24 april 2017
This French SME is a preferred partner of the leading players in the aerospace industry, and has been supporting all of their manufacturing programs for more than 20 years. The company meets the stringent productivity and quality imperatives by using powerful tools, such as TopSolid'Design and TopSolid'Cam, which feature advanced functions to speed up the programming of machining operations.
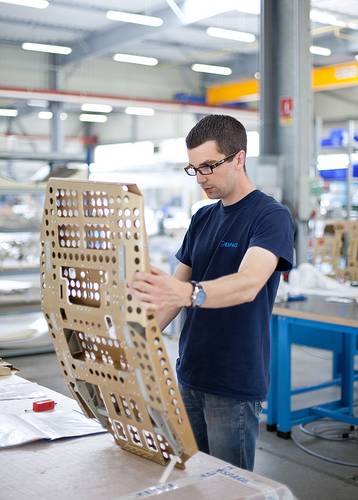
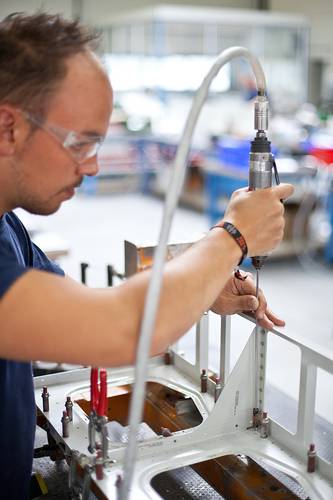
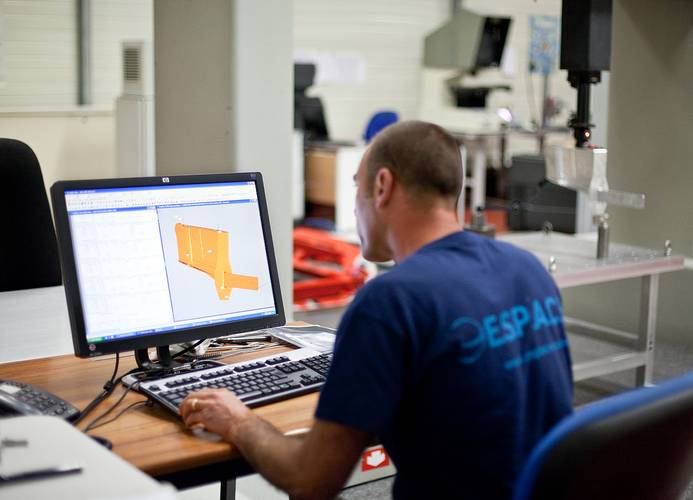
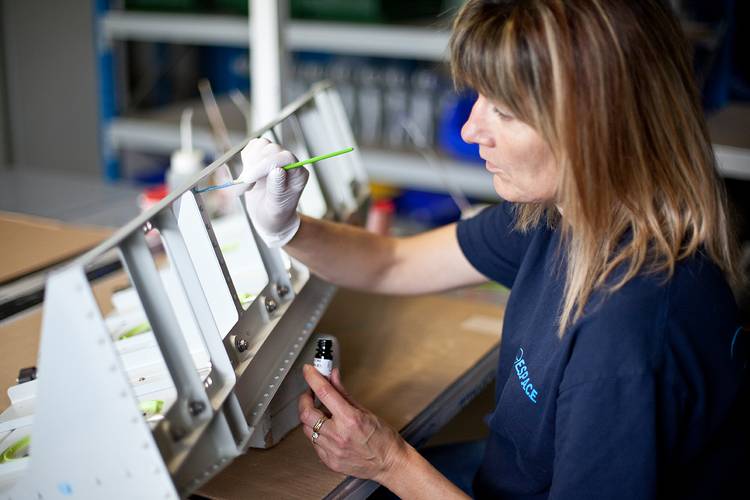
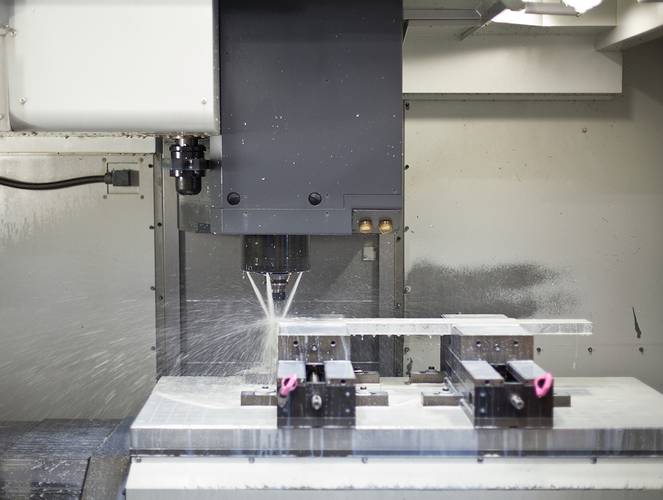
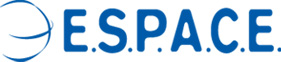
E.S.P.A.C.E has been active in the aerospace manufacturing sector for more than 25 years, working with prestigious names such as Airbus, Safran, Latécoère and Stelia Aerospace. These customers, plu smany others, rely on E.S.P.A.C.E's specialists to manufacture complex sub-assemblis, mechanical parts and sheet metal parts for airframes and aircraft interiors. Its plants also produce urgent parts, avionic supports and electrical units. Every day, the company calls on its wealth of skills and know-how in its production plants located close to the hubs of the French aerospace industry in Saint-André-Des-Eaux near Saint-Nazaire and Muret near Toulouse.
In 2010, the company set up its subsidiary 2AS (Ateliers Aéronautique du Sahel) in Jemmel, Tunisia. "Our primary objective is to meet the demands of our customers by proposing manufacturing solutions tailored to their needs," explains Alain Ganne, the company's Production Engineering and Programming Manager. The activities in the three plants are guided by a focus on productivity and quality, and the copany does everything in its power to meet the demanding specifications. Thanks to its specialized human and material resources, E.S.P.A.C.E has become an expert in precision machining, including three- and five axis milling, fine sheet metal work, TIG welding, and the assembly of sub-assemblies. "For example, we have a strong command of numerous special processes for the Airbus programs, such as ADET / AIPI-AIPS for airframes," explains the specialist.
"Our production activity is organized into dedicated teams and lines that guarantee the flexibility inherently required in aerospace projects. In this way, we can easily switch from the manufacture of parts to series production runs of the production of complex sub-assemblies." Nothing is left to chance in the machining of mechanical parts, thanks to the powerful TopSolid'Cam programming software. "Our customers send us the CAD files of the parts to be machined, and then we program the operations using Missler Software's TopSolid software. We have been using this solution for 14 years, and we recently upgraded to version 7, which features numerous smart functions," continues Alain Ganne. "Lightalloy and hard metal parts (stainless steel and titanium) are machined with three-and five axis milling machines (Mori Seiki, Haas, Hurco) that meet a broad range of needs, from ultra-high precision parts to less demanding production operations." According to this expert in machining, the deployment of Missler Software's solution has amde the machining programming processes significantly more responsive. Tights production deadlines for machined parts can be met in just a few days (usually five to ten days), depending on their complexity. "TopSolid'Cam offers a number of benefits, including its capacity to quickly create machining paths by strategy propagation, which allows for short cycles. It also enables us to build on our know-how. Machining procedures can now be reproduced for similar parts. This saves time and increases profitability," notes the E.S.P.A.C.E Production Engineering and Programming Manager.
The programmers' jobs are also meade easier thanks to the management of tolerances with FreeShape and the comprehensive libraries of cutting tools and conditions. Simple, intuitive and scalable, TopSolid can provide operators with machining programs that make it easier to control even the most sophisticated machines. The software also includes a machining simulation module that features a preview of the tool paths. The tool also manages all inter-operation movements, possible collisions, the travel of each axis, and remaining materials. These features cut the time spent fine-tuning. "This comes in very handy for high added-value parts and/or urgent orders," adds Alain Ganne. With its native interoperability, TopSolid also protects the company's machining databases, thanks to its integrated product data management (PDM) system. "We are now able to keep our production history, which is an indispensable asset in aerospace production operations," enthuses the engineer. The successful collaboration with Missler Software's local branch based in Nantes is another reason why the production engineering specialists at E.S.P.A.C.E are so satisfied. "We communicate frequently and our quest for machining excellence is helped by listening closely to one another," confirms Alain Ganne. "One example is the installation of high-performance post processors that are adapted and customized for our machines in collaboration with the specialists from the local branch." This collaboration may well be extended to include other activities. Constantly on the lookout for new solutions, E.S.P.A.C.E uses additive manufacturing to produce certain parts. As part of the C-FAST project, Missler Software is also working with the CIRTES on the development of a hardware and software offer dedicated to additive manufacturing within the next three years. It will use the CIRTES Straoconception process and Missler Software's TopSolid CAD/CAM software, specially adapted to this process, to manufacture large parts. Wait and see...
The strong point of the TopSolid application at E.S.P.A.C.E:
- The conservation of the machining databases thanks to the integrated production data management (PDM) system
- Reuse of programming know-how
- Machining simulation to minimize program development cycles
- Fruitful and permanent dialog with Missler Software's local specialist
Alain Ganne's conclusions: "TopSolid'Cam's capacity to quickly generate machining paths, and the ability to build on our programmers' know-how, boost productivity, and imprive quality. These are essential targets in aerospace manufacturing."
E.S.P.A.C.E in figures
More than 25 years of activity in the aerospace industry
2016 turnover: €28.7 million
Total headcount: 330
Three manufacturing plants: two in France, in Saint-André-des-Eaux near Saint-Nazaire and Muret near Toulouse, and one plant in Jemmel, Tunisia. Production is organised by product line, with the corresponding targets and indicators. The company implements visual management in all its production workshops in an effort to involve every single employee in this organization. Every employee knows and respects the product lines. The two sites in France are linked by an SDSL line to share IT resources (ERP Hélios, Accounting, Action Tracker) and communications resources (integrated telephony, webcam and videoconferencing networks).
Meer informatie nodig
EEN VRAAG OVER ONZE PRODUCTEN OF OPLOSSINGEN?
Vind uw dichtstbijzijnde verkooppuntContacteer onsVraag een offerte aan