15 september 2010
CAM package brings a dream to life. With modern drawing packages, designers have a lot of tools at their disposal to design complex shapes. But the challenge is also to manufacture these effectively. This imposes a number of conditions relating to the machines, especially regarding control and programming, but also to the designer, because he needs to be able to ascertain what is attainable, and what is not. High performance CAM software links these conditions, and gets the maximum from both the designers and the machines.

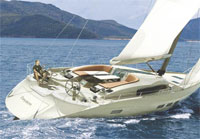
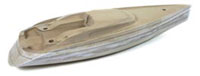
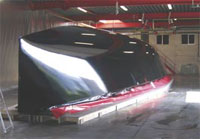
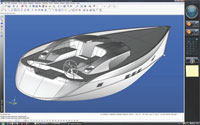
To make complex shapes in 3D often requires a 5 spindle machine. That means that the spindle with the milling head can not only move in the X, Y- and Z-axis, but can also tilt in two additional axes. This increases the accessibility and one can define more advanced milling paths, which follow complex curves in three dimensions. However, defining complex paths is something that can hardly be done manually, because normal interpolations between two points are no longer sufficient. Moreover, as the complexity increases, it also becomes more difficult to take all limiting conditions into account, so that the risk of collisions or other errors increases. A sophisticated CAM package meets both cases, because the conversion of a design in an NC programme for the machine, takes place automatically, taking into account the possibilities and limitations of that specific machine. Because of this, the designer's freedom increases, because the feasibility of each design may already be verified on the computer screen. With a high performance CAM system, one needs, at least in theory, less machine experience, because a lot of knowledge about tooling has been integrated in the software.
A convinced CAD/CAM user is Ben Van Hool, founder of the company Zeydon in Arendonk. The company started at the end of 2004 with designing and building a series of luxurious yachts. The first yacht will be launched in Zeebrugge during the summer (2008). Industrie Technisch Mana-gement interviewed Ben Van Hool and Serge Ulrich, general manager of 3D Ultra Surfaces, who supplied the CAD/CAM software TopSolid, and guided the newcomers in the business to an operational production.
Integrated CAD/CAM
Ben Van Hool is a grandson of the well-known bus builder Van Hool, so a certain entrepreneurship is already in his blood, just as a passion for yachting is. When founding the company Zeydon, there was an additional motive which would play a crucial role: the company wanted to excel in technology, in working with advanced means and tools from the outset. It is often said in Holland that anyone who wants to produce in our country has to specialise in high-quality products, and this reasoning was followed in the case of Zeydon. The 18 meter long yacht combines luxury and sport, and is full of high-quality materials and technologies. Also the boat design is of the highest quality. The boat was designed in cooperation with the company Designworks USA, a subsidiary company of BMW. This cooperation may be seen from the boat design, because the typical shapes of cars can also be recognised in the hull of the boat. Yet the design is functional to start with, because the outside shape determines also how the ship looks at the inside. And the other way round, because when the customer wants certain The boat was designed in cooperation with the company Designworks USA, a subsidiary company of BMW.
With this the choice fell on TopSolid, a package with which one may both design 3D objects and surfaces. In itself the software does not distinguish itself from other packages, but what was essential in the choice of this software solution was the complete integration with the accompanying CAM software. This integration implies that one may already provide parameters for the production phase in the design phase, so that the conversion into an NC programme happens very fast and efficiently by the CAM software.
This is important for the company, because one may discuss, evaluate and adjust designs until the last moment, at which possible changes are included in the conversion without additional efforts by the CAM package. In addition to supplying the CAD/CAM package 3D Ultra Surfaces, a TopSolid reseller in Belgium, took care of a post-processor which was specifically written for Zeydon’s Thermwood machine. The reseller also provided a 3D model of the machine, in order to be able to do a simulation in the software of the way the production will elapse on the machine. This is an efficient way to check in advance that no collisions or other errors will occur.
All parts start at the processing centre
The Thermwood machine is a 5 spindle processing centre with a processing surface of 1.5 by 3 meters, with a Z-axis of 1 meter. The machine plays a crucial role in the company, because all shapes of the boat are brought to life with it. The machine was used to produce the first scale models in the design phase. Also the model that was used in the tank test, to test the hydro-dynamical behaviour of the boat, comes from the machine. But it also serves to make the moulds with which the hull, the deck and numerous other parts of the boat are produced. These parts are made of a composite material from fibre glass, epoxy and foam, with here and there reinforce-ments from carbon fibre, which is shaped by vacuum injection. This means that the material is applied to the mould in dry form. After this the material is covered with foil and a vacuum is created at which resin in injected. The advantage of this technology is a big flexibility in creating shapes and weight saving, because the portion of fibre in the final material may amount to 60 percent, while this is limited to 40 percent with hard laminating. Hard laminating is applied with hatches and the like, where one plasters a shape onto a mould, and places it on the processing centre afterwards, to get the desired shape with high accuracy.
The moulds for the hull and deck have been made at the processing centre in pieces, and joined together afterwards. The machine first makes a positive shape, on which the actual mould is made. Besides that, there are 60 additional moulds for hatches and interior parts. Metal parts are outsourced, but are also made in accordance with designs from Zeydon. The CAD/CAM package offers also advantages here, because one can do the preliminary work of the supplier by oneself and thus have maximum control over the quality of the final result. With this the design is crucial because it is one of the points at which the luxurious yacht may distinguish itself on the market. The hydro-dynamic part of the boat was designed by a ship architect, but all parts above the water line and the interior are decisive for the style and prestige of the boat. The flexible way in which design and production have been integrated means that one can go very far in terms of design.
One can develop elegant solutions for every detail, like the connections for fuel and fresh water, at which these elements are integrated into hatches or sinkings. Because of the CAM package and the 5 spindle milling machine, these elements are included in the moulds almost automatically. The machine operator shall only put on a block and press on start.
The TopSolid allow you to enter all production parameters in the design phase, so that the processing into a NC programme is carried out fast and efficiently.
Already in production after a few weeks
The value of working with CAD/CAM can clearly be seen by the fact that Ben Van Hool did not have any experience with machining techniques when he set up his company. He saw the machine, which is actually a wood working machine– many shapes for the moulds are made in MDF – at an exhibition in Paris. Within a few weeks after delivery the first shapes were produced on the machine. For that one needs a good post processor, written for this specific machine. The CAM package calculates the necessary ISO curves based on a design. It is the post processor which converts these into an NC code for the machine, taking into account the precise possibilities and limitations of the machine. Since the company is the first Belgian user of this American machine, the choice was made to have their own post processor developed by 3D Ultra Surfaces. Then it was quite simple to convert designs from the drawing packages to the machine. Also specific tasks from the machining technology, like tool management, elapse quite smoothly with this software. For 5 spindle tooling mostly round cutters are used. When these have been sharpened and the diameter is not exactly in accordance with the original, it suffices to enter the new dimensions into the software and run the CAM programme again. Then a new NC programme is generated, with new milling paths, adjusted to the “new” tool. This way the link between design and result is always maintained, also under changing circumstances. A next task for the software is managing the Bill of Material, so that one can also import the relevant data from all bought parts, and may have a complete overview in the software of all components and the relevant parameters.
SOURCES: INDUSTRIE TECHNIQUE ET MANAGEMENT APRIL 2008
Meer informatie nodig
EEN VRAAG OVER ONZE PRODUCTEN OF OPLOSSINGEN?
Vind uw dichtstbijzijnde verkooppuntContacteer onsVraag een offerte aan