21 maart 2011
A guarantee of exceptional part surfaces and calculation speeds
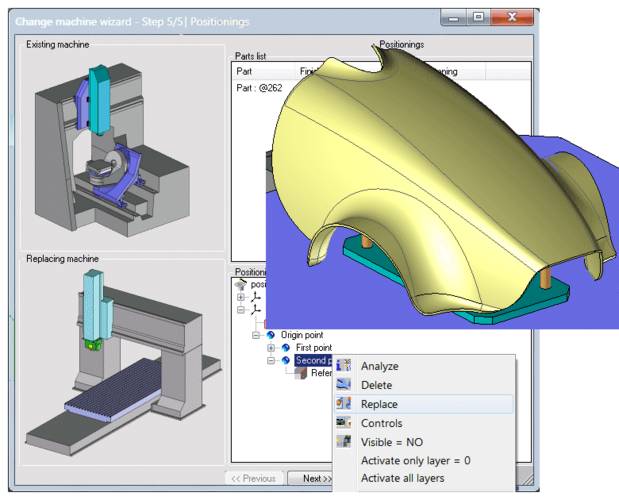
Missler Software will launch the latest version of its Cam software solution, TopSolid’Cam 2011 this month. TopSolid’Cam is a Cam solution which calculates tool paths for numerically controlled machines including milling machines, lathes and machining centres. The latest version of TopSolid’Cam has many new functions for all its customers with a special focus on the tool making and the aerospace industries. TopSolid’Cam 2011 promises excellent part surface quality and unbeatable machining times thanks to such new functions as morphing, machine replacement, Z level helical machining and Z level finishing cycles.
Morphing
Morphing is a 3D operation which creates a tool path on a part (without any underdraft) from 2 curves (opened or closed). The idea is to deform the exterior curve right into the interior curve by using, where desired and/or required, intermediary curves. The resulting tool path is one continuous helical tool path that maintains scallop height as it goes. This means that there is only one entry move and one exit move. This new function in TopSolid’Cam 2011 greatly improves the surface quality of parts thanks to the use of only one tool path which stays in constant contact with the material (thereby avoiding jumps which deteriorate surface quality). 3D morphing also permits significant time gains by greatly reducing, or even eliminating, the need to polish parts.
Machine replacement
A new wizard allows the operator to replace the machine being used with another – there are no limitations concerning the new machine or its kinematics. Any operations which are not possible on the replacement machine are inactivated.
This new function offers huge time gains for workshop managers who can, for example, replace a Mill Turn machine with a lathe or a milling machine, an underused 5 axis machine with a 3 axis machine, etc. In addition the possibility to change machine offers great flexibility to fully exploit the potential of all machines present in the workshop.
Z level helical machining
Z level helical machining allows constant contact between the tool and the material. The principal advantage of this new function is the possibility it offers to prevent “sewing marks” caused by multiple entry and exit moves. This translates into superior surface quality in parts.
Z level finishing cycles
Pockets, commonly found in aerospace parts, often have very thin and fragile walls. TopSolid’Cam 2011 allows the operator to carry out finishing operations on these walls using Z level cycles regardless of the pocket depth. Such cycles help prevent unnecessary weakening of the already thin walls and reduce significantly programming times. In addition multi-pocketing allows the automatic running of processes on faces detected and selected by the operator which enables faster machining times.
Meer informatie nodig
EEN VRAAG OVER ONZE PRODUCTEN OF OPLOSSINGEN?
Vind uw dichtstbijzijnde verkooppuntContacteer onsVraag een offerte aan