21 april 2021
Specialized in custom-made production of joinery and complex fittings from A to Z, this young SME uses a design-manufacturing chain that favors flexibility, reactivity and productivity. Quality manufacturing, one of the assets of which is the TopSolid'Wood CAD/CAM (computer-aided design and manufacturing) software from TOPSOLID SAS.
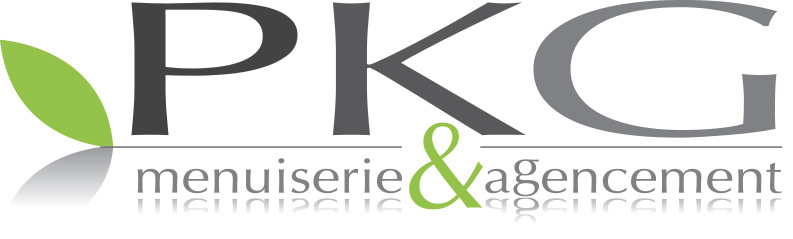
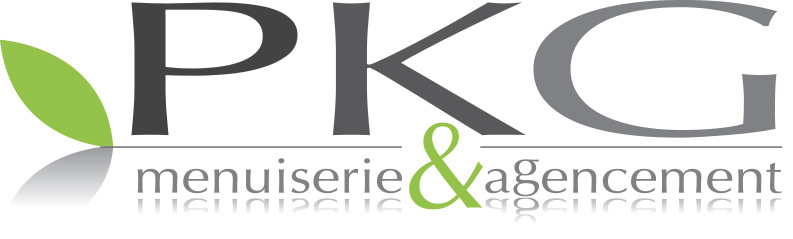
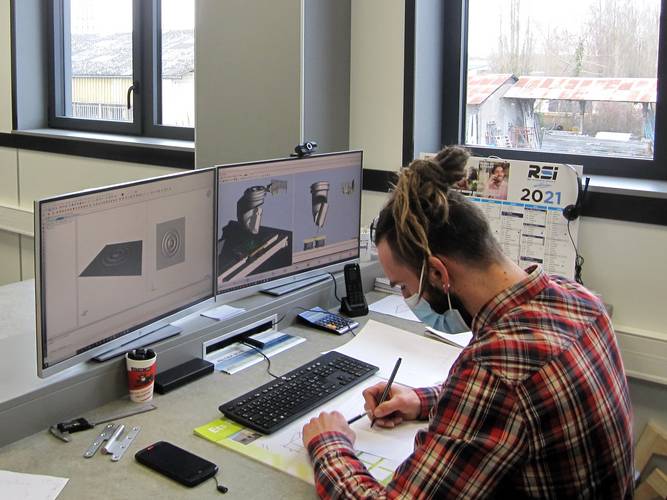
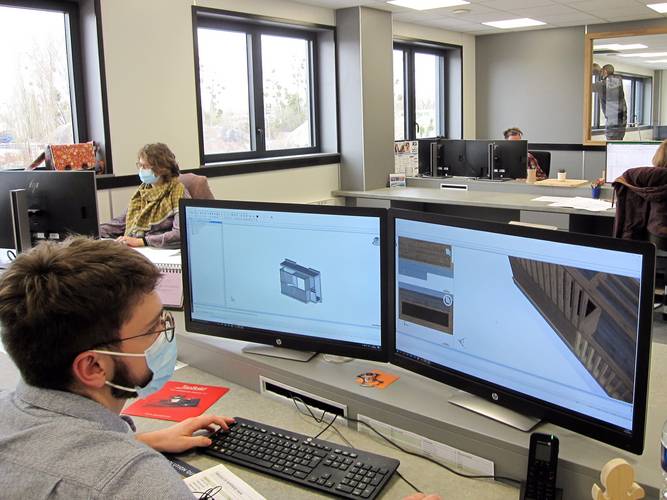
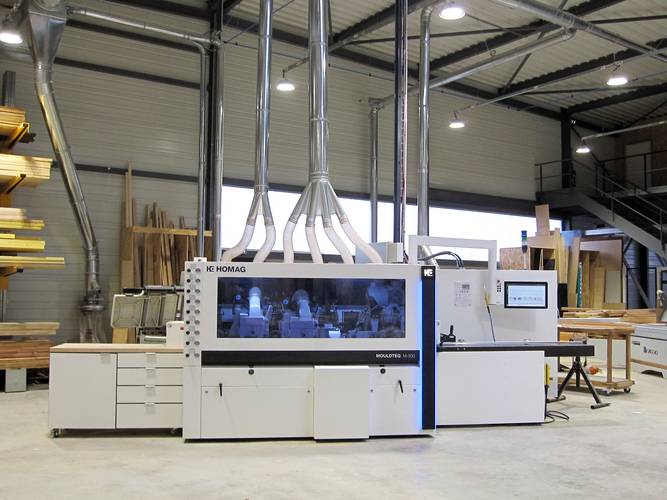
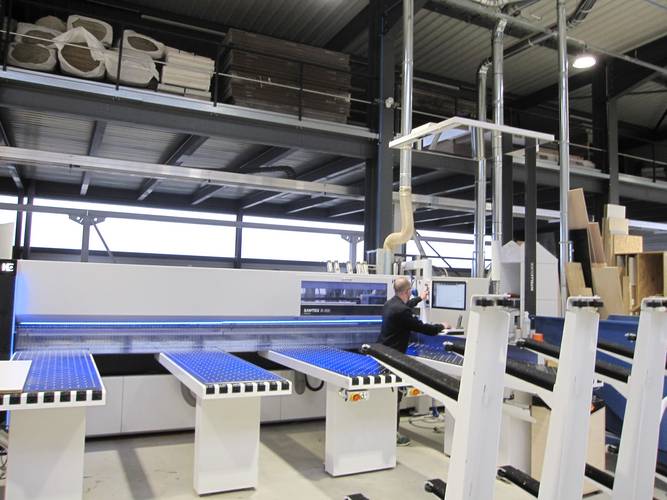
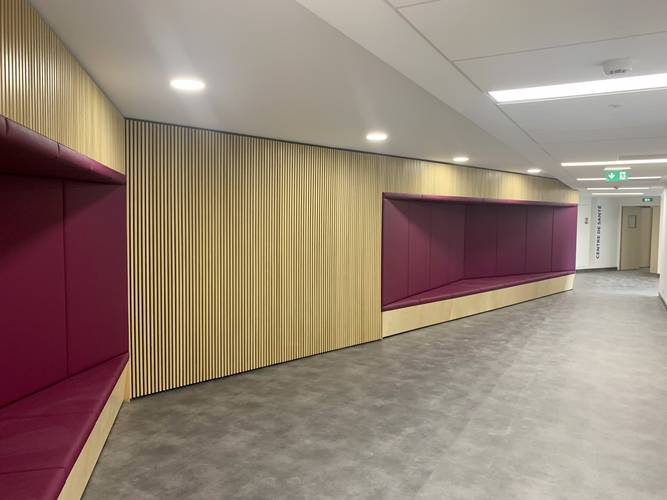
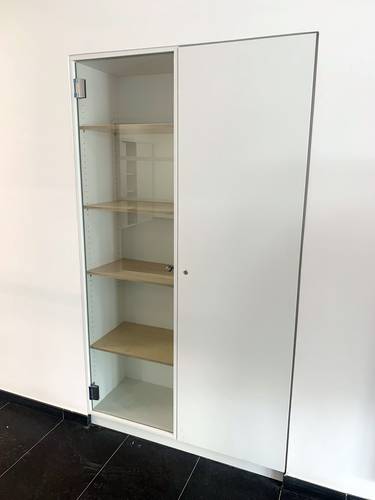
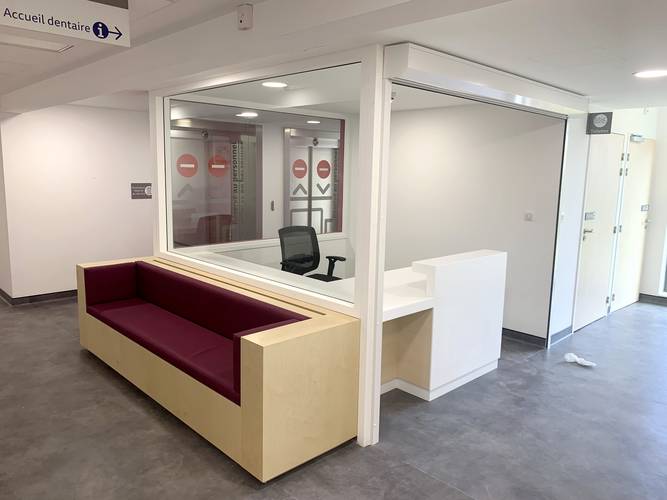
Located in the industrial area of a small village in the Oise region, more precisely in Pontpoint, France, PKG has nothing to envy the big companies for, which are launched on the road to the factory of the future. "I created the company seven years ago, but in 2019 we moved to a new building," says Pierrick Kerboriou, manager of this SME that employs 19 people. "This allowed us to rethink and realize a design and manufacturing solution adapted to our workflow." In his large, environmentally friendly workshop, which is so well insulated that the heat released from the machines is enough to keep it adequately cool, the wooden parts circuits run smoothly. Solid wood and chipboard products for the various construction sites of its high-level clients are designed and manufactured here in a way that is a real case study. These are real partnerships because PKG specialists participate with their know-how in the genesis of each project. "Three years ago, after a study of existing CAD/CAM solutions on the market, we chose the TopSolid'Wood software from the French publisher of the same name," explains Denis Gianessi, head of the design office. "A user-friendly tool that stands out for its versatility. Indeed, our projects include technical furniture, wall detailings and acoustic treatments that use different materials (metal, glass, wood). Like the elements proposed for the renovation of a private mansion that now houses the Chinese embassy or the luxury boutiques of Place Vendôme in Paris.”
Virtually limitless 3D modeling
TopSolid'Wood is the central element of the solution implemented by PKG and it ensures the design of the most complex applications, models them and creates the virtual views of the future project. This is not the only advantage of this tool, which also ensures the management of technical data of the project, the necessary components as well as the management of the stock of the panels to be machined. A feat made possible by the software's virtually limitless 3D modeling. Very powerful, the parametric modeler of the software implements a multitude of functions that facilitate the work of the designer: modeling several parts and sub-assemblies in the same file, the realization of assemblies by reassembly to structure the projects at its convenience or the predefined positioning of parts with the detection of possible collisions.
In addition, intelligent components (processes, drivers, interchangeability, articulation, etc.) are also available to the designer. He can therefore choose those that are most suitable for his project.
As soon as the design of the future project is completed, the machining program created with TopSolid'WoodCam is automatically transferred to the flexible cell installed in the workshop. This ultra-modern facility includes several numerically controlled machines from the German manufacturer Homag (panel saws, machining centers, etc.) served by a robot, which makes it possible to manufacture parts from A to Z. "At first glance, the process may seem simple," explains Pierrick Kerboriou, a young entrepreneur who worked in other woodworking workshops before embarking on this technological adventure. "But you have to be extremely thorough during the design process, because once the machining program is sent to the manufacturing cell, the work is done almost automatically." Therefore, the robot searches for the parts, marked with a QR code depending on the project, in the stores to transport them to the appropriate machine. In fact, operators are rarely involved in this stage of the manufacturing process. "You need experienced designers to take full advantage of the potential of a tool like TopSolid'Wood," insists the PKG manager.
The magic of digital technology allows a two-way dialogue between the workshop and the design office. "Sometimes we use certain manufacturing files in the design of a new project," the specialist points out.
The icing on the cake is that the software automatically calculates machining times and provides indicative information that can help with costing. "This reduces work time and cuts production costs," concludes Pierrick Kerboriou. Once manufactured, the furniture is assembled on site by one of the company's five teams for final validation.
Advantages of the TopSolid'Wood application at PKG
- Detailed modeling of complex applications
- Optional integrated realistic rendering that allows a virtual visualization of the project
- Reliable and precise execution of the machining program for the Homag flexible manufacturing cell
- Close partnership with TopSolid SAS specialists (Paris for training, Toulouse for design, Lyon for CAM)
Pierrick Kerboriou's opinion: "With its powerful configuration capacity, TopSolid'Wood software combines versatility, user-friendliness and efficiency. Its multitude of functions makes the designer's job easier."
PKG in short
Creation of the company: 2013
2020 turnover: €4,586K
Staff: 19 people
€850K investment in the Homag flexible manufacturing cell
Meer informatie nodig
EEN VRAAG OVER ONZE PRODUCTEN OF OPLOSSINGEN?
Vind uw dichtstbijzijnde verkooppuntContacteer onsVraag een offerte aan