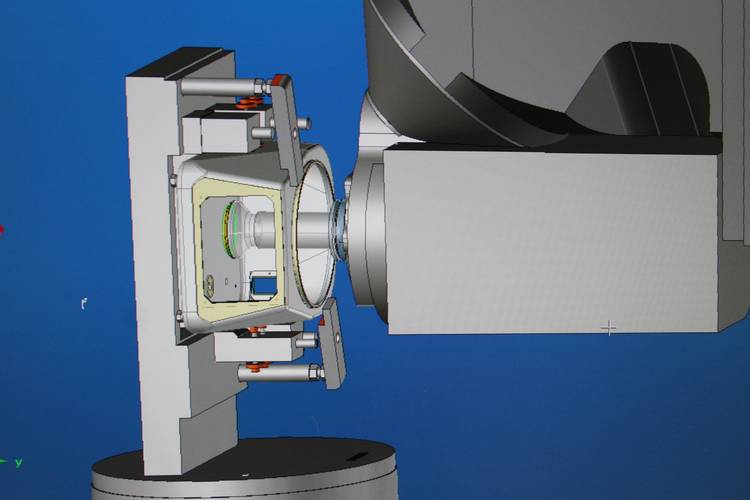
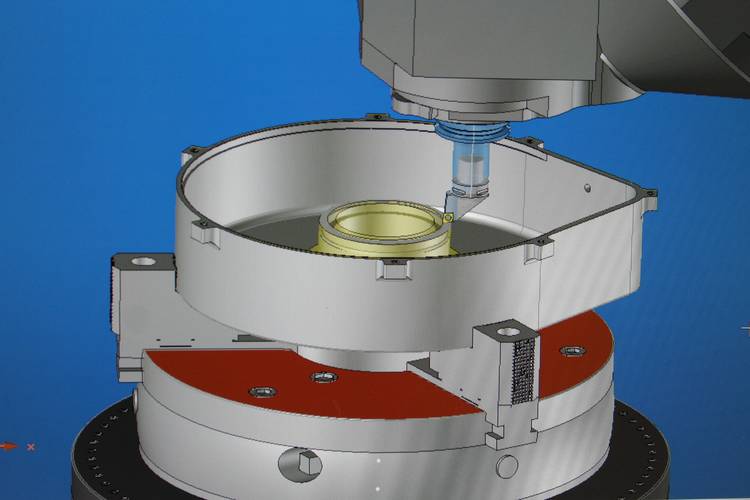
Haver & Boecker was founded in 1887 as a wire weaving company, and in 1925 began to develop packaging machines and screening machines for the raw materials industry. The group of companies is now one of the world's leading suppliers of packaging machines for valve bags or open bags, as well as FormFillSeal machines, in which cement, building materials and minerals, basic chemical and pharmaceutical materials, as well as products for the food industry, are packaged. The HAVER-ROTO-PACKER™ brought into operation in 1960, with which up to 6,000 bags of cement can be filled per hour, has become a trademark of the company. However, Haver & Boecker not only delivers individual machines, but rather as a general contractor also develops complete installations for preparation, packaging and storage of raw materials.
At present, around 2,300 employees worldwide work for the group of companies, which is head-quartered in Oelde, and is also represented by production plants in Great Britain, Belgium, USA, Canada, Brasil, China and India. By using a central, technical document management system, the employees in the international subsidiary companies access the documents from the master design in Oelde. Two years ago, Haver & Boecker began to develop a modular platform concept, in order to be able to implement client-specific or country-specific variants with less expenditure.
Developing machines and installations, which are optimally adapted to the requirements of the client or the product to be filled, is one of the strengths of the company, and one of its greatest challenges at the same time, as production manager Andreas Bauer explains: 'The bandwidths of the fillers, which we process, and the differences in terms of their flow behaviour are enormous. Even cement is not always the same. We have to closely analyse the products macroscopically and microscopically, in order to be able to offer the client the ideal filling technology for their processes'. Haver & Boecker works closely with the bag manufacturers, in order to develop innovative solutions - for example, filling cement in plastic bags, which can be stored outside.
Complete processing in pendulum operation
Haver & Boecker has a relatively high range of manufacturing. Bauer estimates that the share of internal production with a complex machine is between 50 and 60%, although laser cutting of the sheets is completely outsourced, and many components for electrics, pneumatics and automation technology are also bought. Nearly all processes from milling and boring to turning and grinding are used in machining, with milling and turning machining being the most common. In addition to the new AXA travelling column machining centre, the machine park in Oelde has several milling centres or mill turn centres by Gildemeister and Index, which normally run in three-shift operation. In order to use them at optimal capacity, Haver & Boecker prepares drive shafts and other components for companies in the region as a commission order, which also includes the CAD technical preparation of the parts to be manufactured and the CAM programming.
The purchase of the AXA machining centre for longbed and pendulum machining was a replacement investment for a 19 year old vertical machine, which indeed already allowed pendulum operation, but was no longer state of the art in terms of machining possibilities. For shaft production, the partition always had to be dismantled, which limited the pendulum and caused downtimes. AXA was recommended as an alternative due to its modular machining concept and the willingness of the manufacturer to adapt it to the requirements of Haver & Boecker, such as the zero-point clamping systems and the work pieces to be machined.
The new machining centre is dimensioned in such a way that the shafts, which are up to four metres long, can be machined vertically and on the front with the NC swivel head on the left, and complex series parts can be milled and turned in pendulum operation on the rotary table with torque drive in the right machining area. The store offers space for 150 SK50-mills and 36 turning tools, and can also be disconnected and retooled in parallel to the running time. 'For us, everything is designed for minimising the set-up times', says Frank Hegemann, director or pre-production. 'With the new AXA, we can completely machine complex parts in pendulum operation, which reduces the processing time and improves the quality.'
Good support for turning machining
Minimising the set-up times plays an important role in production, since many different components in small batch sizes are to be machined. Reliable NC programmes are a pre-requisite for this. The company therefore needed a CAM system – allowing the machining in the machining area, with the clamping situation and the tools used – to be simulated on the computer: 'We often have to retool the machines in a sheet five or six times. Then we lose a lot of time if there are programming errors', Bauer explains. 'In order to get to the machine as quickly as possible, we wanted to exactly represent all contours and our zero-point clamping system in the CAM system'.
These requirements could not be met with the old 2D programming system, which is why the decision was made three years ago to change to a 3D-capable CAM system. The deciding factor for the choice of the TopSolid'Cam software was the fact that it supports the programming of both milling and turning machining. Most of the eligible systems failed on this point, as asserted by CAM programmer Wolfgang Frenz. 'We provided a sample portion to Moldtech, a TopSolid reseller in Germany, and were quite impressed how quickly it solved the problem with TopSolid. The import of the Solid Edge data in the STEP format was also excellent.'
The strong CAD functions in TopSolid’Cam was another strong point of the software. Having CAD functionalities in the CAM software chosen was important for Haver & Boecker, as their clients in contract manufacturing often do not provide 3D data. In order to be able to programme the NC machining, the employees in work preparation first have to 3D-model the components to be machined. Sub-contracted parts such as the drive shafts, which often appear in similar form, have been consistently parametrised, so that they can be changed by input of small measurements. 'If I amend the diagram or the model, the relevant NC programme automatically adapts due to associativity'. Frenz explains the advantages of the procedure, which Haver & Boecker also use for in-house families of parts, in order to speed up the preparation of the NC programmes.
TopSolid'Cam is currently running in three workplaces of Haver & Boecker. Sales partner Moldtech installed the software, programmed the post-processors and supported the users in the connection of the machine park. The four CAM programmers of the company had a week of training on using the new CAM system in the system house in Salzkotten, and in the event of questions and problems, can always rely on the support of the hotline-employees at Moldtech, who can access their computers via Netviewer if necessary, in order to demonstrate the solution to the problem. Frenz praises the online support, which works very well.
After a few days of training, CAM programmers were in the position to produce the first executable NC programmes. 'What one learns gradually at first, of course, is to develop a uniform operation. We all try to programme in the same way, so that colleagues can easily change our programmes', says Wolfgang Frenz, who does not feel that the move to TopSolid'Cam was difficult: 'On the contrary. When machining complex work pieces, we never knew in 2D exactly where you were positioned in the area, and also had no control over the chip removal. The tracking of the raw part is much easier than before as it is standard for all clamping and machines.
Programming on the virtual machine
In contrast to other CAM systems, the user generates his NC programmes with TopSolid'Cam in a virtual machine environment. Since 3D models were not available for all existing machines, the CAM programmers had to partly gather them in the workshop. Moldtech then modelled the machines in 3D and also displayed the kinematics in the models. The connection of the new machining centre was simpler, since AXA and Moldtech worked well together from the beginning. The machine manufacturer prepared the 3D model so that Moldtech could optimally display the kinematics. Even before delivery of the machine, the German reseller provided a base post-processor, so that AXA could check whether the turning and milling operations were correctly rendered in machine code.
The post-processor then of course has to be adapted to the machine-specific conditions, particularly concerning the limitation of the 5-axis-machining in the right working area. 'Due to the pendulum wall, the head can only completely swing in one direction, so the machining on the opposite side must be controlled by turning the rotary table', explains Hegeman, who is very satisfied with the support of the partner: 'We have never before brought a machine into operation so quickly. We were able to start production four weeks after delivery.'
In order to be able to programme the NC machining more quickly and to simulate reliably, Haver & Boecker displayed not only the machines, but also the clamping system and tools one-to-one in the CAM system. The bench vices are completely parametrised with reference to the zero-point clamping system, in order to be able to represent all clamping situations by inputting just a few parameters. For each machine, Wolfgang Frenz has defined 10 to 15 models with standard clampings: 'When I clamp the work piece to the machine, the system asks me which model I want to use, and where the work piece should be clamped. Providing all of this has taken some time, but an enormous amount of time is now saved in programming.' The user can also programme his machining with TopSolid'Cam without clamping, for example, when depicting the clamping situation would be unnecessary effort.
Haver & Boecker intensively uses the tool management system TopSolid'Tool, which meanwhile contains 1,500 to 2,000 parametrically built tools. The CAM programmers do not only incorporate the tools into the database, but also downloads and extensions. The complete tools are compiled from the individual components, in the way that they are required for the respective machining. Due to corresponding filter functions, during the NC programming they only see the tools, which can be used in the respective machine, provided that they are not already default scaffolded. The material-specific cutting data is provided in TopSolid'Tool for the different machining strategies. If the operator of the machine adjusts anything during machining, he reports back to the CAM programmers, who immediately update the NC programme. This ensures that in a new programme call, for example, after a design modification, the current cutting data is always used.
Improving process reliability
Due to the continual display of machines, clamping systems and tools in TopSolid'Cam, programming times at Haver & Boecker have considerably reduced. 'Depending on the complexity of the work piece, we are certainly 50% quicker', says Frenz. It is equally important that the process reliability has considerably improved due to the possibility of visualising and simulating the machining on the computer. It is therefore quicker to bring in new NC programmes. During machining, the machine operators possibly change the speed or the feed rate from time to time, but the calculated tool paths are correct. Using the adjustment sheet, they detect whether a work piece is running on the machine for the first time, and whether the change statuses of the NC programme and diagram match.
Bauer thinks that further time savings are possible in the process, if current and new components can be further unified in construction terms, so that they can be machined with fewer special tools. However, Bauer still sees potential to improve production: 'We have established efficient 5-axis technology, an optimal CAM system, and a good data bank in the business. Now the task is to further improve the machine environment and the logistics processes. A first step in this direction was the creation of a new set-up area, on which tools, measuring equipment and devices are centrally prepared for the next task. The aim is to have a 'view buffer' of tasks on each machine, so that they can be quickly retooled with the lowest possible waiting times and preparation times'.
Meer informatie nodig
EEN VRAAG OVER ONZE PRODUCTEN OF OPLOSSINGEN?
Vind uw dichtstbijzijnde verkooppuntContacteer onsVraag een offerte aan